Курсовая работа: Спроектировать ректификационную установку для разделения бензол – толуол
Курсовая работа: Спроектировать ректификационную установку для разделения бензол – толуол
ФЕДЕРАЛЬНОЕ АГЕНТСТВО ПО ОБРАЗОВАНИЮ
АНГАРСКАЯ ГОСУДАРСТВЕННАЯ ТЕХНИЧЕСКАЯ
АКАДЕМИЯ
КАФЕДРА МАШИН И АППАРАТОВ ХИМИЧЕСКИХ
ПРОИЗВОДСТВ
КУРСОВОЕ ПРОЕКТИРОВАНИЕ
по процессам и аппаратам химической
технологии на тему:
«Спроектировать ректификационную
установку для разделения
бензол – толуол»
Проектировал студент
гр. Мху – 06 – 1
Руководитель
проекта
Подоплелов Е.
В.
Ангарск, 2009
СОДЕРЖАНИЕ
1 ТЕХНОЛОГИЧЕСКАЯ СХЕМА
2 ТЕХНОЛОГИЧЕСКИЙ РАСЧЕТ АППАРАТА
2.1 Материальный баланс колонны
2.2 Пересчет массовых долей
2.3 Расчет рабочего флегмового числа
2.4 Расчет физико-химических параметров процесса колонны
2.5 Определение диаметра колонны
2.6 Определение тангенса угла наклона
2.7 Определение высоты колонны
2.8 Гидравлический расчет колонны
2.9 Расчет патрубков
2.10 Расчет кипятильника
СПИСОК
ЛИТЕРАТУРЫ
1
ТЕХНОЛОГИЧЕСКАЯ СХЕМА
Ректификация – частичное или полное разделение
гомогенных жидких смесей на компоненты в результате различия их летучести и
противоточного взаимодействия жидкости, получаемой при конденсации паров, и
пара, образующегося при перегонке.
Ректификация широко
распространена в химической технологии и применяется для получения
разнообразных продуктов в чистом виде, а также для разделения газовых смесей
после их сжижения (разделение воздуха на кислород и азот, разделение
углеводородных газов и др.).
Процесс ректификации не
применяется при разделении чувствительных к повышенным температурам веществ,
при извлечении ценных продуктов или вредных примесей из сильно разбавленных
растворов, разделении смесей близкокипящих компонентов.
Технологическая схема
процесса ректификации представленная на рис.1.
Исходную смесь из
промежуточной емкости-1 центробежным насосом-2 подают в теплообменник-3, где подогревают
до температуры кипения и подают в колонну на ту тарелку, где кипит смесь того
же состава хF, т.е. на
верхнюю тарелку нижней исчерпывающей части колонны. Верхняя часть колонны
называется укрепляющей по легколетучему компоненту.
Внутри ректификационной
колонны-4 расположены контактные устройства в виде тарелок или насадки. Снизу
вверх по колонне движется пар, поступающий из выносного куба – испарителя (кипятильника)-5
(куб – испаритель может размещаться и непосредственно под колонной). На каждой тарелки
происходит частичная конденсация пара труднолетучего компонента и за счет
конденсации – частичное испарение легколетучего компонента. Начальный состав
пара примерно равен составу кубового остатка хW, т.е. обеднен легколетучим компонентом. Таким образом,
пар, выходящий из куба – испарителя и представляющий собой почти чистый
