Курсовая работа: Совершенствование технологии получения прядильного раствора в производстве ПАН волокон
Курсовая работа: Совершенствование технологии получения прядильного раствора в производстве ПАН волокон
Федеральное агентство по образованию РФ
Министерство образования и науки РФ
Технологический институт
Кафедра «Химическая технология»
Курсовая работа
по дисциплине «Химия и технология полимерных
композиционных материалов»
на тему
«Совершенствование технологии получения прядильного
раствора в производстве ПАН волокон»
2007
Содержание
Введение
1.
Литературный обзор
1.1.
Получение прядильного раствора ПАН
1.2.
Технология получения прядильного раствора
1.3.
Изменение свойств акрилонитрильных волокон при замене итаконовой кислоты в
сополимере
1.4.
Органические растворители, используемые для получения ПАН волокон
Заключение
Список
использованной литературы
Введение
На
рубеже второго и третьего тысячелетий волокна на основе полимеров и
сополимеров акрилоннтрила заняли 4-6% в общем балансе текстильного сырья.
Полиакрилонитрильные
(ПАН) волокна оказались технологически хорошо совместимыми с натуральными,
особенно с шерстью. Низкие значения плотности полимерного субстрата -
значительно ниже аналогичных характеристик шерсти - предопределили основное
направление в использовании ПАН волокон как шерстеподобного текстильного
сырья. Следует отметить, что мировое производство мытой шерсти, достигнув
постепенно снижается. Это обусловлено быстрым увеличением выпуска химических
волокон, главным образом тонких полиакрилонитрильных, успешно вытесняющих натуральные
из ряда областей потребления. Так же дефицит мытой шерсти и явился, очевидно,
важным фактором, предопределившим интенсивный рост производства ПАН волокон.
К началу
XXI в. суммарные мощности установок
производства ПАН волокон в мире составили 3,5 млн.т., а к 2005 г. намечается их увеличение до 5 млн.т. Следует отметить, что стабильные условия эксплуатации
основного технологического оборудования могут быть реализованы при его
загрузке на 83-88%. Превышение прогнозируемых объемов роста мощностей относительно
фактического производства ПАН волокон обусловлено предполагаемым увеличением
многовариантности технологических процессов и требованиями маркетинговой
стабильности.
Пожалуй,
нет другого вида химических волокон, которые производились бы в столь
разнообразных технологических вариантах, как ПАН волокна. В настоящее время выпуском
ПАН волокон в мире занято более 60 фирм. Варианты этого вида текстильного
сырья различаются следующими характеристиками.
Полиакрилонитрильные волокна и нити в настоящее время представляют
наиболее распространенный вид промышленно освоенных карбоцепных синтетических волокон.
Это связано со специфически ценными свойствами ПАН волокна: низким
коэффициентом теплопроводности, пушистостью, объемностью, которые делают ПАН
волокна практически равноценными заменителями шерсти.
Отечественное
полиакрилонитрильное волокно под названием «нитрон» впервые выпущено в 1963 г. на Саратовском АО «Нитрон». В настоящее время действуют производства по выпуску этого волокна
в г.Саратове - ОАО «Саратоворгсинтез».
ПАН-волокна и нити широко используются для изготовления
изделий народного потребления и в техническом секторе. Волокна на основе ПАН
широко используются как в чистом виде, так и в смеси с другими волокнами, в
основном, в производстве трикотажных изделий (64%), чаще всего верхнего
трикотажа, а также при изготовлении мебельных (обивочных) тканей (~ 17%),
камвольных, суконных и ковровых изделий (~ 15%), пряжи для ручного вязания
(3%), чулочно-носочных изделий (1%) [2].
1. Литературный обзор
1.1. Получение
прядильного раствора ПАН
При получении ПАН основным
волокнообразующим полимером для является не гомополимер - полиакрилонитрил, а
сополимер акрилонитрила с другими мономерами [2-4], что объясняется необходимостью:
- нарушения регулярной и
жесткой цепочки ПАН, которая определяет низкие эластические свойства волокна из
гомополимера, его недостаточную устойчивость к истиранию;
- введения
реакционноспособных функциональных групп, облегчающих накрашивание волокна.
Для получения ПАНВиН
используют различные сополимеры. В отечественной технологии производства волокна
нитрон получил применение тройной сополимер, в состав которого наряду с
акрилонитрилом (АН) СН2=СНСN (~90%) входят метилакрилат (МА) СН2=СНСООСН3
(~ 6%), как сополимер, нарушающий регулярность строения макромолекулы и улучшающий
эластические свойства волокон, имеющий ту же скорость полимеризации, что и АН и
итаконовая кислота (ИтК) (~ 1-3%),
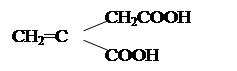
позволяющая улучшить
накрашиваемость волокна за счет присутствия реакционноспособных карбоксильных
групп. Так как в обычных условиях итаконовая кислота представляет собой
кристаллическое вещество (Тпл=163°С), то в производстве волокна нитрон для обеспечения
гомогенной среды при синтезе ПАН используют ее натриевую соль итаконат натрия
(ИтNa)
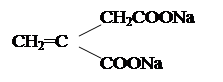
Технологический процесс получения прядильного раствора ПАН
включает следующие основные стадии:
1. синтез
полиакрилонитрила;
2. получение прядильного
раствора и подготовка его к формованию;
-
регенерация
растворителя – цех регенерации растворителя [4].
