Реферат: Индукционная плавка металла
Реферат: Индукционная плавка металла
Федеральное
агентство по образованию
Южно-Уральский
государственный университет
Кафедра общей
и теоретической физики
Реферат
на тему:
«Индукционная
плавка металла»
Выполнил: студент
гр.ФМ-223
Плотников С.А.
Проверил: доцент кафедры
О.Т.Ф.
Герасимов В.К.
Челябинск
2008
Содержание
Содержание2
Введение3
Явление электромагнитной индукции3
Опыты Фарадея3
Применение в Металлургии4
Выплавка стали в индукционных печах4
Индукционные печи промышленной частоты12
Плавка в печи с кислой футеровкой.13
Плавка в вакуумных индукционных печах.13
Заключение16
Используемая литература:17
Введение
Явление
электромагнитной индукции
Электрические токи создают вокруг себя магнитное поле. Связь
магнитного поля с током привела к многочисленным попыткам возбудить ток в
контуре с помощью магнитного поля. Эта фундаментальная задача была блестяще
решена в 1831 г. английским физиком М. Фарадеем, открывшим явление
электромагнитной индукции. Оно заключается в том, что в замкнутом проводящем
контуре при изменении потока магнитной индукции, охватываемого этим контуром,
возникает электрический ток, получивший название индукционного.
Опыты
Фарадея
Рассмотрим классические опыты Фарадея, с помощью которых было
обнаружено явление электромагнитной индукции.
Опыт I. Если в замкнутый на гальванометр соленоид вдвигать
или выдвигать постоянный магнит, то в моменты его вдвигания или выдвигания
наблюдается отклонение прели гальванометре (возникает индукционный ток);
направления отклонений стрелки при выдвигании и выдвигании магнита
противоположны. Отклонение стрелки гальванометра тем больше, чем больше
скорость движения магнита относительно катушки. При изменении полюсов магнита
направление отклонения стрелки изменится. Для получения индукционного тока
магнит можно оставлять неподвижным, тогда нужно относительно магнита
передвигать соленоид.
Опыт ll. Концы одной из катушек, вставленных одна в
другую, присоединяются к гальванометру, а через другую катушку пропускается
ток. Отклонение стрелки гальванометра наблюдается в моменты включения или
выключения тока, в моменты его увеличения или уменьшены или при перемещении
катушек друг относительно друга. Направления отклонившейся стрелки
гальванометра также противоположны при включении или выключении тока, его
увеличении или уменьшении, сближении или удалении катушек.
Обобщая результаты своих многочисленных опытов, Фарадей пришел к
выводу, что индукционный ток возникает всегда, когда происходит изменение
сцепленного с контуром потока магнитной индукции. Например, при повороте в
однородном магнитном поле замкнутого проводящего контура в нем также возникает
индукционный ток. В данном случае индукция магнитного поля вблизи проводника остается постоянной, а
меняется только поток магнитной индукции сквозь контур.
Опытным путем было также установлено, что значение индукционного
тока совершенно не зависит от способа изменения потока магнитной индукции, а
определяете лишь скоростью его изменения (в опытах Фарадея также
доказывается, что отклонение стрелки гальванометра (сила тока) тем больше, чем
больше скорость движения магнита, или скорость изменения силы тока, или
скорость движения катушек).
Применение
в Металлургии
Выплавка стали в
индукционных печах
В индукционной
бессердечниковой печи металл расплавляют в тигле, расположенном внутри
индуктора, который представляет собой спираль с несколькими витками из токопроводящего
материала.
Через индуктор пропускают переменный ток; создаваемый при
этом внутри индуктора переменный магнитный поток (рис. 1) наводит в металле вихревые
токи, которые обеспечивают его нагрев и плавление.
Рис.1
Магнитные силовые линии в индукционной печи 1
|
Чтобы чрезмерно не увеличивать мощность питающего печь генератора
в схему печи включают конденсаторы, компенсирующие индуктивное сопротивление
индуктора. Как известно, наличие индуктивного сопротивления в цепи переменного
тока вызывает сдвиг фаз (величина силы тока отстает от величины напряжения), в
результате чего снижается коэффициент мощности установки соs(ф). Емкость вызывает
обратный сдвиг фаз; подбирая емкость конденсаторов, добиваются настройки
установки в резонанс, когда угол сдвига фаз ф приближается к нулю, а соs ф к единице, Чем выше
частота, тем меньше требуется емкость конденсаторной батареи.
