Дипломная работа: Синтез этилового спирта
Дипломная работа: Синтез этилового спирта
Министерство образования и
науки РФ
Тверской государственный
технический университет
Кафедра технологии
полимерных материалов
Курсовая работа по
теме:
«Синтез этилового спирта»
Выполнила: Дмитриева
А.В.
БТ-0609
Принял: Лагусева Е.И.
ст.препод. кафедры ТПМ
Тверь 2008
СОДЕРЖАНИЕ
Задание к курсовой работе
Введение
1 Литературный обзор
1.1 Методы получения
1.1.1 Получение этилового спирта сбраживанием пищевого
сырья
1.1.2 Гидролиз древесины с последующим брожением
1.1.3 Получение этилового спирта из сульфитных щёлоков
1.1.4 Сернокислотный способ гидратации этилена
1.2 Направления использования
1.3 Источники сырья
2 Физико-химические основы процесса
2.1 Механизм процесса
2.2 Кинетика и термодинамика процесса
2.3 Влияние основных параметров на скорость процесса
2.3.1 Температура
2.3.2 Влияние давления
2.3.3 Концентрация исходных веществ (реагентов)
2.3.4 Влияние мольного соотношения воды и этилена
2.3.5 Катализаторы
2.4 Методы выделения продукта из реакционной смеси
3 Технологическая часть
3.1 Описание принципиальной технологической схемы
производства
3.1.1 Отделение гидратации этилена
3.1.2 Отделение ректификации водно-спиртового
конденсата
3.1.3 Катализаторное отделение
3.2 Основное и вспомогательное оборудование, его
характеристика и обслуживание
3.2.1 Реактор и колонные аппараты
3.2.2 Теплообменная аппаратура
3.2.3 Емкостное оборудование
3.2.4 Оборудование катализаторного отделения
3.2.5 Компрессоры и насосы
3.2.6 Вспомогательное оборудование
3.3 Характеристика сырья и продукта
4 Расчётная часть
4.1 Материальные расчёты и составление материального
баланса процесса
4.2 Тепловые расчёты и составление теплового баланса
процесса
4.3 Термодинамический расчёт
5 Отходы и их обезвреживание
6 Мероприятия по технике безопасности, промсанитарии,
пожарной безопасности и охране труда
6.1 Характеристика производства по взрыво- и
пожароопасности
6.2 Свойства сырья и вспомогательных материалов
6.3 Основные правила работы с токсичными газами и
едкими веществами
6.4 Основные правила пожарной безопасности
Заключение
Список использованных источников
Приложения
Задание к курсовой работе
Произвести технологический расчёт процесса
производства синтетического этилового спирта.
Данные
производительность – 12 тонн в час;
состав этиленовой фракции: этилен – 75%, этан – 25%;
соотношение Н2О : С2Н4 =
0,65 :1 ,
степень превращения по этилену - 94%;
в побочные продукты – 6%.
Введение
Этилен СН2=СН2,
пропилен СН2=СН=СН2, бутилен СН3-СН2-СН=СН2, бутадиен
(дивинил) СН2=СН-СН-СН2 будучи очень реакционноспособными
соединениями, играют важную роль в промышленности органического
синтеза. Из многочисленных реакций, в
которые вступают олефины, наибольшее практическое значение имеют
процессы полимеризации (полиэтилен, полипропилен, полиизобутилен, и др.),
гидратации (спирты), хлорирования (дихлорэтан,
хлористый аллил и т.п.), окисления (окись этилена),оксосинтеза
и некоторые другие реакции. Широкое распространение получили процессы
гидратации олефиновых углеводородов. Таким способом получаются этиловый,
изопропиловый, и другие спирты.
Этиловый спирт (этанол,
метилкарбинол, винный спирт) С2Н5ОН, мол.в. 46,07 -
важнейший представитель предельных одноатомных спиртов. Этиловый
спирт - бесцветная, легко подвижная жидкость со жгучим вкусом и характерным
запахом; т. кип.
78,3° С; т. затв. —112°С; плотность 0,789 г/см3; границы взрывоопасных концентраций этилового спирта в воздухе 3,28 - 18,95 об.%; предельно допустимая концентрация паров
этилового спирта в воздухе 1000 мг/м. Этиловый спирт смешивается в любых соотношениях с водой,
спиртами, эфиром, глицерином, бензином и др. Органическими
растворителями, горит бесцветным пламенем.
Этиловый спирт по объему производства занимает первое
место среди всех других органических продуктов. Он широко применяется как
растворитель и как исходное соединение для различных синтезов. Особенно большие
количества этилового спирта расходуются в производстве синтетического каучука.
Этиловый спирт используется также как исходный продукт для производства
хлораля, этилацетата, диэтилового эфира и многих других продуктов органического
синтеза.
1
Литературный обзор
Этиловый спирт может быть получен одним из следующих
методов: брожением пищевого сырья (зерна,
картофеля и др.), а также отходов сахарного производства –
мелассы; гидролизом растительных материалов,
переработкой сульфитного щелока, гидратацией этилена. Наибольшее
значение имеют получение этилового спирта гидратацией этилена и сбраживанием сельскохозяйственного
сырья и продуктов его переработки.
Сущность спиртового
брожения состоит в том, что виноградный сахар (глюкоза) С6Н1206
в присутствии вещества, вызывающего брожение, через ряд стадий превращается в
этиловый спирт и двуокись углерода:
зимаза (дрожжи)
С6Н1206
2С2Н5ОН + 2С02
В промышленности для
получения спирта пользуются не природным виноградным сахаром, а крахмалом
картофеля, хлебных злаков, отходами сахарных заводов. Крахмал предварительно
осахаривают под действием особого энзима — диастаза, находящегося в солоде (проросших зернах ячменя или
ржи). Осахаривание идет с присоединением воды к крахмалу; при этом образуется
дисахарид — мальтоза С12Н22О11:
диастаз (солод)
m(С6Н10О6) + 0,5mН2О 0,5m(C12H22O11)
В процессе брожения
под влиянием энзима мальтоза гидролизуется в глюкозу:
мальгаза (дрожжи)
С12Н22О11
+ Н20 2С6Н12Ов
мальтоза глюкоза
Глюкозу потом
подвергают спиртовому брожению. Мальтаза, как и зимаза, вырабатывается
быстроразмножающимися дрожжевыми грибками.
Основными видами пищевого сырья для получения
этилового спирта являются картофель и зерновые культуры.
Пищевое сырье вначале очищают от пыли, грязи
и механических примесей, оболочку толстокожурного зерна разрушают на
вальцах, жерновах или других приспособлениях, после
чего очищенный материал разваривают острым паром под давлением в течение 45-110
мин (в зависимости от вида сырья); при этом к зерну прибавляют воду. После
разваривания массу выпускают через выдувное отверстие разваривающего аппарата; при
этом происходит перепад давления от 4-5 ат до 0,2-0,5 ат
(избыточных), вследствие чего оболочки клеток разрываются и сырье
превращается в однородную жидкую массу, поступающую в заторный чан. В этот
же чан для осахаривания крахмала вводят ферментативный препарат - солод, который
получают из проращенного в особых условиях зерна (ячменя, ржи, проса). После
добавления солода массу выдерживают 10-15 мин при 61 для ее стерилизации, а
также растворения и осахаривания крахмала. По окончании осахаривания массу охлаждают до
30, после чего в нее вводят дрожжи. Полученную массу охлаждают до 22-26 град. (двухсуточное
брожение) или 15-18 град. (трехсуточное брожение) и перекачивают в
бродильные чаны. Кроме этилового спирта при брожении образуются: глицерин, янтарная
кислота, метиловый спирт,
сивушные масла,
сложные эфиры и др. Длительность брожения при непрерывном методе
составляет 60-65 часов, содержание э.с. в
зрелой бражке 8-10об.%. Бражка поступает в брагоперегонный аппарат, из
которого отгоняют этиловый спирт и летучие примеси. Остающийся
в аппарате твердый продукт - барда (4,5-7,4%), используется на корм скоту. Крепость
получаемого при перегонке спирта-сырца должна быть не менее 88% (объемн.) Из
спирта-сырца очисткой его от примесей получают спирт-ректификат (95,5%). На рис.1 приведена
схема производства этилового спирта из пищевого сырья,
включающая процессы разваривания и осахаривания крахмала.
Древесина состоит из
целлюлозы, гемипеллюлозы (пентозаны и гексозаны) и лигнина. В состав древесины
входят также минеральные вещества (зола), смолы и жиры, дубильные вещества и т.
д. На целлюлозу приходится около половины массы древесины.
Для получения спирта
древесину обрабатывают (гидролизуют) серной или соляной кислотой. При этом из
целлюлозы образуется глюкоза
(С6Н10О5)х
+ хН2О хС6Н12О6
целлюлоза
глюкоза
которая затем проходит
стадию спиртового брожения. При гидролизе концентрированной (41%-ной) соляной
кислотой получается раствор, содержащий до 30% сахаров. Однако этот способ
из-за сильной коррозии оборудования, а также трудностей при получении и
регенерации 41%-ной соляной кислоты не нашел широкого развития.J
Распространение в
промышленности получил гидролиз древесины разбавленной серной кислотой. По
этому методу древесные опилки обрабатывают в соединенных последовательно
аппаратах (перколяторах) 0,1— 0,4%-ной H2S04 при 7—15 кгс/см2 и 150—170°С.
Получаемый 4%-ный раствор сахара выпаривают, нейтрализуют гашеной известью и
после фильтрования сбраживают. Внедрен также гидролиз 0,4%-ной серной кислотой
в трубчатых аппаратах непрерывного действия при нагревании паром под давлением
25—30 кгс/см2.
Наряду с этиловым
спиртом на гидролизных заводах получают ценные побочные продукты — фурфурол,
метиловый спирт, уксусную кислоту, скипидар, белковые дрожжи, лигнин и т. д. Из
1 т древесных опилок можно получить до 200 кг гидролизного спирта (в расчете на 100%-ный).
Этиловый спирт,
получаемый на предприятиях целлюлозно-бумажной промышленности при сульфитной
варке целлюлозы, принято называть сульфитным спиртом.
При сульфитном способе
выделения чистой целлюлозы большие количества древесной щепы обрабатывают при
повышенной температуре раствором бисульфита кальция или магния, содержащим
некоторый избыток свободного сернистого ангидрида. Жидкость, оставшуюся после
обработки щепы, называют сульфитными щелоками. Это — отход целлюлозно-бумажного
производства. На каждую тонну вырабатываемой целлюлозы получается 8—12 кг
сульфитных щелоков, содержащих 10— 12% сухого вещества (лигнин, углеводороды,
белки, смолы, жиры, окись кальция и др.). Примерно 25% сухого. вещества
относится к сахарам, причем 2/3 из них способны
сбраживаться, давая этиловый спирт.
Из щелоков острым
паром отгоняют сернистый ангидрид и другие летучие вещества, затем нейтрализуют
щелок известковым молоком и направляют его в батарею бродильных чанов, где
щелок последовательно перетекает из одного чана в другой. Брожение проводят при
30 °С в течение примерно 20 ч при .интенсивном перемешивании щелока с дрожжами.
По окончании брожения дрожжи отделяют в сепараторах от сахарного раствора
(бражки). Бражка получается слабой (около 1% спирта). Ее подвергают
ректификации с получением 95%-ного этанола.
1.1.4 Сернокислотный способ
гидратации этилена.
В 1873 г. А.М. Бутлеров и В. Горяинов детально изучили
сернокислотную гидратацию этилена и предсказали техническое значение этого
процесса. В начале 30-х годов в Советском Союзе М. А.
Далиным с сотр. были проведены исследования сернокислотной гидратации
олефинов, а в 1936 г. в г. Баку
была создана первая в СССР промышленная установка по получению этанола из
нефтяных газов.
Концентрированная
серная кислота способна реагировать с этиленом, образуя моно- и диалкилсульфат:
С2H4 + H2S04 С2H5OSO2OH
моноалкилсульфат
2С2Н4 + H2S04 (C2H6О)2SО2
Диалкилсульфат
Эти эфиры при
взаимодействии с водой превращаются в этиловый спирт, выделяя кислоту:
С2H5OSO2OH + Н2О C2H5OH + H2SО4
(С2H5О)2SO2 + 2H2О
2С2H5OH + H2SО4
При этом методе можно
использовать достаточно разбавленные газы (содержащие всего 30—40% этилена),
что позволяет упростить процессы газоразделения. Содержание высших олефинов в
газе должно быть минимально, так как они под действием серной кислоты
полимеризуются с образованием нежелательных смолистых веществ.
Ниже приводится
описание принципиальной технологической схемы процесса. Газ при 25 кгс/см2
и 80 °С подают в нижнюю часть колонны (абсорбера), орошаемой 96—98%-ной серной
кислотой. Абсорбер представляет собой освинцованную и футерованную изнутри
колонну; в ней имеется 15—20 ферросилидовых тарелок с колпачками для
барботирования газа и с трубами для перелива жидкости. Температура абсорбции
поддерживается 70°С за счет снятия реакционного тепла трубчатыми
холодильниками, имеющимися на каждой тарелке. По трубкам холодильников
пропускают холодную воду. Отходящие из абсорбера газы, содержащие примерно 90%
этана и 4—6% этилена, дросселируют до 10 кгс/см2, отмывают водой от
унесенной кислоты, нейтрализуют 5—10%-ным раствором щелочи, вновь промывают и
направляют на пиролиз этана в этилен. Из нижней части абсорбера выводится смесь
моно- и диэтилсульфата с непрореагировавшей серной кислотой. Смесь охлаждают до
50 °С и после дросселирования до 5— 6 кгс/см2 направляют в
специальный аппарат (гидролизер) для гидролиза водой, отделенной при
ректификации этилового спирта.
При гидролизе кроме
этилового спирта образуются диэтиловый эфир, полимеры и т. д. Газы,
выделяющиеся при дросселировании жидкости, отмывают, нейтрализуют и
присоединяют к газам, идущим на пиролиз этана. Гидролиз проводят при 4,5—5
кгс/см2 и 92—96 °С. Вытекающая из нижней части гидролизера жидкость