Синтез полиакрилонитрила протекает по механизму цепной
радикальной полимеризации с использованием в качестве:
· инициатора – порофора;
·
регулятора
молекулярной массы – двуокиси тиомочевины и изопропилового спирта в соотношении
2: 1 [4].
1.
Образование
активного радикала:
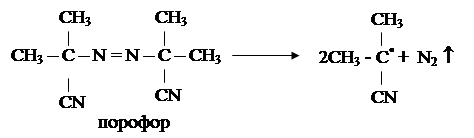
2.
Рост
макромолекулы:


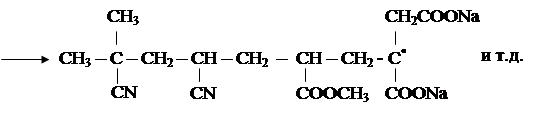
3.
Обрыв
макромолекулы может проходить через молекулу двуокиси тиомочевины (ДОТ):
4.

через молекулу изопропилового
спирта (ИПС):
1.1.1. Методы полимеризации ПАН
Полимеризацию
акрилонитрила можно проводить в блоке, в растворе и в суспензии или эмульсии [3].
Полимеризация
в блоке. Чистый мономер устойчив к действию
температуры до 200°.
Полимер не способен к деполимеризации. Эти условия упрощают процесс.
Полимеризация
акрилонитрила в блоке инициируется светом, азосоединениями, перекисями,
ионизирующим излучением, а также любым другим источником получения радикалов.
Через некоторое время после начала действия радикалов начинается выпадение
полимера в осадок. В это время наблюдается увеличение суммарной скорости
реакции. Дальнейшая реакция протекает в гетерогенных условиях. Реакция
осложняется адсорбционными процессами и может протекать на частицах полимера
как на матрицах. В гетерогенных условиях скорость реакции зависит от структуры
выпавшего полимера, от удельной поверхности частиц и гидравлических условий их
движения. Энергия активации суммарного процесса полимеризации при небольших
степенях превращения акрилонитрила составляет около 30 ккал/моль. Высокая
энергия активации, а также высокая теплота полимеризации (17,3 ккал/моль) и
сложность теплообмена приводят к взрывному характеру протекания
полимеризации акрилонитрила в блоке. Последнее обстоятельство является одной из
причин того, что блочная полимеризация не применяется в производстве.
Однако,
этот способ полимеризации не имеет практического применения.
Полимеризация
в суспензии [3,4].
Суспензионная
полимеризация ПАН основана на способности акрилонитрила образовывать при температуре
20°С 7%-ные водные растворы. Поэтому
процесс суспензионной полимеризации начинается в гомогенной среде, образующиеся
олигомеры выпадают в осадок и реакция завершается в гетерогенной среде.
Полимеризация протекает в присутствии водорастворимых инициаторов. Основные
параметры процесса:
- концентрация
АН, % |
10 – 20; |
- температура,
°С |
30 – 50; |
-
продолжительность, мин. |
20 – 120; |
- степень
конверсии (преобразования), % |
80 – 85. |
Образующийся ПАН отделяется от суспензионной среды, промывается,
сушится. Затем полимер растворяется в одном из доступных растворителей,
например, диметилформамиде (ДМФА) с получением прядильного раствора, который
проходит последующую подготовку к формованию.
К достоинствам суспензионной полимеризации относятся
возможность в широких пределах варьировать состав полимера, упрощение схемы
регенерации ванн, так как АН остается в суспензионной среде (воде), уменьшение
вредности процесса формования, так как растворы ПАН не содержат АН. Однако
многостадийность технологической цепочки при суспензионной полимеризации ПАН
резко снижает эффективность данной технологии.
Так как
полимеризация в суспензии протекает в двух фазах, то и кинетические зависимости
полимеризации будут различными. Первая стадия полимеризации происходит в водной
фазе, и скорость реакции зависит в основном от концентрации свободного мономера
и сравнима со скоростью полимеризации в растворителях.
На
второй стадии полимеризация протекает главным образом на поверхности частиц.
Скорость процесса зависит от количества сорбированного мономера и значительно
выше, чем при полимеризации в растворе. По-видимому, на поверхности частиц
повышается эффективная концентрация мономера в реакционном объеме. Ингибиторы
на этой стадии реакции обладают примерно такой же эффективностью, как и при
полимеризации в растворе, если нет преимущественной сорбции одного из них. Это
определяет автокаталитический ход реакции полимеризации в суспензии.
Поскольку
протекание реакции, особенно до высоких степеней превращения мономера,
определяет вторая стадия процесса, важнейшее значение приобретает состояние
поверхности частиц, их форма, сорбционные слои и общая величина поверхности. В
связи с этим становится понятным отличие эмульсионной полимеризации от
суспензионной. В последнем случае с помощью эмульгаторов уменьшается и
стабилизируется размер полимерных частиц. Это ускоряет и стабилизирует
процесс. В качестве эмульгаторов для эмульсионной полимеризации применяют, как
правило, неионогенные поверхностно-активные вещества или соли жирных кислот
(олеиновой, пальметиновой и др.).
Полимеризация
в растворе. Широкое
распространение в промышленности в последнее время получил метод полимеризации
акрилонитрила в растворе или лаковая полимеризация. В этом случае
полимеризация протекает в гомогенных условиях.
При
проведении полимеризации в растворе отпадает необходимость в целом ряде
операций, таких как выделение, очистка и сушка полимера на химических заводах,
транспортировка его на заводы химического волокна и растворение [5].