Важной
особенностью индукционных печей является интенсивная циркуляция жидкого
металла, вызываемая взаимодействием электромагнитных полей, возбуждаемых с
одной стороны токами проходящими по индуктору и, с другой, вихревыми токами в
металле.
Характер
циркуляционных потоков показан на рис. 2. Положительная сторона этого явления
состоит в том, что благодаря перемешиванию ускоряются плавление и выравнивание
состава и температуры металла, отрицательная — в том, что поверхность металла;
получается выпуклой и может оголяться, так как шлак стекает к стенкам тигля.
Интенсивность перемешивания приблизительно пропорциональна квадрату ампервитков
(1п)- и обратно пропорциональна частоте питающего тока.
Рис. 2. 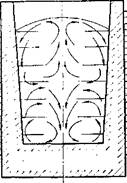
Электродинамическая
циркуляция
металла в тигле
индукционной печи.
Еще одной особенностью индукционных печей является то, что плотность
индуктируемых токов достигает максимума на поверхности металла у стенок тигля и
снижается по направлению к оси тигля («поверхностный эффект»). В этом
поверхностном слое выделяется наибольшее количество тепла, за счет которого
плавится шихта. Толщина слоя металла с большой плотностью индуктируемых токов
обратно пропорциональна корню квадратному из частоты.
Индукционные печи имеют следующие преимущества по сравнению с
дуговыми:
1) отсутствуют высокотемпературные дуги, что уменьшает поглощение водорода
и азота и угар металла при плавлении;
2)незначительный угар легирующих элементов при переплаве легированных
отходов;
3) малые габариты печей, позволяющие поместить их в закрытые камеры
и вести плавку в вакууме или в атмосфере инертного газа;
4) электродинамическое перемешивание, способствующее получению
однородного по составу и температуре металла. Основными недостатками
индукционных печей являются малая стойкость основной футеровки и низкая
температура шлаков, которые нагреваются от металла; из-за холодных шлаков
затруднено удаление фосфора и серы при плавке.
Индукционные печи делят на два типа:
1) питаемые током повышенной частоты;
2) питаемые током промышленной частоты (50 Гц).
В печах первого типа частота питающего тока обычно снижается; По
мере роста емкости и диаметра тигля; малые (несколько килограмм и менее) печи
питаются током с частотой от 50 до 1000 кГц, средние и крупные (емкостью
до десятков тонн) токами с частотой |0,5—10 кГц.
1 Устройство
индукционной печи.
Индукционная
плавильная установка состоит из печи с механизмом наклона и питающего
электрооборудования (генератора повышенной частоты, батареи конденсаторов, щита
управления и на крупных печах — автоматического регулятора электрического
режима). Емкость индукционных печей достигает 60 т. Основные элементы печи
— каркас, индуктор и огнеупорный тигель, который иногда закрывают крышкой.
Рис.3.
Индукционная печь
емкостью 60 кг.
1-каркас,
2-подовая плита,
3-индуктор,
4-изоляционный слой,
5-тигель,
6-абсоцемеитная плита,
7-сливной носок,
8-воротник,
9-гибкий токопровод,
10-деревянные брусья.
Каркас
(кожух) печей небольшой емкости (<0,5 т) делают в форме прямоугольного
параллелепипеда, используя асбоцемент, дерево, выполняя несущие ребра из
уголков и полос немагнитной стали, дюралюминия. В местах соединения
металлических элементов укладывают изоляционные прокладки для исключения
возникновения кольцевых токов, Индуктор в таком каркасе крепят к верхней и
нижней опорным асбоцементным плитам (рис. 3). В печах средней и большой емкости
каркас выполняют из стали в виде сплошного кожуха цилиндрической формы (рис. 4)
и иногда в виде «беличьей клетки», представляющей собой группу вертикальных
стоек, приваренных к верхнему и нижнему опорным кольцам. Для уменьшения нагрева
таких каркасов индуктируемыми токами и потерь с потоками рассеивания используют
следующие решения:
а) каркас
выполняют из немагнитной стали;
б) между
каркасом из обычной стали и индуктором размещают магнитопровод из нескольких
пакетов трансформаторной стали, располагаемых вдоль индуктора (рис. 4);
в) между индуктором
и каркасом размещают замкнутый электромагнитный экран из металла с низким
удельным сопротивлением (меди, алюминия).