состоит из этилового спирта, воды, серной кислоты, диэтилового эфира и
негидролизованного этилсульфата. Эта смесь поступает в отпарную колонну, в
нижнюю часть которой вводят острый пар для завершения гидролиза и отгонки
спирта и эфира. Отпарку в кубе ведут при 125 °С и —1,5 кгс/см2. Из
куба отпарной колонны отводят 47%-ную серную кислоту, которую после очистки от
смолистых веществ направляют на концентрирование.
Парогазовая смесь из
верхней части отпарной колонны, содержащая пары воды, этилового спирта,
диэтилового эфира и кислоты, этан и этилен, поступает
в нейтрализационно-отпарную колонну. Барботируя через щелочной раствор, смесь
нейтрализуется и далее промывается водой; поступающей с верха колонны. В куб
этой колонны подают острый пар для отгонки паров спирта из стекающего в куб
щелочного раствора. Нейтрализованные пары, отходящие из верхней части колонны,
конденсируются в холодильниках и направляются на ректификацию в очистную
колонну. В этой колонне происходит разделение эфира и спирто-водного
конденсата. Эфир дополнительно отмывают водой от спирта и направляют в
ректификационную колонну. С верха этой колонны отводится товарный эфир.
Количество его составляет ^10% от количества спирта-ректификата.
Кубовый продукт
колонны разделяют на следующей ректификационной колонне на спирт и воду,
используемую на стадии гидролиза. Кубовый продукт очистной колонны также
проходит ректификацию; в результате получают товарный спирт-ректификат.
Экономичность данного
процесса определяется в первую очередь методом концентрирования серной кислоты.
Обычно концентрирование проводят в две стадии: упаривание до 88—93%-ной
концентрации дымовыми газами в барабанных концентраторах и добавление олеума с
доведением концентрации кислоты до требуемой. Для уменьшения потерь кислоты при
упаривании и для предотвращения выделения ее паров в окружающий воздух из
газов, выходящих из концентрационных аппаратов, улавливают туман серной
кислоты на мокрых электрофильтрах в электрическом поле высокого напряжения.
Сернокислотный конденсат из электрофильтров вновь поступает в производство.
Недостатками метода являются большой расход серной кислоты, необходимость
применения кислотостойкого оборудования и недостаточная селективность процесса.
В то же время был разработан новый способ получения
этанола – прямая гидратация этилена, который не требовал использования серной
кислоты, что позволяло исключить одну из стадий процесса, сделав его тем самым
более экономичным. Более того, прямая гидратация позволяет получить более
высокий выход продукта и отличается высокой экологичностью.
Прямая гидратация этилена имеет ряд преимуществ перед
сернокислотным методом: исключение расхода серной кислоты и минимальные потребности
в других реагентах, кроме этилена и водяного пара, одностадийность процесса,
более высокий выход спирта. Недостатками прямой гидратации является частая
замена катализатора и использование более дорогих концентрированных этиленовых
фракций. Процесс синтеза
этилового спирта прямой гидратацией этилена технически более прогрессивен, чем
сернокислотной гидратацией, поэтому он получил значительно большее
распространение в промышленности. Характерной особенностью процесса прямой
гидратацией этилена является низкая конверсия исходного сырья – порядка 5% за
один проход. Таким образом, для полного использования этилена он должен быть
пропущен через систему 18-20 раз.
Этиловый спирт широко применяется в различных отраслях
промышленности:
Пищевая промышленность (главный потребитель спирта).
· ликероводочная промышленность
· производство бальзамов, настоек
· консервная промышленность
· виноделие
· производство уксусной кислоты
· кондитерская промышленность.
Парфюмерная промышленность (более 85% парфюмерной продукции содержит раствор спирта).
Фармацевтическая промышленность (40% всех лекарственных препаратов
приготовлено с использованием этилового спирта).
Медицина
· дезинфекция инструментария
· процедуры
Химическая промышленность
· производство синтетического спирта
· производство эфиров, этилена, этила
· производство растворителей, политуры
· производство искусственного волокна
· производство лаков и красок
· производство стекла
· производство антифриза
· производство носителей информации
(аудио-,видео-фотопленка)
· производство синтетического каучука,
ацетальдегида, хлороформа, этилацетата и др. органических продуктов
· производство взрывчатых веществ
· производство топлива для реактивных двигателей
и др.
Радиоэлектронная промышленность
· обслуживание приборов
· производство микросхем
Кожевенная
промышленность
· дубление кожи
Таким образом, спиртовое производство тесно связано, с одной
стороны, со многими отраслями, в которых спирт служит
сырьем, основным и вспомогательным материалом, с
другой - с сельским хозяйством. Оно является единственным производством,
способным превращать дефектные (порченые) зерно и картофель и другие материалы
в доброкачественные продукты.
Исходным сырьем при получении спирта из пищевых
материалов являются
растительные продукты, содержащие углеводы: моно- или
дисахариды, главным образом глюкозу и сахарозу, а также полисахариды – крахмал.
Позже стали применять древесную целлюлозу, которая гидролизом превращается в
глюкозу.
Непосредственно сбраживанию с образованием этилового
спирта подвергаются только моносахариды, поэтому сахар или крахмал под влиянием
ферментов, содержащихся в дрожжах, превращаются в моносахариды:
С12Н22О11
+ 2 Н2О С6Н12О6 + С6Н12О6
сахар глюкоза фруктоза
2(С6Н10О5) + 2x Н2О →xС12Н22О11 2x С6Н12О6
крахмал дисахарид глюкоза
Процесс брожения с образованием этилового спирта
С6Н12О6 2С2Н5ОН
+ 2 СО2
происходит под влиянием бактерий. Наряду с этиловым
спиртом в небольшом количестве получаются высшие спирты.
Глюкоза может быть получена и из древесной целлюлозы
гидролизом. Гидролиз осуществляется при действии концентрированной соляной
кислоты (41% -ной) или разбавленной серной кислоты (0,4 % -ной) при 150-170º
С и 15-30 ат:
(С6Н10О5) + x Н2О x С6Н12О6
Таким образом, сырьем для производства технического
этилового спирта могут быть крахмалосодержащие вещества ( различные виды зерна,
картофель) или сахаросодержащие продукты (сахарная свекла, сахарный тростник и
отходы от производств сахара). При производстве гидролизного этилового спирта
исходным сырьем являются отходы деревообрабатывающих заводов – опилки.
При производстве синтетического этилового спирта
сырьем служит этилен, который получается при пиролизе газового сырья или
нефтяных дистилляторов. Для получения этилового спирта этилен подвергается
сернокислотной или прямой гидратации на твердых фосфорнокислых катализаторах:
+H2SO4 + H2O
C2Н5OSO3 H C2H5OH + H2 О
СН2 =СН2 — +H2O
C2H5OH
H3PO4
Трудовые затраты при производстве этилового спирта из
пищевых продуктов или древесных опилок очень велики, поэтому значительно
выгоднее исходить из дешевого углеводородного сырья и получать спирт
гидратацией этилена.
2 Физико-химические
основы процесса.
2.1 Механизм процесса.
Присоединение
воды к олефинам всегда происходит по правилу Марковникова. Поэтому
первичный спирт можно получить только из этилена; из других олефинов получаются
вторичные или третичные спирты.
Прямой гидратацией
этилена называется обратимый экзотермический процесс непосредственного (без
образования промежуточных продуктов) присоединения воды к этилену в присутствии
катализатора с образованием этилового спирта:
СН2=СН2
+ Н2 С2H5OH + 10,55 ккал
Катализатором процесса
служит ортофосфорная кислота на шариковом носителе — силикагеле. Реакция
предположительно протекает в четыре стадии:
1) физическое
растворение этилена в пленке кислоты;
2) образование иона
карбония:
 С2Н4 + H+ C2H5+
3) взаимодействие иона
карбония с водой с образованием иона алкоксония:
 C2H5+ + Н2О C2H5О+Н2
4) разложение иона
алкоксония на спирт и протон:
 C2H5О+Н2 C2H5ОН+ Н+
Активность
катализатора в течение цикла его пробега постепенно снижается из-за уноса ортофосфорной
кислоты с проходящим через реактор потоком продуктов. Во избежание коррозии
оборудования унесенной кислотой ее нейтрализуют; с этой целью в парогазовый
поток после реактора впрыскивают подщелоченный водно-спиртовый конденсат.
Степень превращения
этилена за один проход через реактор составляет 3,5—4,8%. Непрореагировавший
этилен возвращается в реактор (рециркулирует), пары воды и спирта
конденсируются в системе теплообменников и холодильников, а циркулирующий газ
при этом охлаждается. Водно-спиртовый конденсат отделяют от циркулирующего газа
в сепараторах и направляют на ректификацию. Из всего количества этилена,
вступившего в реакцию, только 95—98,5% превращается в спирт, а остальное
— в диэтиловый эфир, ацетальдегид, полимеры. С целью повышения степени
превращения этилена в спирт поддерживают высокую концентрацию этилена в
циркулирующем газе (90% масс, и более). При этом необходимо, чтобы концентрация
этилена в свежей этиленовой фракции, поступающей с газоразделительной
установки, была равна 99% (масс).
При ректификации водно-спиртового
конденсата из него получают 93—94%-ный спирт. Из выделенного концентрированного
спирта удаляют небольшие количества ацетилена.
2.2 Кинетика и термодинамика процесса.
Рассмотрим равновесие основной реакции: гидратации -
внутримолекулярной дегидратации:
 Н2С=СН2
+ Н2О Н2СОН – СН3
Она протекает с выделением тепла, следовательно ее
равновесие смещается вправо при понижении температуры. Дегидратации, наоборот,
способствует нагревание. Равновесие невыгодно для гидратации олефинов,
так как при 150-300о С, когда катализаторы процесса достаточно
активны, DGо
имеет большую положительную величину и равновесие смещено в сторону
дегидратации. При этом для олефинов разного строения различия в термодинамике
рассматриваемых реакций незначительны. Как показывает стехиометрия реакций, на
их равновесие можно влиять, изменяя давление. Внутримолекулярной дегидратации,
идущей с увеличением числа молей веществ, способствует пониженное или обычное
давление. Наоборот, гидратации олефинов (в том числе и этилена)
благоприятствует высокое давление, увеличивающее равновесную степень конверсии
олефина. Так, последняя при 250-300о С и атмосферном давлении
составляет всего 0,1-0,2%, что совершенно неприемлемо для практических целей,
но при 7-8 Мпа и тех же температурах она возрастает до 12-20 %. Зависимость
равновесной степени конверсии этилена при его гидратации от давления и температуры
изображена на рис.2, причем аналогичные кривые характерны и для других
олефинов. Очевидно, что гидратации способствует одновременное снижение
температуры и повышение давления.
Рассмотрим теперь равновесие в системемежмолекулярная
дегидратация спиртов - гидролиз простых эфиров:
 2ROH ROR + Н2О
В случае этанола ее равновесие описывается уравнением
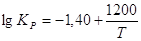
показывающим, что оно смещается вправо при снижении
температуры. Следовательно, при 200-400о С внутри- и межмолекулярная
дегидратация конкурируют друг с другом. Термодинамическим методом регулирования
направления этих реакций является изменение давления: на образование простого
эфира оно не влияет, но получению олефина его снижение благоприятствует.
В ряде случаев роль воды более сложная. Так, фосфорная
кислота, нанесенная на пористый носитель, образует на его поверхности жидкую
пленку, которая абсорбирует воду из газовой фазы. При каждых данных температуре
и парциальном давлении водяных паров в газовой фазе устанавливается фазовое
равновесие, и фосфорная кислота в пленке имеет определенную концентрацию и
соответствующую ей каталитическую активность. Последняя падает при снижении
температуры и росте парциального давления воды, что ограничивает выбор этих
параметров для каждого случая определенными рамками.
2.3.1 Температура.
Реакцию прямой гидратации этилена желательно проводить
при невысоких температурах. Однако практически выбор температуры
лимитируется скоростью реакции и активностью применяемых катализаторов.С
повышением температуры, при прочих равных условиях, равновесная
степень превращения этилена в спирт снижается. Однако при низких
температурах активность фосфорнокислотного катализатора очень мала. Так,
степень конверсии этилена при 280-290о С достигает лишь 4-5%, а при
более низких температурах она еще меньше.На практике процесс прямой гидратации в
паровой фазе в присутствии фосфорнокислотного катализатора ведут в интервале
260-300о С.
С повышением
температуры до 290 °С скорость гидратации этилена возрастает. Дальнейшее
повышение температуры до 320 °С сопровождается незначительным снижением степени
конверсии этилена в этиловый спирт; кроме того, при этом резко возрастает выход
побочных продуктов. Зависимость текущей производительности реактора по спирту (Gcп) от температуры (Т, К)
в верхней части аппарата описывается эмпирическим уравнением:

где а, b, с – коэффициенты, зависящие от активности катализатора и от технологических
параметров процесса. Каждому моменту времени
соответствует оптимальная температура, обеспечивающая максимальные текущую и
суммарную производительность аппарата при минимальной себестоимости спирта.
Отклонение температуры от оптимальной на 5°С приводит к снижению
производительности реактора на 5%; при этом соответсвенно возрастает расход
пара, электроэнергии и катализатора на 1 т спирта. Оптимальная температура (Т,
К) верха реактора, в соответствии с литературными данными, определяется
по формуле:
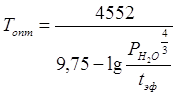
где Рн2о
— парциальное давление паров воды в реакторе, кгс/см2; tэф - эффективное время реакции, с. Использование этого уравнения для
регулирования температуры верха аппарата осложняется трудностью определения tэф для каждого момента работы реактора.
Повышение давления благоприятствует реакции гидратации, причем
оптимальное давление составляет 6,7-8 Мпа . Это давление связано с процессом абсорбции
этилена фосфорной кислотой. Оптимальное парциальное давление водяных
паров равно 2,7-3 Мпа ; оно и определяет мольное соотношение водяных
паров и этилена. Оптимальное парциальное давление этилена составляет 3,5-3,7 Мпа. Общее
давление складывается из парциальных давлений воды, этилена
и примесей. При концентрации этилена в циркулирующем газе 80-85%
общее давление системы получается равным 7-8 Мпа.
Повышение концентрации этилена в циркулирующем газе
при постоянной циркуляции способствует повышению производительности реактора и
снижению расхода пара, электроэнергии и катализатора на 1 т спирта. В то же
время для поддержания более высокой концентрации этилена в газе необходимо
увеличивать долю газа, выводимого из системы для удаления инертных примесей, а
это отрицательно влияет на себестоимость спирта. Оптимальной концентрацией
этилена в циркулирующем газе является 90-92% (об.). повышение концентрации
этилена сверх 93% (об.) нецелесообразно, так как это значительно увеличивает
себестоимость спирта.

