Курсовая работа: Получение хлора методом электролиза повареной соли
Курсовая работа: Получение хлора методом электролиза повареной соли
Введение
Быстрое
развитие хлорной промышленности связано в основном с расширением производства
хлорорганических продуктов – винилхлоридов, хлорорганических растворителей,
инсектицидов и др. Хотя доля неорганиче6ских хлорпродуктов в общем потреблении
хлора сравнительно невелика, их значение для промышленности и народного
хозяйства трудно переоценить.
В России за
последние десятилетие создано и продолжает развиваться производства многих
неорганических хлорпродуктов.
Увеличивается
производство жидкого хлора, хлоридов алюминия, кремния, титана, железа, цинка и
хлоридов других металлов, применяемых в менее широких масштабах. Развивается
производства хлоридов натрия, магния и калия, вырабатываются в значительных
количествах хлораты кальция и перхлораты металлов и аммония.
Серьезные
технические и экономические проблемы возникают в связи со значительным
увеличением количества хлористого водорода, получающегося в качестве отходов в
ряде производств органических и неорганических хлорпродуктов. Заслуживает
большого внимания проблема рационального использования абгазного хлористого
водорода, в части получения из концентрированных и разбавленных растворов
соляной кислоты чистого 100%-го HCl для применения его в ряде процессов
органического синтеза и оксихлорирования.
Литературы
пот производству неорганических хлорпродуктов крайне мало. В последние годы
издано несколько инженерных монографий, посвященных производству хлора,
каустической соды и некоторых неорганических хлорпродуктов. Однако во многом
производства – хлористого водорода и соляной кислоты, хлоратов натрия, калия,
кальция, магния, перхлоратов и хлорной кислоты, водных растворов хлоридов
железа, алюминия и некоторых других продуктов – нет литературы, в которых были
бы систематизированы последние достижения в области их технологии. Кроме того, монография
по отдельным видам технологии производства хлора, каустической соды и
хлорпродуктов не могут заменить книгу, охватывающую весь комплекс этих
производств.
1 Свойства хлора, едких щелочей и водорода
1.1 Хлор
Хлор входит в
VII группу периодической
системы элементов, атомный вес 35,453, молярный вес 70.906, атомный номер 17.
При
нормальных условиях свободный хлор – зеленовато-желтый газ с характерным резким
и раздражающим запахом. Он сжигается при -34,05 °С, образуя прозрачную
жидкость янтарного цвета, затвердевающую при -101,6 °С и давлении 1 атм.
Ниже
приведены основные физико-химические и термодинамические свойства хлора:
Температура, °С
Плавления
Кипения (сжижения) при
1 атм
|
-101,6
-34,05
|
Критические константы
Температура, °С
Давление, атм
Плотность, г/см3
|
144
76,1
0,573
|
Удельный объем, см3/г
|
1,745 |
Плотность, г/л
Сухого газа при 0°Си 1
атм.
Насыщенного пара при 0 °С
и 3,617 атм.
Жидкого хлора при 0 °С
и 3,617 атм
|
3,209
12,08
1470,6
|
Удельный объем, м3/кг
Сухого газа при 0 °С
и 1 атм.
Насыщенного пара при 0 °С
и 3,617 атм.
Жидкого хлора при 0 °С
и 3,617 атм
|
0,3116
0,0828
0,00068
|
Давление паров при 0 °С,
атм. |
3,617 |
Вязкость при 20 °С,
сПа
Газа
Жидкого хлора
|
0,0140
0,35
|
Теплота, кал/г
Плавления твердого
хлора
Парообразования
|
22,9
67,4
|
Теплопроводность,
ккал/(м·ч·°С)
Газа при 0 °С
Газа при 55,5 °С
Жидкого хлора при 30 °С
|
0,0208
0,0242
0,533
|
Энтальпия, ккал/кг
Сухого газа
Насыщенного пара
Жидкого хлора
|
129,4
128,7
64,7
|
Энтропия, ккал/(кг·°С)
Сухого газа
Насыщенного пара
Жидкого хлора
|
0,329
0,312
0,208
|
Показатель преломления
при 14 °С |
1,367 |
При ведении
соли аммония в водный раствор хлора образуются треххлористый азот и . Треххлористый азот образуется при
взаимодействии аммиака или молей аммония с хлором или хлорноватистой кислотой:



При
взаимодействии хлористого аммония с хлорноватистой кислотой при рН=9,5
образуется монохлорамин, при рН=4,5 и температуре ниже 0 °С не образуется.
Чистый хлор,
получаемый электролизом водных растворов щелочных металлов, должен содержать не
менее 96% хлора и не более 2% и 1% . Содержание влаги после
осушки не должно превышать 0,04 вес.%.
В последнее
время требования к качеству газообразного хлора, применяемого в синтезе ряда
органических хлорпродуктов, сильно возросли. Содержание влаги в хлоргазе
ограничивается 40–100 мг/м3, снижается допустимое содержание брома,
соединений серы и других примесей.
1.2 Каустическая сода и едкие щелочи
Выпускаемые
марки улучшенного едкого натра, получаемого по методу электролиза с ртутным
катодом, должны удовлетворять приведенным ниже требованиям.
|
Марка I |
Марка II |
Содержание , % не менее
|
45 |
42 |
Содержание примесей, %
не более


Железо в пересчете на 



Хлораты в пересчете на 
Алюминий в пересчете на









|
0,3
0,02
0,001
0,02
0,0014
0,008
0,01
0,003
0,00003
0,0002
0,00005
0,0001
0,0001
0,0002
0,03
0,0001
|
0,6
0,05
0,001
0,02
0,0014
0,008
0,01
0,01
0,00005
0,00002
0,00005
0,0001
0,0001
0,0002
0,1
0,0001
|
Коэффициент
светопропускания, %, не ниже |
90 |
80 |
Выпускаются
также реактивные и особо чистые едкий натр и едкое кали.
1.3 Водород
Основные
физико-химические свойства водорода приведены ниже.
Молекулярный вес |
2,016 |
Мольный объем при 0 °С
и 760 мм. рт. ст, л |
22,43 |
Температура, °С
Кипения
Плавления
|
-252,8
-259,4
|
Критические константы
Температура, °С
Давление, атм
Плотность, г/см3
|
-239,9
12,8
0,031
|
Плотность
При 0 °С и 760 мм
рт. ст., кг/м3
При температуре
кипения, кг/л
Относительная (по
воздуху)
|
0,0899
0,0709
0,0695
|
Удельная газовая
постоянная, ккал/(кг·°С) |
986,96 |
Теплота, ккал/кг
Плавления
Парообразования при 760 мм
рт. ст.
|
14,0
108,5
|
Объем жидкости,
образующейся из 1 м3 газа при 15 °С и 760 мм рт. ст.,
л
|
1,166 |
Удельная теплоемкость
при 20 °С и 760 мм рт. ст., ккал/(кг·°С)