В каркасе
жестко крепят индуктор, подовую плиту, верхнюю керамику, пакеты магнитопровода.
К передней части каркаса на уровне сливного носка прикрепляют две цапфы, что
необходимо для поворота печи при сливе металла.
Рис.4 Индукционная печь
емкостью 8 т.
1-индуктор,
2-тигель,
3-подовая плита,
4-съемный свод,
5-сливной носок,
6-стальной кожух,
7-ось поворота,
8-магнитопровод из
трансформаторной стали.
Индуктор
имеет форму полого цилиндра и образован уложенными в виде спирали витками из
медной трубки. Профили применяемых медных трубок показаны на рис. 5, а; равностенные
трубки используют обычно для печей повышенной частоты, а разностенные — для
печей промышленной частоты. Для исключения электрического пробоя витки, как
правило, изолируют (на малых печах с небольшим напряжением достаточна воздушная
изоляция, достигаемая зазором между витками в 10—20 мм). Широко применяют
следующие виды изоляции: обмоточную, когда витки покрывают изоляционным лаком и
затем обматывают лентой из диэлектрического материала (стеклоленты, микаленты);
прокладочную, когда между покрытыми лаком витками закрепляют диэлектрические
прокладки (например, из стеклотекстолита); напыленную, когда на поверхность
трубки газопламенным или плазменным способом наносят слой окиси алюминия или
двуокиси циркония с последующим покрытием лаком.
Иногда применяют монолитную изоляцию — покрытые лаком витки
заливают полимерным материалом (полиэфирным компаундом), после застывания
которого образуется монолитная конструкция. Прочность и жесткость индуктора,
являющегося опорой футеровки тигля, обеспечивают, применяя индукторы двух следующих
разновидностей: с креплением витков шпильками и стяжные индукторы. Во-первых,
к виткам индуктора приваривают латунные
шпильки; с помощью шпилек и латунных гаек
витки крепят к нескольким вертикальным стойкам (рис.5б), из изоляционного
материала текстолита, асбоцемента ,дерева; стойки в свою очередь крепят к
опорным плитам каркаса, расположенным над индуктором и под ним. В стяжных
индукторах над верхним и под нижним витками размещают нажимные фланцы, которые
стягивают в осевом направлении с помощью специальных болтов и вертикальных
реек из изоляционного материала (см. рис. 5, в); вертикальные рейки препятствуют
смещению витков в поперечном направлении. Для придания жесткости индуктору и
его крепления в каркасе дополнительно используют пакеты магнитопровода, которые
прижимают к индуктору через изолирующие прокладки с помощью специальных
нажимных болтов.
Если индуктор выполнен монолитным, то в нем не требуется
дополнительного крепления витков, однако такие индукторы применяют редко из-за
сложности ремонта трубки в случае ее повреждения,
Высоту индуктора выбирают в пределах 1,1 —1,2 высоты расплава в
тигле, внутренний диаметр определяют из соотношения:D=DT+2b (ф) +2b (и), где Dt и b (ф) — соответственно
внутренний диаметр и толщина футеровки в середине тигля; b (и) — толщина изоляционного
слоя (<5—6мм). Число витков индуктора определяют расчетом; плотность токов в
индукторе достигает 20—40 А/мм2. Подвод тока к индуктору чаще всего
осуществляют с помощью гибких кабелей.
По внутренней полости медной трубки пропускают охлаждающую воду.
Для обеспечения равномерного охлаждения на средних и больших печах индуктор
делят на 2—4 секции с самостоятельным подводом воды. Поступление воды
контролируется реле, отключающем питание печи при перерыве в подаче воды.