Согласно термодинамическим данным, с
увеличением отношения Н2О : С2Н4 c 0,5 :1 до 1 : 1 значительно повышается степень конверсии
олефина. Однако экспериментальные данные отличаются от
термодинамических: с увеличением отношения Н2О : С2Н4
до 0,7-0,75 степень конверсии этилена действительно
возрастает, но при дальнейшем его увеличении она снижается.
Установлено также, что от соотношения Н20 : С2Н4
зависит и активность катализатора гидратации. Оптимальная концентрация
фосфорной кислоты в жидкостной пленке на пористом носителе составляет 83-85%. Эта
величина зависит от парциального давления водяного пара,
которое определяется общим давлением в системе и мольным отношением вода : этилен.
Оптимальная концентрация Н3РО4 наблюдается при
соотношении Н2О : С2Н4 = 0,75:1. С
дальнейшим ростом этого соотношения возрастает количество воды в пленке,
уменьшается концентрация кислоты и снижается степень конверсии этилена. Поэтому
в промышленных условиях принято мольное соотношение Н2О : С2Н4=(0,6-0,7) : 1.
Промышленные катализаторы должны удовлетворять ряду
требований, предъявляемых технологией. Катализаторы должны быть активными к
данной реакции, возможно более стойкими к действию контактных ядов,
сравнительно дешевыми, обладать высокой механической прочностью,
термостойкостью, определенной теплопроводностью и т.п. Поэтому применяемые на
практике катализаторы редко являются индивидуальными веществами и, как правило,
представляют собой сложные механические смеси, называемые контактными массами. В
состав контактной массы входят в основном три составные части: собственно
катализатор, активаторы и носители.
Носителями называются термостойкие инертные пористые
вещества, на которые тем или иным способом наносят катализатор. Использование
носителей преследует как технологические, так и экономические цели. Во-первых,
при этом создается пористая контактная масса с богато развитой внутренней
активной поверхностью, увеличивается ее механическая прочность и
термостойкость, во-вторых экономится дорогой катализатор (платина, никель,
пятиокись ванадия и т.п.). В некоторых случаях сами носители могут быть
активаторами. К типичным носителям катализаторов относятся силикагель,
алюмосиликат, асбест, пемза, кизельгур, уголь, каолин, некоторые соли.
Поскольку любой каталитический процесс протекает на
поверхности контактной массы, скорость и глубина такого процесса во многом
определяется величиной поверхности катализатора. Одной из основных
характеристик контактных масс является величина удельной поверхности Sуд.
,т.е. поверхность единицы веса или объема катализатора. Для большинства
промышленных катализаторов Sуд составляет от нескольких десятков до нескольких сотен м2 / г.
Чтобы обеспечить столь высокую удельную поверхность, контактные массы должны
быть материалами с высокой пористостью. Мелкие поры, пронизывая зерно
контактной массы, создают внутреннюю поверхность, которая, как правило, в
несколько сотен раз больше ее наружной поверхности.
В производстве этанола прямой гидратацией этилена
наиболее широкое применение получил фосфорнокислотный катализатор на твердом
носителе.
Катализаторы прямой гидратации не должны разрушаться
под действием влаги, поэтому такой катализатор, как фосфорная кислота на
кизельгуре, неприменим - он не имеет скелета и легко разрушается. В качестве
носителя для фосфорной кислоты применяют силикагель или
алюмосиликат. Чаще всего используют шариковый широкопористый силикагель,
обработанный водяным паром с целью снижения удельной поверхности и подавления
побочных реакций уплотнения.
Носитель пропитывают 65 %-ной фосфорной кислотой и
сушат при 100о С. Готовый катализатор содержит 35-40% Н3РО4 85 %-ной концентрации.
В условиях реакции фосфорная кислота, осажденная на
носителе, растворена в пленке воды, адсорбированной на поверхности пор, и
реакция фактически протекает в жидкой пленке фосфорной кислоты. Кислотный катализ,
таким образом ,сводится к гомогенному катализу в жидкостной пленке
катализатора.
Существенными недостатками фосфорнокислотного
катализатора являются его коррозионная агрессивность и постепенный унос кислоты
с поверхности носителя. Эти недостатки могут быть полностью устранены при
использовании нейтральных катализаторов - вольфрамовых и кремневольфрамовых.
Разработаны процессы гидратации этилена на нейтральном
катализаторе в жидкой фазе при 250-300о С и 30 Мпа и при 300о
С и 14 Мпа. В этих случаях процесс ведут в колонне высокого давления, где на
тарелках помещен катализатор - оксиды вольфрама на силикагеле (15-20 % WO3
). Этилен и воду подают в верхнюю часть колонны, а снизу отводят 10 %-ный
спирт. В этом процессе не требуется расходовать большое количество тепла на
испарение воды и перегрев водяного пара.
Разработаны и другие активные вольфрамовые
катализаторы, содержащие 40-60% триоксида вольфрама на широкопористом
силикагеле типа SiO2·12WO3·7Н2О с добавкой борной кислоты.
Катализаторы этого типа готовят, пропитывая силикагель раствором вольфрамата
аммония и прокаливая затем при 400о С . Они не нуждаются в
последующем восстановлении. Добавление в состав катализатора 5-10% борной
кислоты существенно повышает его активность. Наиболее активный катализатор,
содержащий 60% WO3 и 5% В2О3 на силикагеле, применяется в интервале
200-240о С и 1,5-2,5Мпа, т.е. в более мягких условиях- при конверсии
5,5%.
Вольфрамовые катализаторы более активны, чем
фосфорнокислотные, и могут работать в более мягких условиях. Однако они
значительно дороже, ибо вольфрам - дефицитный материал, поэтому такие
катализаторы не нашли широкого промышленного применения.
По технологической схеме прямой гидратации этилена,
описанной в данной курсовой работе, отделение спирто-водного конденсата от
этилена происходит в сепараторах, после чего спирто-водный раствор и все потоки
спирто-водного конденсата после освобождения от растворенного этилена поступают
на ректификацию. Газ, отходящий из сепараторов, содержит
в себе примеси спирта. Для отделения от этих примесей газ
направляется в водяной скруббер, а затем поступает на циркуляционный
этиленовый компрессор. Ректификация осуществляется в колонне
азеотропной ректификации, работающей по стандартной схеме. В ней
от избытка воды отгоняется азеотроп спирт-вода. Спирт-ректификат содержит
некоторый избыток воды, концентрация спирта в нем составляет 90-92%. С низа
колонны выводится фузельнвя вода.
Рассмотрим теперь ряд изобретений по способам
выделения этилового спирта. Авт.свид. 307997 (В.Н.Карасев
и В.Я.Старцев). Изобретение относится к способам переработки
спирта-сырца, полученного прямой гидратацией этилена на
фосфорнокислом катализаторе.
В процессе получения синтетического этилового спирта
способом прямой гидратации этилена на фосфорнокислом катализаторе образуется
5-25% - ный раствор спирта-сырца, содержащий полимеры,
которые при дальнейшей переработке спирта-сырца (на ректификационных
установках) распределяются на тарелках ректификационной колонны и выводятся с
товарным продуктом - спиртом ректификатом) - ухудшая его качество, и
фузельными водами, загрязняя химические стоки.
В существующем способе переработки спирта-сырца
предусматривается вывод полимеров из колонн ректификации путем направления
всего потока жидкостной фазы исчерпывающей части колонны во флорентийский сосуд. Из
флорентийского сосуда (после отстаивания) полимеры направляют в сборник, а
водно-спиртовой конденсат возвращают в исчерпывающую часть колонны на нижележащую
тарелку.
В связи с тем, что концентрация полимеров в спирте-сырце
составляет в среднем 0,1 вес.%, а количество жидкостной фазы в исчерпывающей
части ректификационных колонн велико, данный метод не позволяет выделить полимеры и
последние выводятся из колонны частично в составе фузельной воды в виде
химически загрязненных стоков в больших количествах, сбрасываемых
через установку биологической очистки в природные водоемы, частично
попадая в продукт, ухудшая его качество. Полимеры,
содержащиеся в фузельной воде, очищаются биологическим методом очень трудно.
С целью улучшения качества спирта и упрощения очистки
сточных вод, предлагается при выделении этилового спирта, полученного
прямой гидратацией этилена, отводить из ректификационных колонн
жидкостную фазу с содержанием спирта 40-80 об.% с последующим ее
разбавлением до содержания спирта 10-20 об.% и направлять в отстойник.
Полимеры, являясь водонерастворимыми органическими
продуктами, хорошо растворяются в этиловом спиртеи в процессе
ректификации накапливаются в колонне, достигая максимальной концентрации (17-35 об.%) в
той части колонны, где концентрация спирта 40-80 об.%.
Выделившиеся при разбавлении полимеры отделяют от
водно-спиртового слоя во флорентийском сосуде и выводят в сборник, а
водно-спиртовой слой направляют обратно в колонну на тарелку питания.
Способ позволяет улучшить качество стоков по
химическому поглощению кислорода на 60-65% и качество спирта по содержанию в
нем примесей, определяющихся по ГОСТ 11547-65, на 25
вес.%.
Предмет изобретения: Способ выделения
этилового спирта, полученного прямой гидратацией этилена, путем
ректификации спирта-сырца с одновременным отводом жидкостной фазы исчерпывающей
части колонны в отстойник, отделением полимерной фракции и возвратом
водно-спиртовой фракции на ректификацию, отличающийся тем, что, с
целью улучшения качества целевого продукта и упрощения очистки сточных вод, из
ректификационной колонны отводят жидкостную фазу с содержанием 40-80 об.% ,
разбавляют ее до содержания спирта 10-20 об.% и направляют в отстойник.
Авторское свидетельство 368216.
(Авторы: Г.З.Блюм, В.Л.Волков, С.С.Иевлева и др.). Способ
выделения этилового спирта. С целью получения спирта высокой степени
чистоты предлагается водно-спиртовые растворы, получаемые в качестве
отходов при производстве двуокиси кремния, обрабатывать солями гидроксиламина в
количестве 0,8-1% на 1 л спиртсодержащего раствора, а затем
хлористым кальцием в количестве не менее 3 вес. % или разбавленной серной
кислотой в количестве не менее 10 г на 1 л спиртосодержащего раствора с последующей ректификацией. При однократной ректификации с флегмовым
числом 1 получают 96 %-ный спирт, при вторичной ректификации спирта (флегмовое
число 4-5) получают этиловый спирт, по чистоте не уступающий гидролизному спирту
высшей очистки, а также пищевому,
вырабатываемому из пищевого сырья.
При проведении ректификации во фторопластовой колонне
получают спирт особой чистоты, удовлетворяющий требованиям электроники. Авторское
свидетельство 608796. Способ выделения этилового спирта (Авторы: Е.А.Рябенко, Г.З.Блюм, Г.Г.Виноградов
и др.). Изобретение относится к усовершенствованному
методу получения спиртов, в частности этилового спирта особой чистоты,
используемого, например, в электротехнической промышленности.
По основному авт. свид. 368216 известен способ выделения этилового
спирта из водно-спиртовых растворов, получаемых в качестве отходов при производстве
двуокиси кремния обработкой их последовательно солями гидроксиламина.
Однако в таком способе целевой продукт загрязнен
аммиаком и продуктами его реакции. В связи с хорошей растворимостью в воде
сульфата аммония и некоторых других производных аммиака,
образующихся при осаждении аммиака серной кислотой, последний
полностью не удаляется из водного раствора спирта, РН такого спирта 7,5-8,0. Этот
спирт не может быть использован при обработке полупроводниковых пленок, т.к.
образует на их поверхности налеты, что приводит к нарушению работы приборов.
C целью повышения качества
целевого продукта предлагается в способе выделения этилового спирта по авт. Свид. 368216
водноспиртовой раствор предварительно концентрировать до содержания этилового
спирта 94,0 -96,6 об.%. Предпочтительно фильтрат разбавляют водой до
45-50 об.% и пропускают через активированный уголь со скоростью
2-5 см3/см2·мин. Целевой
продукт выделяют ректификацией. При этом происходит полное осаждение аммиака
и ряда продуктов его реакции с серной кислотой и спиртом.
Одновременно происходит более полное удаление некоторых микропримесей,
например, Са, Fе.
Авторское свидетельство 577201. Способ
выделения одноатомных алифатических спиртов. (Авторы: А.Д.Пешенко, В.И.Радюк и
др.). Изобретение относится к области получения спиртов, в
частности к усовершенствованному способу выделения одноатомных алифатических
спиртов из водных растворов, которые широко используются в органическом
синтезе.
Одноатомные спирты обычно выделяют из продуктов
синтеза ректификацией, причем концентрация спирта в водных растворах, как
правило, не превышает 4-5%.
Поэтому количество воды, которое необходимо отогнать
в процессе ректификации для выделения спирта, в десятки раз превышает
количество его самого. Так как теплота парообразования воды намного
больше теплоты парообразования спиртов, то этот процесс связан с большими
энергетическими затратами. Известен способ выделения одноатомных
алифатических спиртов экстракцией сложным эфиром - этилацетатом. Однако
он не позволяет достигнуть достаточно высокой степени извлечения спиртов, поскольку
коэффициенты распределения для этих спиртов невысоки ( для метанола - 0,1641, этанола
и пропанола 0,5176 и 2,4270) Кроме этого этилацетат хорошо растворим в
воде и имеет невысокую температуру кипения (77,1град.C) и в связи с этим количество экстрагента, которое
необходимо отогнать при выделении экстрагируемого вещества, в
десятки раз превышает количество самого экстрагированного вещества, что
приводит к большим энергетическим затратам.
3 Технологическая часть
3.1 Описание принципиальной технологической схемы
производства
Технологические особенности процесса.
Основной особенностью процесса прямой гидратации
этилена является малая степень конверсии этилена за один проход - не выше 4,5%. Этим
обусловлена необходимость рециркуляции значительных его количеств.
Ввиду высокой кратности циркуляции этилена в системе
возможно накопление инертных примесей, поэтому содержание их в исходном этилене не
должно превышать 2-5%. Эти примеси представляют собой метан и этан. В
результате циркуляции непревращенного этилена концентрация примесей в циркулирующем
этилене возрастает, а концентрация этилена снижается.
Заданную концентрацию этилена в циркуляционном газе поддерживают путем отдувки
части циркулирующего газа в систему газофракционирования.
Поскольку в циркулирующем этилене инертных примесей больше, чем в
свежем, при отдувке можно вывести из системы все поступающие
туда инертные примеси.
Большие объемы циркулирующего газа нужно охлаждать
после реакции и вновь нагревать перед подачей в реактор,
поэтому при гидратации большую роль играет выбор эффективных способов
охлаждения.
Важное значение в процессе имеет также регенерация
тепла, необходимая для снижения расхода пара или топлива на
нагрев сырья и уменьшения расхода воды на охлаждение продуктов. Кроме
того, при рациональной схеме регенерации тепла может быть
значительно понижен или полностью исключен расход пара высокого давления,
необходимого для проведения собственно гидратации.
Реакция прямой гидратации этилена идет с выделением
значительного количества тепла. Однако вследствие низкой степени конверсии
этилена выделяющееся тепло расходуется на нагревание самого этилена и водяного
пара, причем в реакторе адиабатического типа (без отвода
тепла) перепад температуры парогазовой смеси не превышает 10-20о С, что
вполне допустимо. Поэтому проблемы отвода тепла в этом процессе не
возникает.
Еще одной особенностью процесса является унос
фосфорной кислоты вследствие пропускания значительного количества парогазовой
смеси через слой катализатора. Унос кислоты парогазовой смесью, по
опытным данным, составляет 0,5г/ч с 1 л катализатора или 1,5-3 кг в расчете на 1 т спирта.
Активность катализатора в процессе работы снижается
вследствие уноса кислоты и зауглероживания. Срок службы катализатора составляет 400-500 ч. Затем
катализатор регенерируют путем выжигания кокса и нанесения фосфорной кислоты. Срок
службы катализатора можно увеличить до 900-1000 ч, добавляя фосфорную
кислоту в парогазовую смесь на входе в реактор.
В качестве сырья для процесса прямой гидратации
используется технический этилен, содержащий 98-99,9% С2Н4.
Технологическая установка производства этанола прямой
гидратацией этилена состоит из трех отделений: гидратации этилена, ректификации
водно-спиртового конденсата, катализаторного отделения.
Технологическая схема отделения
гидратации изображена на рис. 1. Этиленовая фракция из цехов газоразделения
через буфер поступает на прием поршневого одноступенчатого компрессора 2. Сжатая