труднолетучий компонент, по мере движения вверх обогащается легколетучим
компонентом и покидает колонну в виде почти чистого пара легколетучего
компонента. Для полного обогащения верхнюю часть колонны орошают в соответствии
с заданным флегмовым числом жидкостью (флегмой) состава хР,
получаемой в дефлегматоре-6 путем конденсации пара, выходящего из колонны. Пар
конденсируется в дефлегматоре, охлаждаемом водой. Часть конденсата выводится из
дефлегматора в виде готового продукта разделения – дистиллята, который
охлаждается в теплообменнике-7 и направляется в промежуточную емкость-8. Флегма,
стекая по колонне и взаимодействуя с паром, обогащается труднолетучим
компонентом.
Из куба – испарителя отводят
нижний продукт или кубовый остаток.
Из кубовой
части колонны насосом-9 непрерывно выводится кубовая жидкость – продукт,
обогащенный труднолетучим компонентом, который охлаждается в теплообменнике-10
и направляется в емкость-11.
Рис. 1. Технологическая
схема ректификационной установки
2 ТЕХНОЛОГИЧЕСКИЙ РАСЧЕТ АППАРАТА
2.1 Материальный
баланс колонны
Производительность
колонны по дистилляту Р и кубовому остатку W определяется из уравнений материального баланса:
,
где F, Р, W – расход исходной смеси, дистиллята, кубового
остатка, кг/с;
ХF, ХР, ХW – концентрация низкокипящего
компонента в исходной смеси, кубовой остатке и дистилляте.
F = 10000 кг/ч = 2,78 кг/с
= 1,26 кг/с
W = 2,78 – 1,26 = 1,52 кг/с
2.2 Пересчет массовых долей
Пересчет массовых долей в
мольные:
,
где MA и MБ – молярные массы низкокипящего (бензол)
и высококипящего (толуол) компонентов, кг/кмоль.
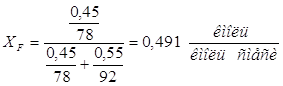
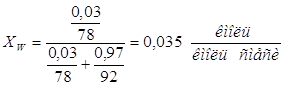
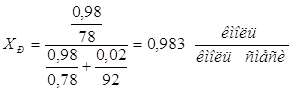
2.3 Расчет рабочего
флегмового числа
Для технологического расчета
ректификационной колонны необходимо построить равновесную зависимость между
жидкостью и паром для смеси в координатах У–X и t–X,У.
Определяем минимальное
флегмовое число:
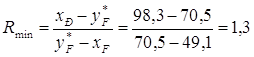
– концентрация легколетучего
компонента в паре, находящегося в равновесии с исходной смесью XF (графика У–X). = 70,5 %
Рабочее флегмовое число
определяется как ,
где β – коэффициент
избытка флегмы (β = 1,02÷3,5).
Определяется рабочее флегмовое
число R, отрезок B, число теоретических тарелок в колонне nT, путем вписывания «ступенек» между
равновесной и рабочими линиями. Рабочие линии строятся для каждого отрезка . Результаты расчетов
заносим в таблицу 2.
Таблица 2
β
|
R
|
В
|
nТ
|
пТ (R + 1)
|
1,2 |
1,56 |
38,4 |
17,8 |
45,57 |
1,5 |
1,95 |
33,3 |
14,2 |
41,89 |
1,8 |
2,34 |
29,4 |
12,5 |
41,75 |
2,5 |
3,25 |
23,1 |
11 |
46,75 |
3,5 |
4,08 |
19,4 |
10,3 |
52,33 |
4,5 |
5,4 |
15,4 |
9,5 |
60,8 |
Строится график в
координатах и из точки минимума на
кривой определяется оптимальное рабочее флегмового число R: Rопт = 2,2 при