Футеровка индукционной печи состоит из следующих основных
элементов: футеровки тигля, подовой плиты (подины), верхней керамики
(воротника) со сливным носком. Подовая плита служит основанием для футеровки
тигля и для индуктора; на средних и крупных печах ее выполняют из шамотных
блоков или кирпичей, иногда на крупных печах — из огнеупорного бетона. На малых
печах подовую плиту делают также из нескольких асбоцементных плит, уложенных
одна на другую (см. рис. 3).
Футеровку тигля, как правило, делают набивной, при плавке она
спекается в монолит; на больших печах тигель иногда выкладывают из кирпичей.
Воротник, т. е. футеровку выше верхнего витка индуктора, которая не может
спекаться за счет тепла жидкого металла, делают из фасонных кирпичей (шамота,
хромомагнезита) или из огнеупорных масс с повышенным количеством связующих.
Сливной носок представляет собой фасонное изделие из шамота.
Футеровка тигля должна обладать следующими свойствами: высокой
огнеупорностью и шлакоустойчивостью; высокой термостойкостью, так как при
загрузке шихты она сильно охлаждается; высокой механической прочностью, чтобы
выдерживать удары шихты при загрузке; минимальной толщиной, поскольку металл
должен находиться как можно ближе к индуктору, т. е. в зоне наибольшей
плотности индуктируемых токов.
Рис. 5.
Профили
трубок для изготовления
Индуктора(а)
и способы крепления
витков
индуктора (б, в):
1-
латунная шпилька .
2- гайка.
3- витки
индуктора
4-стойка
из изоляционного материала .
5-стяжной
болт .
6-вертикальная
рейка.
7-нажимной
фланец.
1 Футеровка может быть основной или кислой. Набивную кислую
футеровку изготовляют из дробленого кварцита (фракции размером менее 3,5 мм)
или кварцевого песка с добавкой в качестве связующего борной кислоты (1,5—4 %)
без увлажнения. Для основных тиглей применяют огнеупорные смеси разных
составов, наиболее часто магнезитовый порошок; в качестве связки используют
огнеупорную глину, жидкое стекло, плавиковый шпат, борную кислоту и др.
Применяют как увлажненные, так и сухие смеси. Перед набивкой тигля внутреннюю
поверхность индуктора покрывают тонким изолирующим слоем, например, нанося
специальную изоляционную обмазку с последующей обклейкой стеклолентой; иногда
дополнительно укладывают теплоизоляционный слой из асбеста. На дне индуктора
засыпают слой футеровочной массы, утрамбовывают ее и затем устанавливают на нее
железный шаблон, наружные размеры которого соответствуют внутренним размерам
тигля. В пространство между шаблоном и индуктором засыпают футеровочную смесь и
уплотняют ее трамбовками. Затем выполняют воротник из фасонных кирпичей или
специальных масс с повышенным количеством связующих.
После окончания набивки футеровку сушат и спекают. Для этого, не
вынимая шаблона, включают плавильную установку; тепло, выделяемое в шаблоне,
нагревает футеровку. В зависимости от емкости тигля спекание длится от 1 до 4 ч
для кислого тигля и от 2 до 10 ч для основного. Окончательное спекание с
расплавлением шаблона происходит во время первой плавки. Спекание можно
проводить, вставив в тигель соответствующих размеров кусок готового электрода.
Тигли емкостью до 300 кг иногда набивают увлажненной массой в специальной
разборной пресс-форме. После сушки на воздухе такой тигель устанавливают в
индуктор на подовую плиту, а пространство между индуктором и тиглем засыпают
мелким огнеупорным порошком.
Стойкость кислых тиглей составляет 20—250 плавок. Основная
футеровка обладает меньшей термостойкостью и стойкость основных 'тиглей
значительно ниже (от 10 до 100 плавок; меньшая величина — для печей большой
емкости). Средний внутренний диаметр тигля От и высоту
расплава h(p) определяют
исходя из заданной емкости печи (объема металла) с учетом того, что величина
отношения Н,,ЮТ должна составлять 1,6—2,0 для 100-кг печи и
снижаться при увеличении емкости (до 1,1—1,4 для 6-т печи). Толщину футеровки
(м) в середине тигля определяют по формуле: b(ф) ~ 0,08 Т(^1/4),
где Т — емкость печи, т. Примерные соотношения между размерами тиглей и
индукторов сталеплавильных печей приведены в табл. 1. Механизм наклона
предназначен для наклона печи при сливе металла. Металл из тигля сливают через
сливной носок, поворачивая установленный на двух цапфах каркас печи на угол До 95°.