Полимеризация в растворе проводится в
растворителях, в которых растворимы как исходные мономеры, так и получаемый
полимер, и завершается образованием концентрированного прядильного раствора,
который используется при формовании волокна или нити [4].
Основные параметры
полимеризации в растворе:
- температура,
°С |
78 – 82; |
-
продолжительность, ч |
1,5 – 2. |
Конверсия полимеров при
полимеризации в растворе не превышает 50 – 70% во избежание получения
разветвленного полимера, характеризующегося повышенной полидисперсностью. Не
вступившие в реакцию мономеры отгоняются из прядильного раствора на стадии
демономеризации.
При полимеризации в растворе
в качестве растворителей могут быть использованы:
- органические
растворители: этиленкарбонат, а также сильнополярные апротонные
диметилсульфоксид, диметилацетамид, диметилформамид;
- неорганические
растворители: азотная кислота, а также концентрированные водные растворы
хлористого цинка, роданистого натрия и др.
Каждый из этих
растворителей характеризуется теми или иными преимуществами и недостатками.
В России
широко применяются в производстве полиакрилонитрильных волокон водные растворы
роданида натрия. Для растворения полиакрилонитрила применяется раствор
роданида натрия, содержащий 51% соли. Меньшая или большая концентрация
роданида увеличивает вязкость прядильных растворов.
Полная
сольватация роданида в водных растворах наступает при содержании 3,96
г-моль/1000 мл (вес. 25%) воды, однако при этом он еще не приобретает
способности растворять ПАН.
Способность
к кристаллизации вызывает необходимость хранения 51%-ных растворов роданида
натрия при температуре выше 15°С. Растворы роданида натрия стабильны, но
вызывают сильную коррозию металлов и в первую очередь железа. Содержание
примесей металлов в растворе не должно превышать 2-10-4%, так как
они отрицательно влияют на процесс полимеризации акрилонитрила.
На практике наибольшее
распространение в качестве растворителей ПАН получили диметилформамид НСОN(СН3)2
и 50 - 52%-ные водные растворы роданистого натрия NaSCN. Соответственно
различают два промышленных способа получения полиакрилонитрильных волокон и
нитей – диметилформамидный (на основе ДМФА) и солевой (на основе NaSCN).
До недавнего времени
достоинством растворов роданистого натрия как растворителя являлась возможность
синтеза ПАН методом полимеризации в растворе, что позволяло значительно
сократить технологию получения прядильного раствора ПАН.
Следует отметить, что
применение водных солей роданида натрия в технологии прядильного раствора ПАН
сопряжено с рядом негативных моментов. Это, во-первых, сложная и многостадийная
регенерация отработанного растворителя; во-вторых, повышенная коррозийность
оборудования, что требует соответствующего аппаратурного оформления, в-третьих,
неидеальные санитарно-гигиенические условия труда: работа с NaSCN приводит к
кожным заболеваниям и заболеваниям внутренних органов, большие энергетические затраты.
К сожалению, на отечественных предприятиях по выпуску волокна
нитрон до настоящего времени преобладает «солевой» способ (на основе NaSCN) [4].
Наряду с
преимуществами метод получения прядильного раствора путем полимеризации
соответствующего мономера или смеси мономеров в растворе имеет и серьезные
недостатки. При этом методе резко уменьшается возможность выпуска волокон
различного ассортимента. В первую очередь это относится к получению ПАН
волокон, так как при получении прядильного раствора путем растворной полимеризации
в заданных условиях и в присутствии заданного инициатора можно получить только
гомополимер или сополимер только одного вида, и, следовательно, из него может
быть получено волокно только одного вида. При получении прядильного раствора
путем растворения готового полимера или сополимера всегда существует
возможность варьировать состав выпускаемого волокна заменой одного полимера
или сополимера другим или смесью двух или трех полимеров. Это значительно
расширяет возможность модифицировать и тем самым разнообразий ассортимент
вырабатываемых волокон. В настоящее время, подавляющее число ПАН волокон
получают на основе сополимеров различного состава [5].
1.2. Технология получения прядильного
раствора
Независимо от используемого растворителя при непрерывной
технологии получения прядильного раствора в производстве волокна нитрон технологический
процесс включает следующие основные стадии [5]:
-
подготовку
мономеров и растворителя;
-
приготовление
реакционной смеси;
-
полимеризацию с
получением прядильного раствора;
-
демономеризацию
прядильного раствора с удалением не вступивших в реакцию мономеров;
-
регенерацию не
вступивших в реакцию полимеризации мономеров и передачу их на стадию
приготовления реакционной смеси;
-
подготовку
прядильного раствора к формованию (смешение различных партий, деаэрацию и
фильтрацию).
Принципиальная технологическая схема получения прядильного
раствора в производстве волокна нитрон приведена на рис.1.
В соответствии с
приведенной схемой исходные мономеры (АН, МА, ИтNa) проходят через
теплообменник-выравниватель температур (поз.2), по межтрубному пространству
которого протекает растворитель – 50 – 52%-ный водный раствор роданистого
натрия или ДМФА. Подготовленные таким образом мономеры и растворитель объемными
дозаторами (поз.3) подаются в аппарат приготовления реакционной смеси –
смеситель (поз.1), куда одновременно поступают инициатор процесса полимеризации
– порофор и регулятор молекулярной массы – двуокись тиомочевины (ДОТ). Как
правило, используют смесь ДОТ и изопропилового спирта в соотношении 2:1 с целью
уменьшения количества образующегося продукта разложения ДОТ – сульфата натрия.