до 70 кгс/см2 фракция поступает на смешение с обратным циркулирующим
газом в кольцевой коллектор. Циркулирующим газом называют газ, который с нагнетательной
линии компрессора 3, пройдя весь агрегат гидратации, возвращается на
прием компрессора 3. Подпитанный свежим этиленом циркулирующий газ из
кольцевого коллектора идет на прием циркуляционных компрессоров 3. Обратный
циркулирующий газ из аппаратов гидратации поступает в кольцевой коллектор поеле
скруббера 13. Компрессор 3 сжимает газ до давления не более 80
кгс/см2 и подает его в межтрубное пространство теплообменника 5, где газ
подогревается за счет тепла обратного газа. Сжатый компрессором 3 газ
принято называть прямым газом, а газ, прошедший реактор гидратации, — обратным
газом.
Прямой газ из теплообменника 5 поступает
в межтрубное пространство теплообменника 10, где подогревается обратным
циркулирующим газом до 190—215 оС. Из межтрубного пространства
теплообменника 10 нагретый газ поступает в трубное пространство подогревателя
4, где паром высокого давления подогревается до 220—269 °С. Паровой
конденсат из подогревателя 4 дросселируют до 6 кгс/см2 и
собирают в пароотделителе, а оттуда отводят в цеховую емкость-сборник.
Образовавшийся при дросселировании пар отводят из пароотделителя в линию пара
под давлением 6 кгс/см2. Прямой газ после подогревателя 4 смешивается
с паром высокого давления (80—100 кгс/см2, ^440 °С) в массовом соотношении 1 :
(0,35-0,43). Смешение происходит в тройнике перед реактором 9.
Паро-газовая смесь при 273—295 °С
поступает в верхнюю часть реактора (гидрататора) 9 и проходит сверху
вниз через слой катализатора. Около 4% этилена из паро-газовой смеси
гидратируется при этом в этиловый спирт.
Выходящие из реактора с температурой
не выше 310 °С продукты уносят некоторое количестве фосфорной кислоты. Для ее
нейтрализации в паро-газовую смесь впрыскивают водно спиртовый раствор щелочи с
концентрацией NaOH 0,25—0,5% (масс), подаваемый в тройник нейтрализации насосом
17 из емкости 16. Подщелоченный водно-спиртовый конденсат готовят
следующим образом: 42%-ный раствор NaOH (содержание Na2C03 не более 2%, по ГОСТ
2263—59) со склада поступает в сборник 19, откуда насосом 18 подается
на смешение с водно-спиртовым конденсатом, поступающим из коллектора через
холодильник 15. Приготовленный конденсат собирается в емкости 16. Подачу
конденсата регулируют по температуре паро-газовой смеси после тройника
нейтрализации: она не должна быть выше 240 °С.
Нейтрализованная паро-газовая смесь и
солевой раствор проходят последовательно трубное пространство теплообменника 10
и котлов-утилизаторов 7 и 8. Охлаждение паро-газовой смеси в
котлах-утилизаторах проводится за счет испарения парового конденсата, подаваемого
центробежным насосом из цеховой емкости-сборника. Из котла-утилизатора 7 отводится
пар давлением 5—6 кгс/см2, а из котла-утилизатора 8 пар
давлением до 3 кгс/см2.
Пар из котлов-утилизаторов направляют
в соответствующие коллекторы. Его используют при ректификации водно-спиртового
конденсата, а избыток направляют в общезаводскую сеть. Паровой конденсат возвращают
в цеховую емкость-сборник. Для компенсации потерь парового конденсата
предусмотрена подача в емкость умягченной воды и парового конденсата из
общезаводских коллекторов.
После котла-утилизатора 8 паро-газовая
смесь и водно-спиртовый конденсат поступают в сепаратор 11, где
конденсат отделяется от паро-газовой смеси. Паро-газовая смесь проходит затем
последовательно трубное пространство теплообменника 5 и холодильника 6,
в которых происходят охлаждение циркулирующего газа до 35 °С и конденсация
паров спирта и воды. Обратный газ и водно-спиртовый конденсат из холодильника 6
поступают в скруббер 13. Там спирт из циркулирующего газа отмывают
фузельной водой, получаемой при ректификации «концентрированного»
водно-спиртового конденсата. Обратный газ из скруббера 13 поступает в
кольцевой коллектор, а водно-спиртовый конденсат («концентрированный»)
дросселируют до давления не выше 6 кгс/см2 и отводят в емкость 12(1).
Оттуда «концентрированный» водно-спиртовый конденсат проходит через
межтрубное пространство теплообменника 14, где подогревается, и уходит
на ректификацию. «Слабый» водно-спиртовый конденсат из сепаратора 11
дросселируется до давления не более 6 кгс/см2, поступает ,в емкость 12(11),
далее проходит теплообменник 14, где охлаждается, и тоже направляется
на ректификацию. Часть конденсата после холодильника 14 проходит
межтрубное пространство холодильника 15 и поступает в емкость 16 на
приготовление подщелоченного водно-спиртового конденсата. Избыток «слабого» и
«концентрированного» водно-спиртового конденсата при необходимости сбрасывают в
емкость 20. Для подачи конденсата из емкости 20 на ректификацию
установлен насос 21.
В газоотделителях 12(1) и 12(11)
вследствие сброса давления до 6 кгс/см2 происходит выделение
газов, растворенных в конденсате. Эти отдуваемые газы, проходя имеющийся .на
каждой емкости 12 небольшой скруббер с насадкой, орошаемой фузельной
водой для отмывки паров спирта, по коллектору отдувки низкого давления поступают
в цех газоразделения (совместно с газом пиролиза).
Для вывода из. системы инертных газов
(метан, этан и др.) часть газа из верхней части кольцевого коллектоpa при 40—45
кгс/см2 передают через подогреватель в цех газоразделения совместно с
газом пиролиза.
Обычно «концентрированный» и «слабый»
конденсат подвергают ректификации в разных колоннах, но возможна и совместная
переработка в одной колонне при условии подачи их на разные тарелки. При этом
«концентрированный» конденсат вводят в колонну на несколько тарелок выше по
отношению к «слабому». Ниже приведена схема ректификации только «концентрированного»
конденсата, так как работа и устройство колонн и соответствующего
оборудования одинаковы.
Ректификационная колонна состоит как
бы из двух колонн, поставленных одна на другую. Нижняя часть колонны
называется исчерпывающей, а верхняя — укрепляющей. Границей между ними служит
тарелка питания (17-я при переработке «концентрированного» конденсата, 24-я в
случае «слабого»), на которую непрерывно подается сырье.
Исчерпывающая часть колонны служит
для извлечения остатков легкокипящего компонента (спирта) из вы-сококипящего
(воды). Эта часть соединена с трубчатым кипятильником 14 обогреваемым
водяным паром. В кипятильнике происходит частичное испарение циркулирующего
через неге кубового продукта (фузельной воды). Циркуляция фузельной воды
происходит за счет перепада давлений, создаваемого столбами некипящей жидкости
в кубе и кипящей в кипятильнике при «110°С и 0,5 кгс/см2. Фузельная
вода из куба колонны 1 проходит водяной холодильник 13, где
охлаждается до 40 °С. Часть фузельной воды после холодильника 13 сбрасывают
в канализацию, а остальное поступает в емкость 12 для орошения скруббера
в отделении гидратации. Фузельная вода из куба колонны, перерабатывающей
«слабый» водно-спиртовый конденсат, после холодильника сбрасывается в
канализацию.
Пары спирта-ректификата с верха
колонны 1 при 90 °С и 0,2 кгс/см2 поступают в дефлегматор 2,
где конденсируются и охлаждаются водой. Конденсат из дефлегматора 2 поступает
в емкость 16, откуда насосом 15 частично подается в виде флегмы в
верхнюю часть колонны 1; остальной конденсат (спирт-ректификат) направляется
на очистку от ацетиленовых соединений. Несконденсировавшиеся в дефлегматоре 2
пары спирта поступают в конденсатор 3, где конденсируются; конденсат
также направляется в емкость 16.
Полученный в колонне 1 спирт-ректификат
подогревается очищенным спиртом в теплообменнике 4 и через паровой
подогреватель 5 поступает в колонну 6, где от спирта отгоняется
ацетилен. Вместе с ацетиленом уходит также некоторое количество эфира,
альдегида и спирта. Температуру в кубе колонны 6 поддерживают в
интервале 80—90 °С за счет обогрева глухим паром, подаваемым в кипятильник 20.
Из куба колонны 6 отбирается готовый спирт-ректификат. Он проходит
теплообменник 4, водяной холодильник 19 и поступает в емкость 18,
откуда насосом 17 откачивается на склад.
Отходящий с верха колонны 6 поток
проходит водяной холодильник 7 и поступает в колонну 8 для извлечения
остатков спирта. С верха этой колонны пары, содержащие ацетилен, направляются в
дефлегматор 9, флегма из которого стекает в сборник 23, а оттуда
насосом 22 подается на орошение колонны 8. Несконденси-ровавшиеся
пары из дефлегматора 9 идут в рассольный конденсатор 10, оттуда
конденсат стекает в сборник 18. При наличии ацетилена в спирте отбор
ведут в емкость 16, а несконденсировавшиеся газы направляют в линию
отдувки низкого давления. В кубе колонны 8 поддерживают температуру 60°С
за счет обогрева глухим паром, подаваемым в кипятильник 21. Выводимый из
куба колонны 8 спирт поступает в емкость 16.
3.1.3
Катализаторное
отделение
Технологическая схема этого отделения изображена на
рис. 3. Шариковый силикагелевый носитель поступает от поставщика в бумажных
крафт-мешках.
Взвешенный носитель загружают
электроподъемником в аппарат 4 на пропаривание. Пропаривание предназначено
для увеличения диаметра пор носителя с целью предупреждения его растрескивания
при пропитке кислотой. Загруженный пропарочный аппарат герметично закрывают и
нагревают горячим воздухом до 155 °С. Воздух в аппарат 4 подается
воздуходувкой 1 через осушитель 2 и паровой подогреватель 3
Затем носитель в аппарате 4 разогревают до 190—200 °С за счет тепла
острого пара, пропускаемого через аппарат и выпускаемого в атмосферу. При
температуре носителя 170 °С давление в аппарате 4 постепенно поднимают
до 18 кгс/см2. При этом давлении носитель пропаривают в течение 1—2 суток;
конденсат и пар в небольшом количестве дренируют.
После пропаривания прекращают подачу
острого пара и доводят давление в аппарате 4 до атмосферного. Аппарат
охлаждают до 40—50 °С, продувая воздухом. Пропаренный носитель выгружается
давлением воздуха в. приемный переносной бункер 12. Бункер с носителем с
помощью электротельфера и грузового лифта поднимают на загрузку через сито 5 в
печь 6 для прокаливания. Отсеянную мелочь собирают в мешки и вывозят.
Прокаливание свежего пропаренного
носителя в печи 6 проводится топочными газами при 650 °С.
Топочные газы образуются в топке 7
в результате сгорания метано-водородной фракции в токе воздуха, подаваемого
вентилятором 8. Прокаленный носитель периодически выгружают, затем его
взвешивают, отсеивают на полигональном сите 9 от мелочи и крошки и загружают
в ванну 10, заполненную фосфорной кислотой. Отсев (пыль и мелочь)
ссыпают в мешки и вывозят.
Раствор фосфорной кислоты готовят в
смесителе 17 путем разбавления водой смеси отработанной и свежей кислот.
Отработанную фосфорную кислоту заливают всмеситель из отстойника 14, а
свежую закачивают центробежным насосом 18 из емкости 19. Свежая
ортофосфорная кислота прибывает в цех в железнодорожных цистернах. Ее сливают
из цистерны по гибкому шлангу в приемную емкость 20 с помощью вакуума,
создаваемого вакуум-насосом 22. Из емкости 20, кислота
откачивается насосом 18 в емкость 19. Массу в аппарате 17 перемешивают
насосом 18. Готовый раствор откачивают из смесителя 17 насосом 18
на пропиточный узел в сборник 15. Оттуда фосфорную кислоту заливают
в пропиточную ванну 10.
Пропитку носителя ведут в течение 2
ч. По окончании пропитки сливают кислоту из ванны в отстойник 14 для
отделения от взвеси. Пропитанный носитель выгружают из ванны через нижний люк в
сушилку 11. Сушку ведут горячим воздухом, нагретым в паровом
пластинчатом калорифере 23 до 130—140°С. Горячий воздух движется по
сушилке противотоком к катализатору и выходит в, атмосферу. Воздух в сушилку 11
подают вентилятором 13. Готовый катализатор поступает на сито 24 для
отсева мелочи и далее в приемные бункеры 12. Партию из 8—9 бункеров с
катализатором и одного бункера с прокаленным носителем транспортируют
автопогрузчиком в отделение гидратации этилена.
3.2 Основное и вспомогательное оборудование, его
характеристика и обслуживание
В процессе производства
этилового спирта выполняются разнообразные операции — перемещение, нагрев и
охлаждение продуктов, разделение жидких и газообразных потоков, ректификация,
пропитка носителя фосфорной кислотой и др. Эти операции проводят с применением
соответствующей аппаратуры. Для нормального проведения технологического
процесса и обеспечения безопасных условий труда обслуживающего персонала
аппаратура и оборудование должны быть прочными и долговечными.
Реактор предназначен для проведения
гидратации этилена; конструктивно он представляет собой пустотелый вертикальный
аппарат. Реактор состоит из цилиндрического кованого корпуса внутренним
диаметром 1260 мм и двух приваренных к нему сферических днищ. Общая высота
аппарата 10600 мм. Корпус, днища и люки изготовлены из стали. Температура в
аппарате допускается до 310°С, Давление до 80 кгс/см2. Реактор
теплоизолирован.
В реактор загружают
фосфорнокислотный катализатор, который создает кислую коррозионную среду. Для
защиты от коррозии аппарат футерован медными листами, полностью прикрывающими
его внутреннюю поверхность. Медную футеровку навешивают на внутренние стенки
реактора кольцевыми поясами с помощью сварки. Пространство между поясами
тщательно герметизируют. Медную футеровку укрепляют с таким расчетов чтобы она
не сползала при выгрузке отработанного катализатора. Под влиянием рабочей среды
футеровка становится хрупкой, и ее герметичность в таком состоянии может легко
нарушаться. Поэтому футеровку после каждого пробега катализатора тщательно
осматривают и при наличии растрескиваний заменяют дефектные места.
Реактор имеет два люка
(верхний для загрузки катализатора и входа исходной парогазовой смеси и нижний
для выгрузки катализатора и выхода продуктов), три штуцера для термопар и
штуцер в верхней части для аварийного сброса давления через предохранительный
клапан (или вручную - по шунту к клапану).
Загрузку катализатора проводят в
следующем порядке. Устанавливают тройник нейтрализации на нижнем люке реактора,
причем между фланцами нижнего люка и тройника устанавливают вершиной вверх
конус из медного листа с отверстиями. Число отверстий в конусе делается таким,
чтобы их суммарная площадь была бы меньше сечения трубопровода на выходе из
реактора. Через верхний люк на верх конуса насыпают 0,4 м3 колец Рашига, 0,5—1 м3 не пропитанного кислотой носителя и 9—10 м3
катализатора. Катализатор к месту загрузки Доставляют в бункерах, вмещающих 1 м3 катализатора Бункер из катализаторного отделения в отделение гидратации привозят
автопогрузчиками. Далее бункер на тележке передвигают в монтажный проем, откуда
пневмотельфером поднимают на верхний этаж. Выгружают катализатор через нижний
люк, самотеком в бункер.
При эксплуатации реактора
требуется учитывать его конструктивные особенности. Например, нельзя резко
сбрасывать давление во избежание вспучивания футеровки. Нужно выдерживать
заданное соотношение между циркулирующим, газом и паром во избежание
конденсации пара и, следовательно, коррозии стенок реактора.
Скруббер предназначен для разделения
водно-спиртового конденсата и циркулирующего газа и отмывки из последнего
несконденсировавшихся паров спирта фузельной водой. Контакт между газом и водой
при отмывке осуществляется на кольцах Рашига, загруженных слоем высотой 2,5 м. Для отделения капель жидкости, уносимых газом, в верхней части аппарата установлен отбойный
пакет из нескольких вертикальных рядов проволочной сетки. Водно-спиртовый
конденсат собирается в кубе аппарата.
Аппарат состоит из цилиндрического
корпуса и двух приваренных днищ. Входной штуцер для парожидкостной смеси
расположен в кубовой части аппарата, а штуцер ввода фузельной воды — выше слоя
колец Рашига. Над входным штуцером установлена опорная решетка для колец
Рашига. Аппарат имеет люки для внутреннего осмотра, а также для выгрузки колец
Рашига. Ректификационная колонна предназначена для ректификации
водно-спиртового конденсата. Она представляет собой цилиндрический аппарат с 50
решетчатыми тарелками. Колонна имеет 4 люка для внутреннего осмотра аппарата и
чистки тарелок. Загрязняются обычно тарелки исчерпывающей части; их
периодически очищают. Тарелка представляет собой металлический диск с рядами
параллельных прорезей размером 150X4 мм. Тарелка не имеет сливных стаканов; она
состоит из. отдельных листов - секций, укрепленных на балках каркаса планками и
болтами. Тарелки устанавливают таким образом, что прорези двух соседних тарелок
оказываются перпендикулярными друг другу. Тарелка питания представляет собой
диск с большими отверстиями для прохода паров и маленькими отверстиями для