Наклон печи осуществляют лебедками, тельферами, а на крупных печах
устанавливают гидравлический механизм наклона.
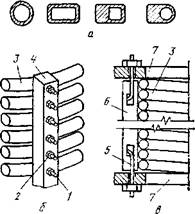
|

|
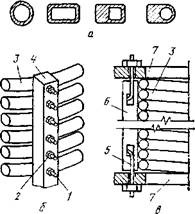
|
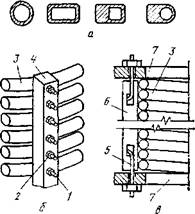
|
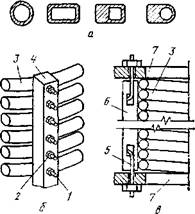
|
Таблица 1. Размеры индуктора и тигля индукционных печей
Рис. 6.
Упрощенная электрическая
схема индукционной печи.
Емкость, кг |
Размеры индуктора, |
Размеры тигля, мм |
высота |
Внутренний
диаметр |
глубина |
толщина дна |
сверху и снизу |
100 |
490 |
410 |
440 |
165 |
50 |
80 |
500 |
790 |
700 |
610 |
215 |
70 |
100 |
8000 |
1300 |
1380 |
1200 |
200 |
ПО |
150 |
1400 |
830 |
760 |
720 |
200 |
90 |
130 |
Электрическое оборудование -служит для подачи питания на индуктор
индукционной печи. Упрощенная электрическая схема индукционной печи повышенной
частоты, питаемой от машинного пли лампового генератора, показана на рис. 6.Переменный
ток высокой частоты от генератора через выключатель 2 подается на
индуктор 3, параллельно которому подключены конденсаторы 5 и 6.
Конденсаторы предназначены для компенсации индуктивного сопротивления
индуктора и установки в целом (компенсации реактивной мощности установки). В
цепь включены две группы конденсаторов: конденсаторы первой группы 6 подключены
постоянно; а конденсаторы второй группы 5 включают в случае
необходимости. В процессе плавки по мере нагрева шихты изменяется ее удельное
сопротивление и магнитная проницаемость, что изменяет индуктивное сопротивление
установки. Включая или отключая дополнительные конденсаторы добиваются
равенства индуктивного и емкостного сопротивлений, т.е. величины coos(ф) установки ,близкой к
единице. В качестве источников питания (преобразователей частоты) используют
ламповые и машинные генераторы, тиристорные преобразователи. Для питания малых
печей («30—50 кг) применяют ламповые генераторы, вырабатывающие ток с частотой
от 30 кГц до несколько мегагерц; их мощность изменяется от 0,3 до 1000 кВт.
Большая часть промышленных печей с тиглями емкостью 60—100 кг и более питаются
от машинных генераторов. Их выпускают мощностью от 12 до 2500 кВт с частотой
вырабатываемого тока 0,5; 1; 2,4; 4; 8 и 10 кГц. Соотношение между емкостью печи
и мощностью генератора примерно следующее:
Емкость, т 0,06 0,4 1,0 6 10
16 25
Мощность, кВт 50 250 500 2500 3000
5000 6000
В
последние годы в качестве источников питания все шире применяются тиристорные
преобразователи частоты. Промышленность выпускает тиристорные преобразователи
мощностью до 3200 кВт с частотой вырабатываемого тока от 0,5 до 10 кГц.
Эти преобразователи обладают по сравнению с машинными генераторами,
следующими преимуществами: более высокий электрический к. п. д.; высокая
готовность к работе; возможность автоматического поддержания оптимального
электрического режима без переключения в силовой цепи (не требуется
переключения конденсаторов, что упрощает конструкцию конденсаторной батареи);
отсутствие вращающихся частей и бесшумность в работе.