В смеситель (поз.1) поступают также рециркулируемые мономеры.
Приготовленная
реакционная смесь передается в аппарат полимеризации – реактор (поз.4). Реактор
представляет собой цилиндрическую емкость с трехлопастной мешалкой. Реакционная
смесь поступает в нижнюю часть реактора и заполняет весь его объем, получаемый
прядильный раствор отбирается из верхней части реактора. Из реактора (поз.4) прядильный
раствор ПАН, содержащий 30 – 50% не вступивших в реакцию полимеризации мономеров,
проходит в аппарат отгонки мономеров – демономеризатор (поз.5), где из тонкого
слоя прядильного раствора, стекающего по стенкам аппарата и тарелкам, в
условиях вакуума удаляются не вступившие в реакцию мономеры. Удаленные мономеры
проходят сепаратор-конденсатор мономеров (поз.6) и возвращаются в
технологический цикл (поз.1) в виде рециркулируемых мономеров. А
демономеризованный прядильный раствор от нескольких реакторов поступает в бак
меланжирования (усреднения) (поз.7) и затем в аппарат удаления пузырьков
воздуха и азота (продукта разложения порофора) – деаэратор (поз.8), работающий
по тому же принципу, что и демономеризатор [7]. Деаэрированный прядильный
раствор ПАН с целью завершения его подготовки к формованию фильтруется на рамных
фильтр-прессах и передается в прядильно-отделочный цех на формование.
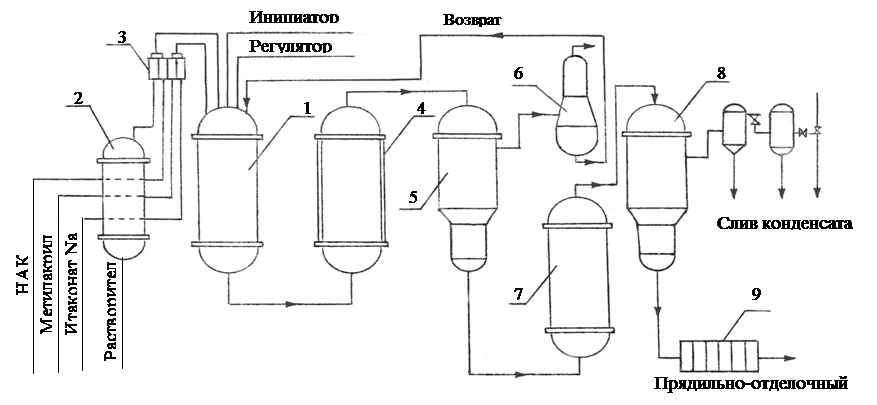
Рис.1. Принципиальная
технологическая схема получения прядильного раствора в производстве волокна нитрон:
1- смеситель реагентов; 2
– выравниватель температур; 3 - дозирующая установка; 4 – реактор; 5 –
демономеризатор; 6 – сепаратор-конденсатор; 7 – бак меланжирования; 8 –
деаэратор; 9 – фильтр-пресс
1.3. Изменение свойств
акрилонитрильных волокон при замене итаконовой кислоты в сополимере
Для получения ПАНВиН
используют различные сополимеры. В отечественной технологии производства
волокна нитрон получил применение тройной сополимер, в состав входят
акрилонитрил, метилакрилат и итаконовая кислота.
Учитывая то, что
итаконовую кислоту получают из пищевого продукта – лимонной кислоты, проводятся
работы по замене итаконовой на другие сополимеры, введение которых улучшало бы
накрашиваемость волокна нитрон. Так, например, рассматривалась возможность
использования для этих целей металлилсульфоната,
2-акриламид-2-метилпропансульфоновой кислоты [6]. Однако из-за сложности
обеспечения чистоты получаемого прядильного раствора, изменения условий
полимеризации эти сополимеры не получили практического промышленного применения
[4].
Ташкентскими
исследователями еще в 1990 г. установлена принципиальная возможность замены
итаконовой кислоты на акриловую (АК) [7].
В России
итаконовую кислоту не производят, и поэтому ее замена на более дешевый и
недефицитный продукт чрезвычайно важна. Для решения технологических задач
необходимы глубокие исследования вопросов влияния АК на процесс полимеризации,
реологические свойства растворов, равномерность и интенсивность крашения
катионными красителями.
Процесс
полимеризации осуществлялся в лабораторных условиях с моделированием
производственного режима (температура - 70°С, рН = 5) и сохранением
некоторых компонентов состава - порофора в качестве инициатора полимеризации,
диоксида тиомочевины - в качестве регулятора молекулярной массы и роданида
натрия - в качестве растворителя.
При
исследованиях изменяли продолжительность процесса полимеризации (12, 45 и 75
мин) и состав сополимера - АН:МА:АК (93,5:5,2:1,31; 92,3:5,1:2,6; 89,8:5,0:5,2
%). Образцы получали в виде пленок путем растворения сополимера в
диметилформамиде с последующим отливом.
Анализ
результатов показал, что оптимальной является продолжительность полимеризации
75 мин. За этот период, при содержании в сополимере 1,3% ИК, выход полимера
составлял 87%. Наличие в сополимере такого же количества АК приводит к
увеличению выхода полимера до 91,3%. С увеличением содержания АК в 2 и 4 раза
отмечен снижение выхода полимера.
От
состава сополимера зависят и его реологические свойства. Замена ИК на такое же
количество АК приводит к некоторому снижению вязкости, но с увеличением
количества АК вязкость возрастает, а при 4-кратном увеличении АК - возрастает
значительно, затрудняя формование волокна.