слива жидкости; отверстия равномерно расположены по всей тарелке. Тарелки
питания устанавливаются на приеме сырья и на приеме флегмы. Колонна оснащена
штуцерами для подвода пара от кипятильника, для отвода паров в дефлегматор, для
приема флегмы и питания, для отвода кубового продукта, для подключения
регулятора уровня в кубе, бобышками для отбора импульсов давления и
температуры.
3.2.2 Теплообменная аппаратура
В производственных условиях
горячие потоки охлаждаются вначале в теплообменниках, где они отдают свое тепло
холодным потокам, поступающим в процесс, а затем — в холодильниках. При
регенерации тепла горячих потоков повышается КПД тепла по производству,
уменьшается расход воды на охлаждение и вырабатывается пар давлением 3 и 5
кгс/см2. В производстве этанола применяют теплообменные аппараты
следующих типов:
1)
теплообменники,
подогреватели, котлы-утилизаторы, холодильники с плавающей головкой;
2)
кипятильники,
кожухотрубные холодильники жесткого типа;
3)
калориферы.
Устройство кожухотрубного
теплообменника с плавающей головкой показано на рис. . Он состоит из
металлического корпуса, в котором помещен пучок трубок, ввальцованных в трубные
решетки, и крышек. Одна из решеток, снабженная внутренней крышкой, может
свободно перемещаться внутри корпуса, что позволяет компенсировать тепловые
расширения трубок. Такая подвижная решетка называется плавающей головкой.
Передняя крышка аппарата имеет входной и выходной штуцеры, а также
вспомогательные штуцеры (воздушник и для дренажа). В переднюю крышку встроена
глухая перегородка, делящая ее на две камеры: приемную и выходную. На передней трубной
решетке имеется продольный паз для захода края перегородки крышки.
В трубах теплообменника в верхней
половине газ движется по направлению к плавающей головке, а в нижней наоборот.
Поворот газа с изменением направления: хода происходит в крышке плавающей головки,
которая в отличие от передней крышки не имеет перегородок. Крышку плавающей головки
крепят к плавающей трубной решетке с помощью двух струбцин. Передняя головка
аппарата имеет фланцевое соединение, включающее сразу три крупных фланца: от
крышки, от трубной решетки и от корпуса. Для фланцевых соединений
теплообменников, находящихся под давлением 64—80 кгс/см2, в качестве
прокладочного материала обычно применяются металлические кольца (материал —
сталь Армко). На линиях пара низкого давления и воды применяются паронитовые
прокладки. К теплообменникам с плавающей головкой относятся все теплообменники
отделения гидратации. Подробнее остановимся на особенностях конструкции и
эксплуатации каждого из них.
Теплообменник 5 состоит из
нескольких аппаратов, включенных последовательно. Они работают в относительно
мягких температурных условиях и реже других выходят из строя. Трубное и
межтрубное пространства теплообменников практически не загрязняются. Для
увеличения скорости прохождения газа по межтрубному пространству там
установлены перегородки, заставляющие газ идти по винтообразной линии, что
улучшает теплообмен. Штуцер для входа газа в межтрубноё пространство расположен
на корпусе снизу, чтобы поток поступал на поверхность трубок перед пла вающей
головкой. Выходной штуцер расположен на корпусе сверху с расчетом теплообмена
выходящего газа с входящим. На задней крышке имеются вспомогательные штуцеры
(воздушник и для дренажа).
Теплообменник 10 состоит из
нескольких аппаратов. По трубной части его проходит обратный газ сразу же после
тройника нейтрализации. Вследствие высокой температуры в межтрубной части
аппарата (в застойных зонах) образуется полимерная масса, которая ухудшает
теплообмен.
Паровой
подогреватель 4 работает в
сложных температурных условиях. Межтрубное пространство всегда чистое, так как
по нему проходит пар высокого давления. В трубках возможно образование
полимерной массы из-за высокой температуры, поэтому при вскрытии аппарата
трубки следует прочищать.
Котлы-утилизаторы 7 и 8 работают в
сложных условиях из-за колебания уровня парового конденсата в межтрубном
пространстве. При изменении уровня обнаженные трубки нагреваются сильнее и
благодаря тепловому расширению испытывают большие механические нагрузки, так
как концы трубок жестко закреплены. Это является причиной негерметичности
аппарата как в узле вальцовки трубок, так и. в теле самих трубок. Корпус
котлов-утилизаторов рассчитан на низкое давление. Пар выходит через сухопарник;
там осуществляется отбой капель воды. Сухопарник приваривается непосредственно
к корпусу. На корпусе котла имеются два нижние штуцера для ввода парового
конденсата, два штуцера для подключения регулятора уровня и верхний
штуцер-воздушник. На задней крышке котла имеется дренажный штуцер, а наверху —
бобышка для подключения манометра.
Холодильник 6 состоит из
нескольких одинаковых менников. При грязной промышленной воде в межтрубном
пространстве образуется накипь на трубках и на крышке плавающей головки. В
процессе эксплуатации возможно образование газовых пробок из-за пропуска газа,
что может привести к повышению температуры на выходе обратного газового потока.
В отделении
ректификации все теплообменники — кожухотрубные, жесткого типа. Водно-спиртовый
конденсат и фузельная вода являются загрязняющими средами, т. е. они дают на
поверхности теплообмена отложения полимеров и солей, которые периодически
приходится удалять. Дефлегматор и конденсатор, работающие на промышленной воде,
могут загрязняться только примесями, имеющимися в воде. Обычно теплообменное
оборудование в отделении ректификации работает удовлетворительно.
3.2.3 Емкостное
оборудование
Газоотделитель 12(1) представляет
собой горизонтальную полую цилиндрическую емкость, имеющую вверху промывную
колонку с насадкой из колец Рашига. Емкость 20 —
вертикальный цилиндрический аппарат с расположенным внутри по дну змеевиком для
подогрева в зимнее время. Остальные аппараты — полые цилиндрические емкости.
3.2.4 Оборудование
катализаторного отделения
Осушитель
воздуха 2 (см. рис. 3) — вертикальный цилиндрический аппарат,
заполненный активной окисью алюминия.
Пропарочный
аппарат 4 — вертикальный цилиндрический аппарат со
сферическими днищами.
Сито 5 — шестигранный барабан, обтянутый металлической
сеткой (размер отверстий 2,5 мм). Аппарат, предназначен для отсева пыли и крошки от носителя.
Прокалочная
печь 6 — вертикальный прямоугольный аппарат шахтного типа,
выложенный изнутри огнеупорным кирпичом и снабженный трубчатым теплообменником
для охлаждения воздухом носителя, выгружаемого из аппарата. На верху аппарата
имеется приемный бункер, обеспечивающий равномерное распределение носителя и
служащий затворным устройством от попадания дымовых газов в помещение.
Топка 7—
горизонтальный цилиндрический аппарат с плоским днищем; выложен изнутри
огнеупорным кирпичом.
Сито 24 — сито
«Ротекс» с электроприводом. Предназначено для отсева пыли и мелочи от готового
катализатора.
Пропиточная
ванна 10—вертикальный
цилиндрический аппарат со сферическим днищем.
Сборник 16 —
вертикальный цилиндрический аппарат с коническим днищем.
3.2.5 Компрессоры и
насосы
Компрессор 2 (см. рис.
1)—поршневого типа. Служит для сжатия этиленовой фракции, поступающей из цеха
газоразделения, до 70 кгс/см3. Компрессор 3 — тоже
поршневого типа; служит для обеспечения циркуляции газа в агрегате гидратации.
Для перекачки
жидких продуктов применяются насосы различных типов — поршневые,
центробежные и др. Поршневые насосы используются для подачи на нейтрализацию
подщелоченного водно-спиртового конденсата и для подачи фузельной воды на отмывку паров спирта из
циркулирующего газа в скруббер 13. Остальные
насосы, применяемые в производстве, являются центробежными или других типов,
обеспечивающих заданные условия перекачки.
3.2.6 Вспомогательное
оборудование
К
вспомогательному оборудованию относятся: бункеры, в которых транспортируют
катализатор, тельферы, мостовые краны, дренажные емкости, масляное хозяйство,
емкости парового хозяйства цеха, вентиляционное и отопительное оборудование,
воздушный компрессор. Вспомогательное оборудование косвенным образом
способствует успешному ведению технологического процесса.
Большое
значение в производстве придается вентиляции, которая делится на приточную и
вытяжную. Приточная вентиляция выполняет и отопительную функцию, подавая в
зимнее время теплый воздух, нагретый в калориферах. Приточная вентиляция
улучшает условия труда за счет уменьшения концентрации углеводородов,
выделяемых через неплотности в оборудовании. Приточная вентиляция имеется в
компрессорном, насосном и операторном помещениях, в отделениях гидратации и
катализаторном. Вытяжная вентиляция служит для отсоса паров жидкостей и тяжелых
газов. Отсасывающие отверстия коробов располагаются обычно низко над полом.
Вытяжная вентиляция имеется в насосных и служит также для улучшения атмосферы в
помещениях.
В отделении
гидратации имеется вентиляционная система, отсасывающая катализаторную пыль в
период загрузки и выгрузки катализатора.
Пыль, захваченная воздухом, задерживается в 72-рукавном фильтре с
электроприводом. При этом пыль с внутренней поверхности рукава стряхивается
вниз в сборник. Воздух, профильтрованный через рукава, выходит из фильтра.
Такой же фильтр для улавливания пыли установлен в катализаторном отделении.
Дренажные
емкости служат для сбора продуктов из аппаратов, которые освобождают перед
ремонтом. Собранный продукт периодически откачивается из этих емкостей в
специальный сборник. Наличие дренажных емкостей уменьшает сбросы, улучшает атмосферу
цеха.
Отопительное
оборудование (калориферы) подогревает воздух, подаваемый приточной вентиляцией
в помещение. Необходимо следить, чтобы в холодную погоду калориферы не
замерзли.
Грузоподъемное
оборудование служит для подъема и перемещения грузов по территории.
Воздушный
компрессор служит для обеспечения пневмотельфера воздухом.
3.3 Характеристика сырья и продукта
Основным сырьем для производства этилового спирта
методом прямой гидратации является этилен.
Этилен СН2=СН2, мол.вес.28,05, бесцветный газ со слабым запахом; т.пл. 169,5о; т.кип. - 103,8о;
теплота сгорания 333,5 ккал/моль; т.воспл.
546о (в воздухе); растворимость
газообразного этилена в одном объеме растворителя: 0,25 в
воде, 3,59 в спирте, хорошо растворим в эфире. Пределы
взрывоопасных концентраций в воздухе 3-34 об.%. При
нагревании выше 350-400о разлагается: 3С2Н4=2СН4+2СНºСН; при температуре белого каления этилен
преимущественно дегидрируется: СН2=СН2®НСºСН+Н2.
В светильном и коксовом газе находится 3-5% этилена; в
некоторых газах нефтепереработки его содержание достигает 20%.
Этилен - очень реакционноспособное соединение; его
химические свойства обусловлены главным образом межуглеродной двойной связью и
проявляются в большой склонности к реакциям присоединения. Этилен
- один из важнейших исходных продуктов синтеза органических соединений.
При действии хлора на этилен в органическом растворителе
( обычно в дихлорэтане) в присутствии металл.или хлорного железа гладко
образуется дихлорэтан:
СН2=СН2 + Cl2 ® Cl2CH2CH2Cl
Дихлорэтан широко применяют как растворитель и сырье для
получения винилхлорида и др. В присутствии АLСI3 этилен
алкилирует бензол и образует этилбензол. В присутствии ионных катализаторов типа АLСI3 или ВF3 возможно алкилирование этиленом изопарафинов с
образованием сильно разветвленных алканов, представляющих интерес в качестве
авиационного топлива.
С НСI этилен при -30о дает этил хлористый,
применяемый для этилирования, например, в производстве тетраэтилсвинца.
С хлоридами серы этилен образует дихлордиэтилсульфид
(иприт) (СIСН2СН2)2S. Реакцией этилена с формальдегидом в уксусной
кислоте в присутствии Н2SО4 можно
получить ацетат триметиленгликоля его омылением - триметиленгликоль.
Реакцией этилена с СО и Н2 можно получить пропионовый альдегид, а с СО2
- пропионовую кислоту.
К числу производств, основанных на
использовании этилена и получивших широкое промышленное развитие,
относятся в первую очередь его полимеризация, его окисление в окись
этилена, гидратация в этиловый спирт.
Из общего количества используемого в различных странах
этилена 25-40% расходуется на производство полиэтилена, 20-40%
перерабатывается в спирт, до 25% идет на получение окиси этилена, »10% приходится на долю производства стирола (через
этилбензол), примерно столько же на дихлорэтан и другие
хлорпроизводные.
При содержании в воздухе около 0,1% этилена
фрукты и овощи (особенно лимоны, виноград, помидоры)
ускоренно созревают. В
медицине этилен применяют для общего наркоза при хирургических операциях.
Этилен можно получать многими способами, в
частности дегидратацией спирт, пропуская его пары над Al2O3 при 350о-400о. При
этом образуется сравнительно чистый этилен. Метод применяется не только в лабораторной
практике, но и в небольшом масштабе и в производстве. В
странах, бедных нефтью, этилен иногда производят частичным
гидрированием ацетилена при 180 - 320о над Рd -
катализатором на силикагеле. Этилен можно также получать реакцией этана с
избытком окиси углерода над Fе2О3 при 800 - 900о,образующаяся
смесь этилена с СО пригодна для непосредственного получения пропионового
альдегида.
Однако основные методы получения дешевого этилена в
крупном масщтабе связаны с переработкой нефти и природного газа. Так, газы
парофазного или жидкофазного крекинга нефтепродуктов при 700 - 800о
содержат 17 - 20 % этилена. После разделения газов методами дробной
абсорбции, глубокого охлаждения и ректификации под давлением
выделяют этиленовую фракцию, с 90 - 95% этилена и примесью 1-3% пропилена, 1-4%
метана и 3-6% этана.
В настоящее время основным источником низших олефинов
является пиролиз углеводородного сырья, проводимый с целью производства этилена.
Попутно при пиролизе получают другие ненасыщенные газообразные углеводороды -
пропилен, бутены и бутадиен. Одновременно образуются
жидкие продукты (смола пиролиза), которые содержат также ценные углеводороды, как
изопрен, циклопентадиен, бензол, толуол,
ксилолы и нафталин.
Основным сырьем процесса пиролиза с целью получения
газах, газовые бензины прямой перегонки нефти, а
также рафинад каталитического риформинга, остающийся после удаления ароматических
углеводородов. В качестве сырья пиролиза применяют также средние и
тяжелые нефтяные фракции и даже сырую нефть.
Процесс производства этилена и других олефинов из
углеводородного сырья включает стадии пиролиза углеводородов,
компримирования газа пиролиза, удаления тяжелых углеводородов, осушки,
разделения (газофракционирование), удаление сероводорода,
диоксида углерода и ацетилена. этилена являются этан, пропан
и бутан, содержащиеся в попутных газах нефтедобычи и в
нефтезаводских
Этиловый спирт - конечный продукт производства. Физические
свойства этилового спирта описаны во введении данной работы.
Рассмотрим теперь, что же представляет этиловый спирт по своим
химическим свойствам. При взаимодействии этилового спирта с
щелочными металлами образуются этилаты: 2С2Н5ОН + 2Nа®2С2Н5ОNа + Н2; водой этилаты омыляются до С2Н5ОН и NаОН. При действии на этиловый спирт кислот образуются
сложные эфиры. Концентрированная H2SO4 образует с этиловым спиртом этилсерную кислоту
С2Н5ОН + Н2SО4 ® С2Н5НSО4 + Н2О;
При взаимодействии этилового спирта с уксусной
кислотой в присутствии конц. серной кислоты или других катализаторов
получается этилацетат:
С2Н5ОН + СН2СООН ® С2Н5ОСОСН3 + Н2О
При дегидрировании этилового спирта в присутствии
катализаторов(серебро, медь) образуется ацетальдегид:
С2Н5ОН ® СН3СНО
Если пропускать пары этилового спирта над сложным
катализатором при 380-400о нормальном давлении,
происходит дегидратация и дегидрогенизация этилового спирта (способ С.В.
Лебедева) с образованием бутадиена - 1,3 (дивинила):
2С2Н5ОН® СН2 = СН -
СН = СН2 + 2Н2О + Н2
Нагреванием этилового спирта до 140о в
присутствии Н2SО4 образуется диэтиловый эфир:
2C2Н5ОН
® (С2Н4)2О + Н2О
Над активированной окисью алюминия этиловый спирт
дегидратируется до этилена:
С2Н5ОН® СН2=СН2 + Н2О
При каталитическом взаимодействии этилового спирта с
аммиаком образуются моно-, ди- и триэтиламины.
Этиловый спирт - наркотик,
возбуждающе действующий на организм. Длительное воздействие больших доз может
вызвать тяжелые органические заболевания нервной системы, печени, сердечно-сосудистой
системы, пищеварительного тракта и т.д.
Предельно-допустимая концентрация этилового спирта в
воздухе рабочей зоны 1000 мг/м3 .
4 Расчётная
часть
4.1 Материальные расчёты и составление материального
баланса процесса
СН2 =СН2 + Н2О® С2Н5ОН
На образование 1кмоль спирта идёт 22,4 м3 этилена:

С учётом степени превращения на
стадиях процесса:

Вместе с этиленом будет подано этана
в количестве:

Всего этан – этиленовой фракции:
2072,1554м3 +6216,4662м3
= 8288,6216 м3
Определим расход этилена:
G (C2H4) = (6216,4662 ּ 28)/22,4 = 7770,5828 кг
Определим расход этана:
G (C2H6) = (2072,1554 ּ 30)/22,4 = 2775,2081 кг
Всего этан – этиленовой фракции:
7770,5828 кг + 2775,2081 кг =12276,3кг = 10,5457909 тонн
Для получения 1 кмоль этанола
требуется 1 кмоль воды. Определим расход воды для производства 12000 кг
этилового спирта:
G (Н2O) = 18 ּ 12000 / 46 = 4695,6522 кг
Побочных продуктов с учётом степени
превращения образуется:

Таблица 1. Материальный баланс.
Приход |
кг
|
Расход |
кг
|
Этиленовая фракция
Вода
|
10545,7909
4695,6522
|
Этанол
Этан
Побочные продукты
|
12000
2775,2081
466,235
|
Итого |
15241,4431 |
Итого |
15241,4431 |
4.2
Тепловые расчёты и
составление теплового баланса процесса
Тепловой баланс процесса рассчитываем
на основании уравнения:

где G – количество
вещества, с – средняя теплоемкость этого вещества, t – температура, отсчитанная от какой-либо точки (обычно от 00С).
Рассчитываем количество теплоты,
вносимое водой:

Рассчитывает количество теплоты,
вносимое этиленовой фракцией:
Теплоёмкость этиленовой фракции
рассчитываем по уравнению:


Определим количество теплоты, уносимое этаном: t=2200С
Q (С2H6) = 2775,2081 ּ (5,75 +
175,11 ּ 10-3 ּ 493 - 57,85 ּ 10-6 ּ 4932) ּ (320-220) =17321,48253
кДж/час
Определим количества теплоты, уносимо этанолом:
Q (C2H5OH) = G ּ с ּ t, t=2200С
G (C2H5OH) = 16000
кг/час
с= (19,07 + 212,7 ּ 10-3 ּ 493
– 108,6 ּ 10-6 ּ 4932) = 97,536 Дж/мольּК
Q (C2H5OH) = G ּ с ּ t =
12000 ּ
97,536 ּ
(300-220) = 93634,53946 кДж/час
Количество теплоты, уносимое из реактора с помощью
холодильников:
Qп
=Q (H2O) + Q (эт.фр.) – Q (C2H6)-Q (C2H5OH)=77805,68913+ 106606,1794-
-17321,48253- 93634,53946=73455,84654 кДж/час
Расход
воды в холодильниках:
с (Н2О)
= 33,61 Дж/моль ּ К
G(воды в холодильниках) = Qп/(с(воды) ּ (tкон – tнач)) = 73455,84654 ּ 1000/33,61 ּ (300-220)
= =27319,19315 кг/час
Таблица 2. Тепловой баланс
Приход |
кДж |
Расход |
кДж |
Этиленовая фракция
Вода
|
106606,1794
77805,68913
|
Этанол
Этан
Вода в холодильниках
|
93634,53946
17321,48253
73455,84654
|
Итого |
184411,8685 |
Итого |
184411,8685 |
CH2 = CH2(г) + H2O(пар) < = >C2H5OH(г) T=493K
Зависимость удельной изобарной теплоёмкости от
температуры выражается уравнениями:
– для органических веществ
– для неорганических веществ
Изменение удельной изобарной теплоёмкости считается по
уравнению:

Изменение удельной изобарной теплоёмкости для данной
реакции:

Δа=19,07-4,196=14,874
Δb=(212,7-154,59) ּ 10-3=58,11 ּ 10-3
Δc=(-108,6+81,09) ּ10-6=-27,51 ּ10-6

Энтальпия реакции при данной температуре
рассчитывается по формуле:

=
= - 45,74 кДж/моль
= - 45,74
кДж/моль + ∫((14,874+58,11 ּ 10-3Т - 27,51 ּ10-6Т2)
–
- (30,00+10,71 ּ 10-3Т + 0,33 ּ 105Т-2))dT
Дж/моль = - 45,74 кДж/моль +14,874
ּ (493- -298)
+ 0,5 ּ 58,11 ּ 10-3 ּ (4932-2982) - 0,33 ּ 27,51 ּ10-6(4933-2983) – (30 ּ (493-298) + 0,5 ּ 10,71 ּ 10-3(4932-2982) –
0,33 ּ 105(493-1-298-1)=
-45,74 кДж/моль + 1,785 кДж/моль= - 43,955 кДж/моль
Энтропию реакции при 493 К рассчитаем по уравнению:

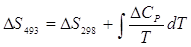


-126,14 + ((14,874 ּ Т-1 +58,11 ּ 10-3 - 27,51
ּ10-6Т)
– (30 ּТ-1 + 10,71 ּ 10-3 + +0,33 ּ 105Т-3)dT = -
126,14 + 14,874ln(493-298) +58,11 ּ 10-3(493-298) – 0.5 ּ 27,51 ּ10-6 (4932-2982)
– 30 ּ ln(493-298)
- 10,71 ּ 10-3(4932-2982) – 0.5 ּ 0,33 ּ 105(493-2-298-2) =
=-198,66 Дж/моль ּ К
Энергия Гиббса для реакции при 493 К вычисляется по
уравнению:


Так как реакция является обратимой, найдём значение
константы равновесия:

5 Отходы и их
обезвреживание
Процесс производства синтетического этилового спирта
методом прямой гидратации этилена связан с применением и образованием токсичных,
взрывоопасных и пожароопасных веществ.
Для уменьшения и предотвращения вредных выбросов в
атмосферу газов, содержащих токсичные углеводороды,(этилен,
диэтиловый эфир, ацетальдегид и др.) имеются следующие
возможности:
·
строгое соблюдение
технологического режима (при этом снижается количество выбросов через
предохранительные клапаны и воздушники, уменьшаются частота остановок и связанное с
ними сбрасывание газов);
·
монтаж и эксплуатация
оборудования в соответствии с правилами (это предупреждает газовые выбросы
через неплотности).
Процесс синтеза этилового спирта сопровождается
значительным уносом фосфорной кислоты, которая может вызвать коррозию оборудования и
трубопроводов. Поэтому одной из стадий процесса является
нейтрализация продуктов реакции, выходящих из гидрататора в парогазовой фазе
путем взаимодействия с подщелоченным водно-спиртовым конденсатом. Образующиеся
при нейтрализации соли фосфорной кислоты (0,4-0,5 кг на 1 т спирта) растворяются в водно-спиртовом конденсате
и пройдя вместе с продуктами реакции через теплообменник-рекуператор,
котлы-утилизаторы, сепараторы и т.д. поступают на узел ректификации и выводятся из
системы вместе с обратной промывной водой в канализацию.
В процессе гидратации этилена образуются побочные
продукты: диэтиловый эфир, ацетальдегид, полимеры этилена, являющиеся
отходами производства. Значительная часть этих соединений удаляется
при ректификации и очистке этилового спирта.
С целью улучшения качества спирта и снижения
содержания углеводородов в сточных водах производства синтетического этанола в
настоящее время на стадии переработки спирта-сырца проводится отвод жидкостной
фазы (в составе которой отходы производства - полимеры) с содержанием спирта 40
- 80 об. % с последующим ее разбавлением до содержания спирта
10 - 20 об. % и направлением в отстойник.
Полимеры, являясь водонерастворимыми органическими
продуктами, хорошо растворяются в этиловом спирте и в процессе
ректификации накапливаются в колонне, достигая максимальной концентрации (17 - 35 об. %) в
той части колонны, где концентрация спирта 40 - 80 об.%.
Выделившиеся при разбавлении полимеры отделяют от
водноспиртового слоя во флорентийском сосуде, выводят в сборник и далее
в канализацию, а водноспиртовой слой направляют обратно в колонну на
тарелку питания.
Способ позволяет улучшить качество стоков по
химическому поглощению кислорода на 60 - 65 %, что облегчает очистку
сточных вод на биоочистных сооружениях.
Для поддержания высокой концентрации этилена (98,5 %)в
процессе гидратации проводят отдувку циркулирующего газа,
который после отмывки паров спирта в скруббере, поступает в цех
газоразделения для переработки совместно с газом пиролиза.
Для вывода с установки инертных газов (метан, этан и
др.) часть газа из верхней части кольцевого коллектора при
40 - 45 кгс/см2 передают через подогреватель в цех
газоразделения для переработки.
6 Мероприятия
по технике безопасности, промсанитарии, пожарной безопасности и охране труда
Производство
синтетического этилового спирта относится к пожаро- и взрывоопасным
производствам. Кроме того, в цехе используются токсичные и едкие вещества.
Основными моментами, определяющими опасность в цехе, являются:
1) наличие
жидких и газообразных продуктов, образующих с воздухом взрывоопасные смеси с
низким пределом взрываемости;
2) ведение
процесса при высоких давлениях (до 100 кгс/см2) и высоких
температурах (до 450 °С);
3) наличие тока
высокого напряжения для электродвигателей;
4) токсичность
сырья, вспомогательных материалов и готовой продукции;
5) образование
зарядов статического электричества при движении газов и жидкостей по
трубопроводам и аппаратам;
6) ведение
сварочных работ внутри реакторов.
6.1 Характеристика производства по
взрыво- и пожароопасности
Процессы
гидратации этилена, ректификации и очистки спирта являются закрытыми и
осуществляются по непрерывной схеме. Появление газа или паров в
производственном помещении возможно только вследствие неисправности
оборудования или при авариях. Помещения цеха по взрываемости относятся к классу
В-1а, наружные установки к классу В-1г,
катализаторное отделение — невзрывоопасное.
По пожаро- и
взрывоопасности цех относится к категории «А», так как во всех отделениях
имеются вещества с нижним пределом взрываемости 10% и менее, а также
легковоспламеняющиеся жидкости (т. всп. 28 °С и ниже) в количествах,
достаточных для образования взрывоопасных смесей. В компрессорном зале и отделении
ректификации имеется этилен; в насосных и на установке удаления ацетилена из
спирта имеются этиловый спирт и диэтиловый эфир; в катализаторном отделении применяют
метано-водородную фракцию в качестве топлива.
Если
концентрация этих продуктов в воздухе находится между верхним и нижним
пределами взрываемости и имеется источник воспламенения, возможен взрыв; при
концентрации этих продуктов выше верхнего предела взрываемости и при наличии
источника воспламенения возможен пожар.
При
монтировании электрооборудования следует учитывать, что технологическая среда
производственных помещений установки по взрываемости имеет такую характеристику
согласно ПИВРЭ (Правила изготовления взрывобезопасного и рудничного
электрооборудования): по этилену ЗТ1, по этанолу 2Т2, по диэтиловому эфиру 2Т4
(где первая цифра — категория взрывоопасной смеси, Т1, Т2, Т4 — группы
взрывоопасности смеси).
По санитарным
условиям производство этанола относится к производствам П-д, для которых в
бытовых помещениях предусмотрены гардеробная, умывальная и душ. По количеству
выделяющегося от оборудования тепла помещения реактора и паровых коллекторов
относятся к горячим отделениям; для таких производственных помещений
предусмотрен 8-кратный обмен воздуха в час.
Этиленовая
фракция, содержащая 98—99% (об.) С2Н4. Горючий
газ. Смесь этилена с воздухом взрывоопасна, ядовита, действует на центральную
нервную систему. Предельно допустимая концентрация этилена в помещении 500 мг/м3.
Метано-водородная
фракция, содержащая 89—90% СН4 и 5—10% Н2.
Указанные вещества не ядовиты, но при большом содержании их в воздухе
затрудняется дыхание из-за недостатка кислорода. С воздухом образует
взрывоопасные смеси.
Этиловый
спирт ядовит, действует на центральную нервную систему, при
попадании в организм в небольших количествах вызывает опьянение, в больших — состояние,
близкое к наркозу, иногда заканчивающееся смертью. Предельно допустимая
концентрация паров спирта в помещении 1000 мг/м3.
Диэтиловый
эфир обладает наркотическими свойствами, действуя на центральную
нервную систему. Пары эфира с воздухом образуют взрывоопасные смеси. Предельно
допустимая концентрация паров диэтилового эфира в помещении 300 мг/м3.
Инертный
газ состоит из азота (до 86%), двуокиси углерода (до t2%) и
кислорода (до 2%); СО быть не должно. При большом скоплении инертного газа в
помещении снижается содержание кислорода, что может привести к кислородному
голоданию организма. Иногда в инертном газе содержится окись углерода; она вызывает
головные боли при вдыхании небольших количеств, обморочное состояние и смерть
при вдыхании больших количеств.
Азот не ядовит, но
при большом скоплении в помещении снижает содержание кислорода. Технический
азот, подаваемый в цех, содержит до 0,1% кислорода.
Фосфорнокислотный катализатор, содержащий не менее 48% Н3Р04 и до 52%
силикагеля. Катализаторная пыль вызывает раздражение дыхательных путей. Предельно
допустимая концентрация катализаторной пыли в помещении 2 мг/м3.
Ортофосфорная кислота (60—80%-ная) при попадании на кожу вызывает ожоги.
Едкий натр (40%-ный
раствор) — едкая жидкость. При попадании на кожу вызывает ожоги с образованием
язвочек. Особенно опасно попадание щелочи в глаза.
6.3
Основные правила работы с токсичными газами и едкими веществами
Общими
средствами защиты от углеводородных газов и паров, применяемыми в
производственных помещениях, являются проветривание помещений (естественная
вентиляция), приточная, вытяжная и аварийная вентиляция.
В качестве
индивидуальных средств защиты органов дыхания и зрения работающих используются
промышленные фильтрующие противогазы. Применение фильтрующих противогазов
возможно только в атмосфере, содержащей не менее 16% (об.) свободного кислорода
и не более 0,5°/о (об.) вредных веществ..
Общими
средствами защиты от пыли катализатора и силикагеля служат вытяжные
вентиляционные и аспирационные установки, а также воздухозаборники, устанавливаемые
в местах пылевыделения. Индивидуальными средствами защиты от пыли являются
респираторы типа «лепесток» одноразового пользования.
Защитными средствами
от едких жидкостей (кислот, щелочей) являются наголовные щитки, очки, шлем-маски
от противогазов, прорезиненные фартуки и перчатки, резиновые сапоги. При работе
со щелочью необходимо быть в хлопчатобумажной спецодежде, при работе с кислотой
— в суконной.
При
проведении работ в слабо вентилируемых помещениях, емкостях, колодцах, траншеях
и т. д. применяют шланговые противогазы. В тех случаях, когда нельзя работать в
шланговом противогазе, применяют газоизолирующий аппарат.
При
загазованности помещения первый, кто это заметил, должен сообщить в
газоспасательный отряд по телефону и начальнику смены, а сам до прибытия дежурного
по отделению должен принять меры по устранению причины загазованности, усилению
вентиляции и предупреждению обслуживающего персонала.
Взрыв или
пожар могут произойти при концентрациях углеводородов, спирта, диэтилового
эфира в интервале от нижнего до верхнего пределов взрываемости.
Возбудителями
взрыва или воспламенения являются:
1) открытое
пламя (курение или ведение огневых работ в цехе);
2) самовоспламенение
продуктов (сернистого железа, образующегося в аппаратах при наличии
сероводорода в перерабатываемом газе, а также углеводородных полимеров,
образующихся в процессе переработки непредельных углеводородов);
3) искра при
ударе металла о металл или камень;
4) образование искры
при работе на неисправном электрооборудовании;
5) статическое
или атмосферное электричество.
В целях
соблюдения мер пожарной безопасности в цехе и недопущения пожаров и загораний
необходимо весь цех (территорию, технологические установки, резервуарные парки,
склады, мастерские, служебно-бытовые помещения и прочие объекты) содержать в
чистоте и порядке. Кроме того, не допускается загромождение проезжих дорог,
подъездов, подступов к зданиям и сооружениям, путей эвакуации, проходов и
выходов из зданий, площадок вокруг производственного оборудования, подступов к
противопожарному инвентарю и средствам связи посторонними предметами.
Условия
проведения огневых работ в цехе такие:
1) в
компрессорном отделении цеха разрешаются временные огневые работы по пайке
электродвигателей, компрессоров. Двигатель, ремонтируемый с применением
временных огневых работ, отключают от коммуникаций заглушками и продувают инертным
газом до отсутствия в цилиндрах двигателя непредельных углеводородов;
2) систему
гидратации, на которой проводятся временные огневые работы, нужно остановить.
Давление из системы сбрасывают, а участок, на котором проводятся временные
огневые работы, отключают заглушками от аппаратов и коммуникаций и пропаривают
до полного отсутствия углеводородов; анализ воздуха в месте сварки должен
показывать отсутствие углеводородов;
3) при
проведении огневых работ внутри реактора требуются следующие дополнительные
условия: во время проведения огневых работ с помощью вытяжной вентиляции
отсасывают воздух из реактора; решетки под реактором закрывают асбестовым
одеялом с целью избежать попадания искр на этот этаж отделения.
Все средства
пожаротушения, пожарное оборудование и инвентарь должны содержаться на
установленных местах в полной исправности и готовности к немедленному
использованию.
Не
допускается розлив жидких углеводородов и нефтепродуктов, а также утечка газов
через фланцевые соединения, сальники насосов и запорную арматуру.
В случае
возникновения пожара или аварии необходимо немедленно сообщить в пожарную
команду по телефону 01 или по извещателю и одновременно принять меры по
ликвидации аварии и тушению пожара имеющимися средствами пожаротушения: водой, песком,
паром, асбестовыми одеялами, огнетушителями.
При тушении
электрооборудования можно применять воду и пар; пенный огнетушитель разрешается
использовать только после снятия напряжения.
Заключение
Производство этилового спирта в нашей стране играет
важную роль в народном хозяйстве.
Гидратация этилена - наиболее эффективный способ
производства этилового спирта, позволяющий экономить по сравнению с его
получением из пищевого сырья на 1т этилового спирта около 4 т зерна или до 12 т
картофеля.
На получение 1 т этилового спирта из пищевого сырья
затрачивается от 160 чел.-час (из зерна) до 280 чел.-час. (из картофеля), из
нефтехимического сырья - 10 чел.-час.; значительно меньше капитальных затрат
потребуется на строительство заводов синтетического этилового спирта по
сравнению с заводами пищевого этилового спирта.
Метод получения этилового спирта сернокислотной
гидратацией этилена в настоящее время несколько устарел, кроме того он является
небезопасным. Опасность данного метода обуславливается прежде всего
использованием концентрированной серной кислоты и жёсткими технологическими
параметрами процесса. Использование того или иного способа производства во
многом обуславливается качеством сырья, а именно – содержанием этилена в исходной
фракции.
Прямая гидратация этилена имеет ряд преимуществ перед
сернокислотным методом: исключение расхода серной кислоты и минимальные
потребности в других реагентах, кроме этилена и водяного пара. Кроме того,
процесс прямой гидратации этилена протекает в одну стадию, что обуславливает
более высокий выход спирта.
Этиловый спирт применяется в пищевой, химической
промышленности, в парфюмерии и медицине, поэтому необходимо следить за
соответствием получаемого спирта ГОСТам нашей страны. Сейчас в России довольно
сложная ситуация с потреблением алкоголя населением. Нашей пищевой
промышленности нужен контроль за качеством спирта, за подпольным производством
и незаконной продажей спиртных напитков. Таким образом, возможно, уменьшить
смертность населения, и употребление алкоголя станет более безопасным.
Список использованных источников
1. Валакин В.П. Получение синтетического этилового
спирта. М., Химия, 1976.
2. Лебедев Н.Н. Химия и технология
основного органического и нефтехимического синтеза. Изд. 3-е, перераб. М.,
Химия, 1981 г.
3. Справочник. Расчёты химико-технологических
процессов. Под общей редакцией проф. И. П. Мухлёнова. Л., «Химия», 1976 г.
4. Справочник. Краткий справочник
физико-химических величин. Изд. 8-е, пер./Под ред. А.А. Равделя и А.М. Пономарёвой.
Л., Химия, 1983 г. 232с.
5. Юкельсон И.Ю.Технология основного
органического синтеза. М.,Химия, 1968 г.
6. Паушкин
Я.М. Нефтихимический
синтез в промышленности. М.,Наука,1966 г.
7. Авторские
свидетельства: №307997, №577201, №847911,
№249358, №368216, №608796, №.2337967.
Приложения
.
Рис. 1. Схема отделения прямой гидратации этилена:
1 - буфер; 2 - компрессор свежего этилена; 3 - компрессор
циркулирующего газа; 4 - паровой подогреватель; 5, 10, 14 -
теплообменники; 6, 15 - холодильники; 7,8 - котлы-утилизаторы, 9
- реактор; 11 - сепаратор; 12(1), 12(11) - газоотделители; 13
- скруббер; 16, 20 - ёмкости; 17, 18, 21 - насосы; 19 -
сборник; ФВ - фузельная вода
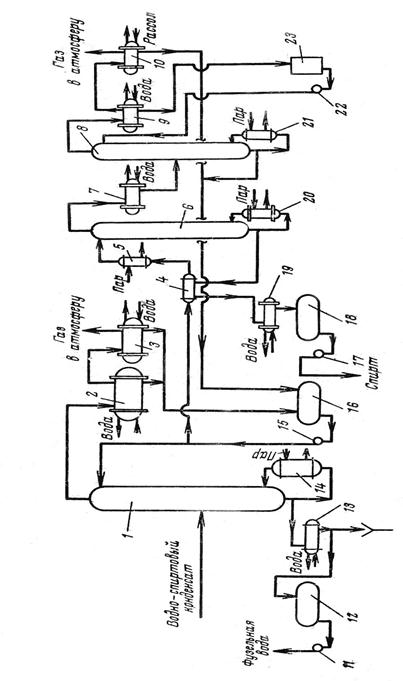
Рис.2. Схема отделения ректификации водно-спиртового
конденсата:
1, 6, 8 – ректификационные колонны; 2, 3, 7, 9, 10 –
конденсаторы-дефлегматоры; 4 – теплообменник; 5 – паровой
подогреватель; 11, 15, 17, 22 – насосы; 12, 16, 18 – ёмкости; 14,
20, 21 – кипятильники; 23 – сборник.
Рис. 3. Схема катализаторного отделения:
1 – воздуходувка; 2 – осушитель; 3
– паровой подогреватель; 4 – пропарочный аппарат; 5, 9 –
полигональные сита; 6 – прокалочная печь; 7 – топка; 8, 13 –
вентиляторы; 10 – пропиточная ванна; 11 – сушилка; 12 –
бункер; 14 – отстойник; 15, 16 – сборники; 17 – смеситель;
18 – насос; 19, 20 – ёмкости; 21 – щелочной гидролизатор; 22
– вакуум-насос; 23 – калорифер; 24 – сито «Ротекс».
Рис. 4.
Реактор: Рис. 5. Скруббер:
Рис. 6. Ректификационная колонна;
1 – крышка; 2, 3, 5, 6, 9 – штуцеры для термопар; 4 – люки; 7
– корпус; 8, 10 – штуцеры для замера уровня в кубе; 11 – днище; 12
– прорези; 13 – отверстия для слива жидкости; 14 – отверстия
для прохода паров.
|