В состав электрооборудования индукционной печи входят также
подключаемые к силовой цепи через трансформаторы тока и напряжения
электроизмерительные приборы и приборы защиты (от перегрузок по току и
напряжению и в случае отключения охлаждающей воды). Крупные индукционные печи
снабжены автоматическим регулятором, который поддерживает оптимальный
электрический режим путем взаимосвязанного регулирования коэффициента мощности,
напряжения и силы тока. Основные параметры работы электрооборудования (мощность
генератора, емкость конденсаторов, требуемая частота тока и другие) определяют
расчетом исходя из заданных емкости печи, длительности плавления, температуры
жидкого металла.
Индукционные печи промышленной частоты
Футеровка и индуктор печей промышленной частоты такие же,
как у печей повышенной частоты. В схеме электропитания отсутствует генератор
тока повышенной частоты; печь включается в сеть через ступенчатый понижающий
трансформатор с вторичным напряжением от 100 до 1000 В. Ввиду отсутствия
преобразователя частоты для этих печей характерен меньший (на 5—10 %) удельный
расход электроэнергии и более высокий коэффициент мощности.
Однако при низкой частоте питающего тока (50 Гц) у этих печей
интенсивность электродинамического перемешивания металла значительно выше, чем
в печах повышенной частоты. Чтобы избежать чрезмерной циркуляции металла, печи
промышленной частоты рассчитывают на меньшую удельную мощность, чем печи
повышенной частоты; такой мощности недостаточно для быстрого расплавления
стальной шихты. Поэтому печи промышленной частоты обычно используют для плавки
металлов с более низкой температурой плавления (чугуна, цветных металлов).
Мощность печи емкостью 1 т составляет 360 кВ-А, емкостью 25 т — 4800 кВ-А.
Технология плавки
Плавку в индукционных печах обычно ведут без окисления примесей и
не ставят задачу удаления фосфора и серы, так как из-за
«холодных» шлаков дефосфорация и десульфурация затруднены.
Стали и сплавы выплавляют либо из легированных отходов (метод переплава),
либо из чистого шихтового железа и лома с добавкой ферросплавов (метод
сплавления).
Выбор установки. В печи с основной футеровкой можно выплавлять
сталь любого состава, но стойкость этой футеровки значительно ниже, чем кислой.
В печах с кислой футеровкой нельзя выплавлять стали с высоким содержанием
марганца, алюминия, титана, циркония, так как окислы марганца, взаимодействуя с
кремнеземом футеровки, быстро разрушают ее, а алюминий, титан и цирконий восстанавливают
кремний из кремнезема футеровки.
Плавка в печи с основной футеровкой. Продолжительность плавки
в индукционной печи очень небольшая, что не позволяет многократно проверить
состав металла путем его анализа. Поэтому получение стали с заданным составом
базируется на предварительном расчете шихты, для чего необходимы точное знание
ее состава и взвешивание. В частности, содержание углерода, серы и фосфора не
должно превышать допустимых в выплавляемой стали пределов.
Шихту составляют из мелких и крупных кусков, что обеспечивает
плотность ее укладки и сокращение длительности плавления. Наиболее крупные
куски укладывают у стенок тигля, где плотность токов максимальная. Тугоплавкие
ферросплавы загружают в нижнюю половину тигля.
После включения тока следят за тем, чтобы куски шихты не
сваривались в «мосты», препятствующие оседанию плавящихся кусков вниз.
Периодически шихту «осаживают» с помощью ломика. По мере оседания шихты
догружают ту ее часть, которая не вместилась при завалке. После появления
жидкого металла в тигель вводят шлакообразующую смесь из извести, плавикового шпата
и магнезита в соотношении 4:1:1. Назначение наводимого шлака — уменьшить
насыщение металла газами из атмосферы и окисление легирующих элементов. При
плавлении поддерживают максимальную мощность генератора и высокий соs(ф) путем подключения
конденсаторов. Длительность плавления изменяется от 30—40 мин на малых печах
(емкостью ~50 кг) до 2 ч на крупных.