При
изучении свойств сформованных пленок установлено, что их линейная плотность
практически не зависит от состава сополимера и соотношения компонентов в нем.
По показателям механических свойств образцы на основе сополимеров с АК
превосходят промышленный образец, причем их свойства значительно зависят от
содержания АК в сополимере. Большей разрывной нагрузкой и удлинением обладают
образцы, содержащие 2,6 % АК.
Замена
одного компонента, по данным ТГА, не оказывает существенного влияния на
термостойкость сополимера. Образцы имеют аналогичные начальные температуры
термолиза: промышленный - 230°С, содержащий 1,3 и 2,6% АК - также 230°С, 5,2%
АК - 235°С. После завершения основных стадий термолиза (500°С) выход
карбонизованного остатка (КО) составляет у промышленного образца 71% (масс), у
образца, содержащего 2,6 % АК - 72%. Однако увеличение количества АК до 5,2 %
приводит к снижению выхода КО до 66%. Замена ИК на АК значительно уменьшает
экзотермические эффекты процесса циклизации, что может положительно проявиться
при переработке нитей из такого сополимера в углеродные.
Состав
сополимера анализировали методом ИК-спектроскопии. Сравнительный анализ
ИК-спектров показал совпадение полос поглощения всех валентных колебаний при
длине волн от 800 до 3200 см-1. Однако отмечена большая
интенсивность полос поглощения валентных колебаний групп СООН при 3640 см-1
у волокон, содержащих 1,3% АК, по сравнению с промышленным образцом. Увеличение
содержания АК в 2 и 4 раза практически не влияет на интенсивность частоты
колебаний групп СООН. Следовательно, изменения в спектрах поглощения связаны с
химической природой АК.
Зависимость
интенсивности окраски пленок катионными красителями от состава сополимера изучали
путем определения коэффициента отражения в видимой части спектра.
Установлено, что при замене 1,3% ИК на такое же количество АК интенсивность
окраски возрастает во всей области спектра. С увеличением содержания АК
интенсивность окраски в еще большей степени усиливается, что может позволить
сократить расход дорогостоящих красителей. Следовательно, без изменения
технологических параметров процесса, только замена ИК на АК в составе
сополимера и изменение соотношения компонентов в сополимере в производстве ПАН
волокон позволит:
-
применить более доступный и недефицитный отечественный компонент сополимера;
-
увеличите выход сополимера на 3,1 % без ухудшения физико-механических и
физико-химических свойств волокон;
-
придать волокнам большую активность при окрашивании катионными красителями.
Авторами
[8-10] с целью улучшения качества и расширения ассортимента
полиакрилонитрильных (ПАН) волокон, а также замены итаконовой кислоты (ИК) при
получении волокна нитрон предлагаются волокна на основе тройного сополимеров
акрилонитрила (АН) с метилакрилатом (МА) и N-винилкапролактамом (ВКЛ).
Синтез и
формование волокон проводили по технологическому режиму, принятому для волокна
нитрон. Волокна формовали на малой лабораторной прядильной установке из
13%-ных прядильных растворов сополимеров в роданиде натрия.
Установлено,
что при увеличении содержания ВКЛ до 8% (масс.) прочность волокон при
растяжении повышается, тогда как усадка и удлинение при разрыве уменьшаются.
Увеличение суммарного содержания вторых компонентов (МА и ВКЛ) до 20% не
приводит к существенному изменению свойств волокон по сравнению с 10%-ным их
содержанием. Этот факт, вероятно, объясняется особенностями структуры волокон.
На
физико-механические показатели волокон влияет не только состав сополимеров, но
и степень пластификационной вытяжки. С ее увеличением заметно возрастают
усадка и прочность, снижаются линейная плотность и удлинение волокон.
При
рассмотрении основных физических свойств химических волокон необходимо, прежде
всего, оценивать их надмолекулярную структуру, которая во многом определяет
эти свойства. Судя по поперечным срезам волокон на основе тройных сополимеров
АН с МА и ВКЛ, все образцы имеют овальное поперечное сечение. С увеличением
степени пластификационной вытяжки форма поперечного среза несколько изменяется,
в целом оставаясь бобовидной. Степень однородности волокон между собой и вдоль
оси по размерам, наличию дефектов, способности к свечению в поляризованном
свете, набуханию в муравьиной кислоте значительно различается в зависимости от
состава сополимера и степени пластификационной вытяжки. Самым тонким, наиболее
однородным, бездефектным и более ориентированным (по способности к двойному
лучепреломлению) оказалось волокно, полученное из сополимера с высоким содержанием
ВКЛ (АН:МА:ВКЛ= 90.21:2.05:7.85). Волокно же, содержащее 1,8% ВКЛ и 8,41% МА -
наиболее дефектное, с округлым поперечным сечением и неоднородным свечением в
поляризованном свете.
Оценивая
некоторые структурные характеристики волокон по дифрактограммам, установили,
что структура волокон заметно изменяется при варьировании состава сополимера.
Так, с увеличением содержания ВКЛ (при пластификационной вытяжке 225%) степень
кристалличности возрастает от 64 до 87% при степени ориентации 11-23, что
свидетельствует о более высокой способности к ориентации волокон, сформованных
в данных условиях.