2.4 Расчет
физико-химических параметров процесса колонны
Средние массовые расходы
жидкости для верхней и нижней частей колонны определяются из соотношений:
LB = P · R = Ф = 4421 · 2,2 = 9726,2 кг/ч
LH = Ф + F = P · R + F = 9726,2 + 10000 = 19726,2 кг/ч
Средний расход пара по
колонне постоянен:
G = P · (R + 1) = 4421 · (2,2 + 1) = 14147,2 кг/ч
средние концентрации
жидкости:


средние концентрации
пара:


где ; ; (график Х-У).
По диаграмме при средних концентрациях
пара и жидкости определяются средние температуры пара, °С:

а)
средние
мольные массы жидкости:
;

б)
средние
мольные массы пара:
;

в)
средние
плотности пара:
;
,
г)
средние
плотности жидкости:
 ; ,
где ρ1 и ρ2 – плотности массы соответственно низкокипящего и
высококипящего компонентов при температурах =
88,5ºС и = 103ºС
и – среднее массовые концентрации
жидкости вверху и внизу колонны:
; ,

; =
800 кг/м3
; =
787,4 кг/м3
д)
средние
вязкости пара:
; 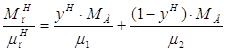
где и – среднее мольные массы
пара в верху и низу колонны, кг/кмоль;
и –
вязкости низкокипящего и высококипящего компонентов паровой смеси при
температурах и , мПа·с
, 0,92 ·
10-2 мПа·с;
, 0,923·
10-2 мПа·с
е)
средние
вязкости жидкости:
,
где и – вязкости НК и ВК
компонентов жидкости при , мПа·с
(табл. 2).
; 
; 
2.5
Определение диаметра колонны
Рабочая скорость пара для
насадочной колонны:
,
где ρп
и ρж – плотность пара и жидкости.
Насадка – Кольца Рашига
25х25х3.
f=200м2/м3
Е=0,74 м2/м3
Низ колонны:
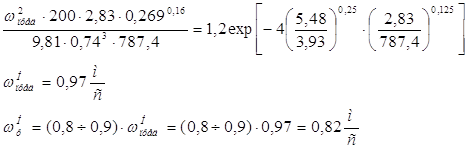
Верх колонны:
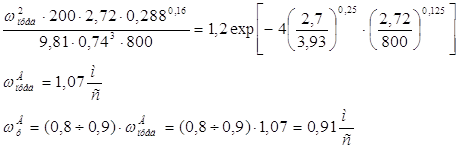
Диаметр колонны рассчитывают
отдельно для верхней и нижней частей колонны:
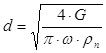
Рассчитанные диаметры
верхней и нижней частей колонны отличаются друг от друга на 3,5% < 10%,
принимаем колонну одного диаметра, равного: D=1600 мм.
Принимаю d аппарата равным 1600 мм с насыпной насадкой, перераспределительными тарелками типа ТСН-ll (ОСТ 26-705-73) и распределительной тарелкой типа ТСН-lll (ОСТ 26-705-73).
Рабочая скорость пара в
колонне при выбранном диаметре:

2.6
Определение тангенса угла наклона
Коэффициент
массопередачи зависит от угла наклона кривой равновесия, причем этот угол
является переменной величиной. Поэтому линию равновесия из графика Х-У
(рис. 1) разбивают на равные участки
вертикальными линиями, проведенными через точки Х1 =
0,1; Х2= 0,2 и т. д. Для каждого участка определяют тангенс угла наклона отрезка кривой равновесия:

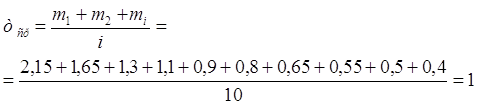
2.7 Определение
высоты колонны Расчет высоты насадки
методом ВЭТТ:
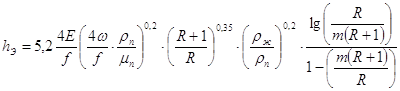

Действительная высота насадки:


Общая высота насадки:

Высота колонны
определяется по формуле:
,
где , – высота соответственно сепарационной
части колонны, расстояние между днищем колонны и тарелкой.
2.8 Гидравлическое
сопротивление слоя орошаемой насадки

где - гидравлическое
сопротивление сухой насадки, Па.
,
где - свободный объём насадки,
=0,74 м3/м3;
- эквивалентный диаметр насадки, =0,015 м;
- коэффициент сопротивления сухой
насадки.
,
где - удельная поверхность
насадки, =200 м2/м3.
Гидравлическое
сопротивление для верхней части колонны:

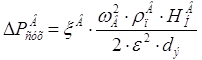

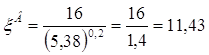


Гидравлическое
сопротивление для нижней части колонны:

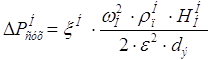

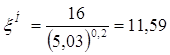


Общее гидравлическое
сопротивление для всей колонны:

2.9 Расчет патрубков
Внутренний диаметр
патрубка определяется из уравнений расхода:
, откуда ,
где G – массовый расход перекачиваемой
среды, кг/с;
ρ – плотность среды, кг/м3;
ω – скорость движения жидкости, м/с
Внутренний диаметр
штуцера для вывода дистиллята из колонны:
Стандартный диаметр
патрубка dу = 200 мм (наружный диаметр 219 мм, толщина стенки 6 мм).
Внутренний диаметр
штуцера для ввода пара в колонну:
Стандартный диаметр
патрубка dу = 300 мм (наружный диаметр 325 мм, толщина стенки 8 мм).
Внутренний диаметр штуцера
на входе исходной смеси в колонну:
,
Стандартный диаметр
патрубка dу = 100 мм (наружный диаметр 108 мм, толщина стенки 5 мм) [2, прил. 7].
Внутренний диаметр
штуцера на выходе кубового остатка из колонны:

Стандартный диаметр
патрубка dу = 80 мм (наружный диаметр 89 мм, толщина стенки 4 мм).
2.10 Расчет кипятильника
Исходные данные:
Количество паров воды для
конденсации G1 = 3,93 кг/с; удельная теплота
парообразования смеси (толуола) r1 = 362,5 кДж/кг при температуре кипения tк = 110ºС. В качестве
теплоносителя использовать водяной пар с абсолютным давлением 5 кгс/см2.
Влияние примеси бензола на теплоотдачу не учитывать.
Тепловая нагрузка
аппарата:
Q = G1 · r1 = 3,93 · 362,5·103 = 1424,63·103 Вт
Расход воды:
G2 = ,
где r2=2117·103 Дж/кг – удельная теплота
парообразования водяного пара при температуре конденсации tконд=151,1 ºС
Средняя разность
температур:
Примем ориентировочный коэффициент
теплопередачи от конденсирующего пара к воде (конденсатор) (4, табл. 3) Кор
= 1000 Вт/м2·К, тогда требуемая площадь поверхности
теплообменника:

Поверхность, близкую к
ориентировочной имеет теплообменник с высотой труб Н=2,0 м и диаметром кожуха D=0,6 м и поверхностью теплообмена F=40 м2. Испарители могут
быть только одноходовыми, с диаметром труб d=25x2 мм.
Проведу уточненный
расчет:
,
где ρ1=777 кг/м2 ; λ1=0,116
Вт/(м ·К); μ=0,251
·10-3 Па·с; σ1=18,35·10-3 Н/м -
физико-химические характеристики жидкого толуола при tкип=110ºС
Значение коэффициента b определяется по формуле:
,
где ρп –
плотность паров толуола, при tкип=110ºС



Коэффициент теплоотдачи для пара,
конденсирующегося на наружной поверхности труб высотой Н, определяется:
,
где ρ2=932 кг/м2 ; λ2=0,683
Вт/(м ·К); μ2=0,207
·10-3 Па·с – физико-химические характеристики конденсата воды при tконд=132,9ºС

Сумма термических
сопротивлений стенки и загрязнений:
,
где - толщина стенки, мм;
λст –
теплопроводность нержавеющей стали, λст =17,5 Вт/(мК)

Коэффициент
теплопередачи:

Удельная тепловая
нагрузка:
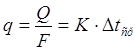

откуда

Это уравнение решается
графически, задаваясь значением q. В
качестве первого приближения принимается ориентировочное значение удельной
тепловой нагрузки:

q=40000 Вт/м2 у =2,55
q=38000 Вт/м2 y =0,93
q=37000 Вт/м2 y =0,15
при у=0 q=36800 Вт/м2
Требуемая поверхность F=1424630/36800=38,71 м2
Выбранный из каталога
теплообменник с F=40 м2;
D=600 мм; Z=1; n=257;
H=2,0 м; d=25x2 мм
подходит, так как присутствует запас поверхности.
СПИСОК
ЛИТЕРАТУРЫ
1.
К.Ф. Павлов, П.Г.
Романков, А.А. Носков. Примеры и задачи по курсу процессов и аппаратов
химической технологии. – Л.: Химия, 1987.
2.
Методические
указания по курсовому проектированию процессов и аппаратов химической
технологии. «Расчет ректификационной установки непрерывного действия». –
Ангарск, АГТА, 2000.
3.
Основные процессы
и аппараты химической технологии: Пособие по проектированию. Под ред. Ю.И.
Дытнерского, 2-е изд., перераб. и дополн.- М.: Химия, 1991.
4.
Расчет
теплообменников. Справочно-методические указания по курсовому проектированию
процессов и аппаратов химической технологии. Составили: Л. И. Рыбалко, Л. В.
Щукина. Ангарская государственная техническая академия. – Ангарск: АГТА, 2001.
|