После расплавления отбирают пробу металла на анализ и сливают
плавильный шлак, чтобы предотвратить восстановление из него фосфора, после чего
наводят новый шлак, добавляя шлакообразующую смесь того же состава, что и в
период плавления. Мощность, подаваемую на индуктор, снижают на 30—40 %. После
получения результатов анализа проводят легирование, корректировку состава
металла и его раскисление путем введения в тигель соответствующих ферросплавов,
после чего металл сливают из тигля в ковш. Иногда при выплавке высококачественных
сталей проводят диффузионное раскисление металла. Для этого в шлак вводят раскислительные
смеси, состоящие из извести, молотого ферросилиция, порошкообразного алюминия,
делая выдержку в течение примерно 30 мин; циркуляция металла в тигле
индукционной печи ускоряет раскисление.
Ферросплавы при плавке в индукционной печи присаживают в следующем
порядке: феррохром, ферровольфрам и ферромолибден вводят в завалку;
ферромарганец, ферросилиций и феррованадий — за 7—10 мин до выпуска; алюминий
перед выпуском. При таком
порядке введения угар элементов следующий: вольфрама
около 2 %,- хрома, марганца и ванадия — 5—10 %, кремния — 10—15 %, титана25—35
Плавка в печи с кислой футеровкой.
Содержание серы, фосфору и углерода не должно превышать допустимых
в выплавляемой стали пределов. При выплавке сталей легированных хромом,
вольфраме и молибденом в завалку вводят феррохром, ферровольфрам, ферромолибден.
Загрузку шихты и расплавление ведут так же, как и в с основной футеровкой. Шлак
во время плавления шихты, наводя; добавками боя стекла, шамота и извести
После расплавления и анализа отбираемой пробы металла проводят
легирование (корректировку состава) и раскисление. Ферромарганец, ферросилиций
и, если необходимо, феррованадий, вводят в металл на 7—10 мин до выпуска,
алюминий непосредственно перед выпуском. Угар марганца составляет 10 %, кремний
практически не угорает, угар вольфрама и молибдена около 2 %, хрома 5 %.
Расход электроэнергии при выплавке стали в индукционных составляет
500—700 кВт -ч/т.
Плавка в вакуумных индукционных печах.
Плавка в вакуумных индукционных печах позволяет получать сталь и
сплавы с малым содержанием газов, неметаллических включений и примесей цветных
металлов, легировать сплав любыми элементами, в том числе обладающими высоким
сродством к кислороду без их потерь на окисление .
Устройство печи. Первые печи были периодического действия. После
выпуска плавки вакуумную систему отключали и печь открывали для извлечения слитков
и загрузки шихтовых материалов. Позже были созданы более совершенные печи полунепрерывного
действия. Эти печи позволяют загружать шихту, устанавливать изложницы и
извлекать слитки без нарушения вакуума в плавильной камере. Емкость
существующих печей достигает 50 т.
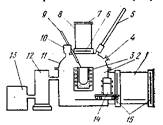
Рис. 7.
Схема
вакуумной индукционной
печи
полунепрерывного действия
На рис. 7 показана схема вакуумной индукционной печи полу;
непрерывного действия. Плавильная камера 2 имеет сверху съемную крышку.
В камере установлен индуктор с тиглем 3, закрепленный на цапфах; наклон
тигля для слива металла производят с помощью привода, расположенного с наружной
стороны камеры. В крышке плавильной камеры над тиглем размещена шлюзовая
загрузочная камера 8, отделяемая от плавильной вакуумным затвором 6 и
закрываемая крышкой 7, что позволяет загружать шихту без нарушения вакуума. В
загрузочную камеру ставят бадью с раскрывающимся дном, заполненную шихтой.
Закрыв крышку 7, в камере 8 создаю вакуум, после чего
открывают затвор 6 и шихта из бадьи высыпается в тигель.
Камера изложниц 1 отделена от плавильной камеры и от помещения
цеха задвижками 15. Через нее, как через шлюзовое устройство, в
плавильную камеру подают изложницы 14, установленные на тележке и после
слива в них металла из тигля возвращают обратно.