Сравнение
результатов сорбции волокон, полученных из сополимеров АН:МА:ВКЛ одинакового
состава, показывает, что увеличение пластификационной вытяжки от 225 до 340%
приводит к уменьшению сорбции паров воды. Изменение степени пластификационной
вытяжки волокон влияет и на удельную поверхность и объем пор; значения этих
параметров возрастают с уменьшением пластификационной вытяжки. Удельная поверхность
и объем пор с увеличением содержания ВКЛ в сополимере уменьшаются.
Химическое
строение нового сополимера предопределяет сродство красителя к волокну,
поскольку функциональные группы элементарных звеньев, концевые и боковые
группы макромолекул являются активными центрами, на которых происходит
физическая или химическая сорбция красителя. Наиболее богаты активными
группами или центрами сополимерные ПАН волокна с высоким содержанием ВКЛ, в
результате чего им присуще повышенное сродство к дисперсным красителям.
Значительное влияние на адсорбцию красителей ПАН волокном оказывает нарушение
его структуры в процессе создания сополимеров АН. Активные группы мономеров,
вводимые для сополимеризации, способны образовывать дополнительные связи с молекулами
дисперсных красителей. Так, сомономер ВКЛ (вернее, его функциональные группы)
обладает высокими адсорбционными и комплексообразующими способностями и
поэтому высоким сродством к дисперсному красителю. Положительные полюса диполей
дисперсных красителей могут притягиваться к отрицательным зарядам атомов
кислорода карбоксильных групп лактамных циклов ВКЛ, которые также способны
образовывать водородные связи с атомами водорода дисперсных красителей.
Для
изучения накрашиваемости и способности сорбировать краситель, в частности
дисперсный красно-фиолетовый, использовали волокна на основе сополимера
АН:МА:ВКЛ с соотношением компонентов 90:2:8, 90:5:5 и 90:8:2, сформованные в
идентичных условиях по роданидному способу с пятикратной пластификационной
вытяжкой. Крашение проводили при температуре, близкой к температуре кипения
воды (373 К), в присутствии поверхностно-активного вещества ОП-10.
Процесс
сорбции красителя волокнами из водных растворов ОП-10 протекает сравнительно
недолго. В течение 90 мин достигается видимое равновесие. В выбранном режиме
кинетика крашения, скорость сорбции и равновесное содержание красителя в
волокне существенно зависят от содержания ВКЛ в сополимере. С увеличением
содержания ВКЛ до 8% в сополимере равновесное сорбированное содержание красителя
в волокне (С = 22 г/кг волокна), ярко-окрашенном в выбранном режиме крашения,
существенно выше, чем в волокне на основе сополимера с 2%-ным содержанием ВКЛ (14
г/кг) и волокне нитрон (3,9 г/кг). Таким образом, увеличение количества
виниллактамных групп в сополимере позволяет получить акриловые волокна, способные
окрашиваться в яркие цвета дисперсными красителями.
Поскольку
вода является структурным пластификатором по отношению к сополимеру АН:МА:ВКЛ,
процесс крашения протекает, по-видимому, в условиях, близких к переходу
полимерного субстрата в высокоэластичное состояние, что также оказывает влияние
на процесс сорбции красителя волокном.
Термодинамические
характеристики процесса крашения волокон из сополимеров АН:МА:ВКЛ определяли,
варьируя температуру от 343 до 373 К. Установлено, что с повышением
температуры равновесная сорбция красителя увеличивается. Так, для волокна на
основе сополимера, содержащего 8% ВКЛ, значения равновесного содержания
красителя на волокне составили 14,4; 17,6 и 22,0 г/кг волокна при температуре
343, 358 и 373 К соответственно. Аналогично влияет изменение температуры на
сорбцию красителя волокнами с содержанием ВКЛ 5 и 2%. Однако коэффициент диффузии
в исследуемом интервале температуры изменяется незначительно [9].
Характеризуя
исследуемые волокна, следует учитывать влияние температуры на их физическую
структуру. С этой точки зрения все новые волокна относятся к группе
гидрофобных термопластичных, не имеющих развитой системы микропор, но
способных резко увеличивать свободный объем при нагревании выше температуры
стеклования. Диффузия в этих волокнах происходит в возникающем в условиях
фиксации свободном объеме.
Таким
образом:
- при
замене ИК на ВКЛ в тройных сополимерах АН:МА:ИК получаются волокна, аналогичные
по структуре промышленному волокну нитрон, которые обладают тем более высокой
способностью к ориентации, чем больше ВКЛ введено в состав сополимера;
-
полученные волокна обладают высокими физико-механическими характеристиками,
повышенной гидрофильностью и накрашиваемостью дисперсными красителями по
сравнению с волокном нитрон;
-
увеличение содержания ВКЛ в составе сополимера, а также повышение температуры
способствуют повышению степени закрепления дисперсного красителя на волокне.
При обычных технологических режимах окрашивания удается достичь высокого
содержания остаточного красителя на волокне [8-10].
1.4. Органические
растворители, используемые для получения ПАН волокон
Из
большого числа веществ, в которых растворяется ПАН, практическое распространение
нашли органические растворители – диметилформамид (ДМФА), диметилацетамид (ДМАА),
диметилсульфоксид (ДМСО) и этиленкарбонат [2].
Полимеризация ПАН в
диметилформамиде. ДМФА
является одним из наиболее доступных и широко используемых, отличается высокой
растворяющей способностью, то есть характеризуется минимальной вязкостью
эквиконцентрированных растворов по сравнению с другими растворителями (табл.1).