На крышке 11 смонтирован шлюзовой дозатор 10 для
введения добавок по ходу плавки и гляделка 4. Через крышку // с помощью
герметичных уплотнителей вводят термопару 5 и ломик 9 для осаживания
шихты.
Печь питается током повышенной частоты. Вакуумная система состоит
из группы форвакуумных 13 и бустерных 12 насосов, обеспечивающих
вакуум порядка 1,33—0,13 Па.
Процесс плавки в вакуумной индукционной печи.
Для плавки в вакуумных печах применяют шихтовые материалы,
очищенные от масла и окалины; состав их должен быть точно известен. В шихту вводят
никель, ферромолибден, ферровольфрам и кобальт, если этого требует состав
выплавляемой стали. После загрузки шихты включают ток, а на печах
периодического действия предварительно из печи откачивают воздух.
Плавление ведут, непрерывно откачивая насосами из плавильного
пространства выделяющиеся газы. За время плавления удаляется большая часть
вносимых шихтой газов — водород, часть азота, а также влага; жидкий металл при
плавлении кипит, что является результатом выделения пузырьков окиси углерода,
получающейся при взаимодействии углерода с растворенным в металле кислородом.
После расплавления делают выдержку в течение 20 — 40 мин, вовремя
которой происходит рафинирование от ряда примесей , раскисление и легирование
металла. В печи в этот период поддерживают давление
1,3 — 0,13 Па. Раскисление металла происходит углеродом по реакции
, равновесие которой в
условиях вакуума сдвинуто вправо, поскольку продукт реакции непрерывно удаляют
(откачивают). Преимуществом такого раскисления является то, что металл не
загрязняется его продуктами. Обычно выдержка длится до полного успокоения ванны
(т. е. до прекращения выделения СО). Раскисление идет либо за счет
содержащегося в металле углерода, либо за счет углерода, вводимого в начале
рафинирования в виде графита, чугуна.
Помимо рафинирования от кислорода в период выдержки удаляются азот
и водород и испаряются примеси цветных металлов (2п, 5п, РЬ, Аз, В). В период
выдержки проводят легирование и окончательное раскисление кусковыми
раскислителями, которые вводят через дозаторы. В начале выдержки вводят
феррохром, феррованадий, в конце выдержки ферросилиций, ферротитан, алюминий,
ферромарганец. Перед выпуском, если это потребуется, кальций, магний и РЗМ
Выплавленный металл разливают в изложницы, как правило, в
вакууме.
Иногда в процессе плавки ведут десульфурацию металла. С
этой целью на дно тигля до начала завалки шихты загружают десульфурирующую
шлакообразующую смесь (например, из 90 % СаО и 10 % СаF2).
Основные преимущества вакуумной индукционной плавки обусловлены
наличием вакуума, обеспечивающего рафинирование от ряда примесей и раскисление
углеродом, а также отсутствием контакта металла с окислительной атмосферой. Выплавляемые
при этом сталь и сплавы содержат пониженные количества азота, примесей цветных
металлов, кислорода и неметаллических включений, почти не содержат водорода;
все это повышает целый ряд служебных свойств сталей. Отсутствие контакта с
кислородом атмосферы позволяет выплавлять стали и сплавы, содержащие
легкоокисляющиеся элементы без их угара.
Недостатком вакуумных индукционных печей является то, что при
длительной выдержке в результате реагирования с окислами футеровки металл
загрязняется кислородом и неметаллическими включениями, а также
восстанавливаемыми из футеровки элементами (кремнием, алюминием и др.).
Заключение
Открытие явления электромагнитной индукции имело большое значение,
так и была доказана возможность получения электрического тока с помощью
магнитного поля. Этим была установлена взаимосвязь между электрическими и
магнитными явлениями, что послужило в дальнейшем толчком для разработки теории
электромагнитного поля.
Используемая
литература:
1.
Трофимова Т.И.
Курс Физики: Учебное пособие для вузов. стр.223-224.
2.
Паволоцкий
,Рощин В.Е. «Электрометаллургия и стали».
3.
Воскобойников В.Г.,
Кудрин В.А., Якушев А.М. «Общая металлургия» Учебник для вузов. Стр.482-496
|