Таблица
1
Вязкость
растворов ПАН в различных
растворителях при 40 °С
Растворитель |
Вязкость растворителя,
hр, П
|
Вязкость
10%-ного раствора ПАН, h0,
П
|
Относительная вязкость
hр / h0×10-2
|
Концентрация
раствора ПАН при вязкости 315 П |
Диметилформамид |
0,73 |
18 |
15 |
18,2 |
Диметилсульфоксид |
1,76 |
65 |
37 |
14,9 |
Этиленкарбонат |
1,99 |
127 |
63 |
11,6 |
В связи с этим
концентрация полимера в прядильном растворе при ДМФА-ном способе составляет:
при мокром
формовании |
- 20 – 25%; |
при сухом
формовании |
- 30 – 32%. |
Достоинством ДМФА как
растворителя в производстве полиакрилонитрильных волокон является и возможность
применения более эффективного сухого метода формования и сравнительная простота
регенерации этого растворителя.
Основные сложности при
ДМФА-ном способе сводятся к следующему:
- необходимость контроля
содержания воды в растворителе, так как повышенное количество влаги в ДМФА
(более 0,5%) уменьшает его растворяющую способность, повышает минимальную
температуру растворения сополимера, снижает стабильность прядильного раствора,
причем чем выше молекулярная масса ПАН и его концентрация в растворе, тем ниже
должно быть предельное содержание воды в ДМФА во избежание желатинизации
прядильного раствора;
- ограниченность использования
ДМФА в качестве растворителя из-за его токсичности, что, к сожалению,
характерно практически для всех растворителей;
- токсичность продуктов
его регенерации. При ректификации ДМФА образуется диметиламин – сильнотоксичный
продукт. Однако его образование можно исключить, если вести регенерацию ДМФА
при температуре 90 - 100°С
(температура кипения 150 - 152°С) в условиях вакуума;
- необходимость
специальной футеровки ректификационных колонн из-за повышенной коррозийности
оборудования в результате образования муравьиной кислоты при регенерации ДМФА [4].
Основным недостатком ДМФА
является малая скорость полимеризации акрилонитрила (до 16 – 24 ч при конверсии
мономера 70%), что в 8-10 раз превышает продолжительность в большинстве других
растворителей. Такая низкая скорость полимеризации объясняется наличием в ДМФА примесей
аминов, которые обрывают растущую цепь и ингибируют процесс радикальной полимеризации.
Однако в последние годы стал возможен выпуск ДМФА высокой степени чистоты и
осуществление непрерывной полимеризации ПАН.
Полимеризация
ПАН в диметилацетамиде. По сравнению с ДМФА диметилацетамид обладает несколько меньшей
растворяющей способностью, но менее токсичен и агрессивен, меньше разрушает
ректификационные колонны. Недостатком ДМАА является более высокая вязкость
эквиконцентрированных растворов, что обуславливает необходимость понижения концентрации
полимера в растворе на 1-2% и увеличения объема отработанной осадительной
ванны, поступающей на регенерацию. Кроме того, у ДМАА более высокая температура
кипения, чем у ДМФА (165 вместо 151°С). ДМАА образует с водой азеотроп, устойчивый до 100°С. Поэтому для полного отделения воды
от ДМАА его подвергают повторной ректификации при температурах выше 100°С.
Полимеризация ПАН в
диметилсульфоксиде.
ДМСО является одним из сравнительно доступных растворителей ПАН. По своей
растворяющей способности ПАН диметилсульфоксид следует за
диметилформамидом. Поэтому в последнее время этот растворитель начали применять
в промышленности полиакрилонитрильных волокон.
Преимуществом ДМСО при
использовании его в качестве растворителя при синтезе полимера в растворе
является высокая скорость полимеризации акрилонитрила. Продолжительность
процесса при конверсии 70% и температуре полимеризации 70°С не превышает 1,5-2 ч [2].
Также из литературных
данных следует [11-13], что растворы ПАН ДМСО более стабильны, чем в ДМФА.
Наличие кислорода в
реакционной среде при полимеризации акрилонитрила в растворе ДМСО, особенно при
температурах ниже 60°С,
сильно замедляет и даже ингибирует процесс. Поэтому полимеризацию в среде ДМСО
проводят в среде инертного газа. Используемый в качестве растворителя ДМСО
должен содержать минимальное количество воды и диметилсульфида. При наличии в
ДМСО 5% воды прядильный раствор желатинизирует уже на третий день [2].
Другое преимущество ДМСО
заключается в том, что он не вызывает коррозии аппаратуры при формовании
волокна и регенерации отработанной ванны.
Недостатками ДМСО являются:
- повышенное количество
акрилонитрила (до 3% от массы ДМСО), поступающего вместе с растворителе в виде
азеотропа в прядильный раствор и затем в осадительную ванну. Это количество
акрилонитрила выделяется при формовании волокна и регенерации осадительной
ванны, что резко повышает вредность работы в прядильном цеху;
- неприятный запах и
повышенная токсичность при разложении ДМСО при формовании волокна, т.к.
выделяется небольшое количество диметилсульфида;
- более высокая вязкость
эквиконцентрированных растворов ПАН в ДМСО (табл.1), значительно превышающая
вязкость растворов в ДМФА, что обуславливает необходимость снижения концентрации
полимера в прядильном растворе.
Полимеризация
ПАН в этиленкарбонате.
Этиленкарбонат является хорошим растворителем для полимеров и сополимеров
акрилонитрила.
Основными
преимуществами этиленкарбоната являются низкая токсичность, отсутствие коррозии
аппаратуры и высокая скорость полимеризации (1,5-2 часа при конверсии 60-70%
акрилонитрила). К недостаткам этиленкарбоната относятся:
-
высокая температура плавления (36°С), что обуславливает необходимость обогрева всех аппаратов и
трубопроводов, по которым поступает этот растворитель;
-
высокая вязкость прядильный растворов и сравнительно легкий гидролиз
растворителя при повышенных температурах, в частности при ректификации [2,3].
Таким образом, анализ
промышленных растворителей ПАН показывает большую эффективность ДМФА как растворителя
в производстве ПАНВиН. Более того, можно отметить, что ДМФА является более
технологичным и менее токсичным растворителем по сравнению с водными растворами
роданида натрия.
Заключение
Широкое
распространение полиакрилонитрильных волокон связано с их специфическими
ценными свойствами: высоко свето- и атмосферостойкотью при достаточно высоких
физико-механических свойствах. Возможность придать ПАН волокнам пушистости и
объемности делает их заменителями шерсти, а способность к циклизации позволяет
использовать их в производстве углеродных волокон.
Сополимером
при синтезе ПАН является итаконовая кислота, которую получают из пищевого
продукта – лимонной кислоты. Поэтому, в настоящее время, предлагается замена итаконовой
на другие сополимеры, введение которых улучшало бы накрашиваемость волокна
нитрон. Такими сополимерами являются: металлилсульфонат, акриловая и 2-акриламид-2-метилпропан-сульфоновая
кислоты, N-винилкапролактам.
При
замене итаконовой кислоты на N-винилкапролактам
в тройных сополимерах получаются волокна, аналогичные по структуре промышленному
волокну нитрон, которые обладают тем более высокой способностью к ориентации,
чем больше N-винилкапролактама введено в состав
сополимера. Полученные волокна обладают высокими физико-механическими характеристиками,
повышенной гидрофильностью и накрашиваемостью дисперсными красителями по
сравнению с волокном нитрон. Увеличение содержания ВКЛ в составе сополимера, а
также повышение температуры способствуют повышению степени закрепления
дисперсного красителя на волокне.
В
технологии получения ПАН наибольшее применение нашли апротонные растворители:
диметилформамид, диметилацетамид. диметилсульфоксид, гидротропный растворитель:
51,5%-ный водный раствор NaSCN.Однако, наиболее перспективным
растворителем при лаковой полимеризации ПАН является диметилформамид, так как
наиболее доступен, менее токсичен по сравнению с водными растворами роданида натрия.
Список использованной литературы
1.
Геллер Б.Э. Состояние
и перспективы развития производства полиакрилонитрильных волокон / Б.Э.Геллер //
Химические волокна. - 2002. - №3. - С.3-10.
2.
Роговин З.А.
Основы химии и технологии химических волокон / З.А.Роговин / З.А.Роговин. - М.:
Химия, 1974. - Т.2. - 344 с.
3.
Карбоцепные
синтетические волокна / под ред. К.Е.Перепелкина. - М.: Химия, 1973. - 589 с.
4.
Устинова Т.П. ПАН-волокна:
технология, свойства, применение / Т.П.Устинова, Н.Л.Зайцева. – Саратов: СГТУ,
2002. – 40 с.
5.
Юркевич В.В.
Технология производств химических волокон / В.В.Юркевич, А.Б.Пакшвер. - М.:
Химия, 1987. - 304 с.
6.
Геллер Б.Э.
Влияние кислотности реакционной среды на процесс гомофазной сополимеризации
акрилонитрила, метакрилата и 2-акриламид-2-метилпропансульфоновой кислоты /
Б.Э.Геллер, Л.А.Щербинина, О.Н.Короткая // Химические волокна. - 2000. - №2. -
С.23-26.
7.
Артеменко С.Е.
Изменение свойств полиакрилонитрильных волокон при замене итаконовой кислоты в
сополимере на акриловую кислоту / С.Е.Артеменко, Л.Г.Панова, Н.М.Савельева //
Химические волокна. – 1996. - №5. – С.42-43.
8.
Мухамеджанова
М.Ю. Структурные, физико-механические и сорбционные свойства волокон из тройных
сополимеров акрилонитрила / М.Ю.Мухамеджанова, Н.Ю.Ширшова, Г.В.Никонович //
Химические волокна. – 2000. - №3. – С.19-22.
9.
Ширшова Н.Ю.
Синтех волокнообразующих сополимеров на основе акрилонитрила, метилакрилата и N-винилкапролактама / Н.Ю.Ширшова,
М.Ю.Мухамеджанова, Г.Хамракулова // Химические волокна. – 2001. - №1. –С.3-6.
10.
Мухамеджанова
М.Ю. Реологические свойства концентрированных растворов тройного сополимера
акрилонитрила / М.Ю.Мухамеджанова, Н.Ю.Ширшова, Г.Хамракулова // Химические
волокна. – 2000. - №5. –С.3-6.
11.
Ассоциация
макромолекул полиакрилонитрила / Л.В.Дубровина, Л.М.Бронштейн, Т.П.Брагина,
П.М.Валецкий // Высокомолекулярные соединения. – Т.40, №3. – С.472-477.
12.
Иовлева М.М. К
вопросу о растворимости полиакрилонитрила / М.М.Иовлева, В.Н.Смирнов,
Г.А.Будницкий // Химические волокна. – 2001. - №4. – С.16-18.
13.
Иовлева М.М.
Фазовые диаграммы волокнообразующих полимеров / М.М.Иовлева // Химические
волокна. – 2000. - №4. – С.20-25.
|