|
3,408
2,42
1,407
|
Вязкость при 0 °С
и 760 мм рт. ст., сП |
0,0085 |
Теплопроводность при 0 °С
и 760 мм рт. ст., ккал/(м·ч·°С) |
0,140 |
2. Источники сырья для электрохимического получения хлора,
едкого натра и водорода
Сырьем для электролиза служит хлорид натрия в виде каменной соли,
самоосадочной соли или подземного рассола. Подготовка сырья к электролизу
включает операции растворения (при использовании твердой соли), очистки рассола
от механических примесей и удаления ионов кальция и магния.
Механические примеси удаляют отстаиванием рассола с последующим
фильтрованием осадка, а ионы кальция и магния, которые отрицательно влияют на
процесс электролиза, обработкой рассола раствором карбоната натрия или
известковым молоком:
СаСl +Na2CO3 → СаСО3+
2NaCl
с последующей нейтрализацией избыточной щелочности соляной
кислотой. Осадок карбонатов кальция и магния удаляют фильтрованием.
Полученный рассол должен иметь концентрацию соли 310–315 г./л,
чтобы обеспечить, возможно, более низкий потенциал разряда ионов при
электролизе. Также существуют допустимые пределы содержания ионов кальция и
магния.
Рассол, поступающий на электролиз, представляет многокомпонентную
систему, в которой содержатся ионы натрия, хлора, гидроксоний-катион и
гидроксид-анион. Последовательность их разряда и образующиеся продукты
определяются в соответствии с «правилом разряда» величиной их потенциалов
разряда, которые зависят от условий электролиза и, весьма существенно, от
материала катода. Различают два варианта технологического процесса электролиза
водного раствора хлорида натрия: электролиз с твердым железным катодом
(диафрагменный метод) и электролиз с жидким ртутным катодом.
Аноды электролизеров в обоих случаях изготавливают из одинаковых
материалов: искусственного графита, пропитанного для уменьшения износа льняным
маслом, или из титана, покрытого слоем оксидов рутения и титана. Аноды второго
типа позволяют вести электролиз при высоких плотностях тока и более низком
напряжении. Такие условия снижают расход электроэнергии на 10–12%. Поэтому
оксидно-рутениевые аноды вытесняют графитовые: ими оснащено в настоящее время
до 70% всех установок электролиза.
3. Современные промышленные способы получения хлора и едкого
натра
Технический
электролиз водных растворов может осуществляться без выделения металлов или с
их выделением на катоде. Среди электрохимических процессов разложения водных
растворов без выделения металлов наибольшее распространение получил электролиз
водных растворов хлорида натрия.
Электролиз
водных растворов хлорида натрия. При электролизе водных растворов
хлорида натрия получают хлор, водород и едкий натр (каустическая сода).
Хлор
– при атмосферном давлении и обычной температуре газ желто-зеленого цвета с
удушливым запахом. при атмосферном давлении температура кипения хлора –33,6° С,
температура замерзания -102° С. Хлор растворяется в воде, органических
растворителях и обладает высокой химической активностью.
Хлор
потребляется прежде всего химической промышленностью для производства различных
органических хлорпроизводных, идущих для получения пластических масс,
синтетических каучуков, химических волокон, растворителей, инсектицидов и т.п.
В настоящее время более 60% мирового производства хлора используется для
органического синтеза. Помимо этого хлор используют для производства соляной
кислоты, хлорной извести, хлоратов и других продуктов. Значительные количества
хлора идут в металлургию для хлорирования при переработке полиметаллических
руд, извлечения золота из руд, а также его используют в нефтеперерабатывающей
промышленности, в сельском хозяйстве, в медицине и санитарии, для
обезвреживания питьевой и сточных вод, в пиротехнике и ряде других областей
народного хозяйства. В результате развития сфер использования хлора, главным
образом благодаря успехам органического синтеза, мировое производство хлора
составляет более 20 млн. т/год.
Едкий
натр, или каустическая сода, – кристаллическое непрозрачное вещество, хорошо
растворимое в воде, имеющее при атмосферном давлении температуру плавления 328°
С. В промышленности выпускается твердый едкий натр и его водные растворы. Едкий
натр широко используется во многих отраслях промышленности –
целлюлозно-бумажной, химических волокон, нефтеперерабатывающей, органического
синтеза, мыловаренной, лакокрасочной и в ряде других.
Водород
– газ, температура кипения которого при атмосферном давлении –252,8 °С. Водород
используют для синтеза важнейших неорганических и органических продуктов:
аммиака, метанола и других спиртов, для гидрогенизации жиров, твердых и жидких
топлив, очистки нефтепродуктов и др.
Сырьем
для производства хлора и щелочи служат, главным образом, растворы поваренной
соли, получаемые растворением твердой соли, или же природные рассолы. Растворы
поваренной соли независимо от пути их получения содержат примеси солей кальция
и магния и до того, как они передаются в цеха электролиза, подвергаются очистке
от этих солей. Очистка необходима потому, что в процессе электролиза могут
образовываться плохо растворимые гидроокиси кальция и магния, которые нарушают
нормальный ход электролиза. Очистка рассолов производится раствором соды и
известковым молоком. Помимо химической очистки, растворы освобождаются от
механических примесей отстаиванием и фильтрацией. Электролиз растворов
поваренной соли производится в ваннах с твердым железным (стальным) катодом и с
диафрагмами и в ваннах с жидким ртутным катодом. Промышленные электролизеры,
применяемые для оборудования современных крупных хлорных цехов, должны иметь
высокую производительность, простую конструкцию, быть компактными, работать
надежно и устойчиво.
Электролиз
растворов хлорида натрия в ваннах со стальным катодом и графитовым анодом
позволяет получать едкий натр, хлор и водород в одном электролизере. При
прохождении постоянного электрического тока через водный раствор хлорида натрия
можно ожидать выделения хлора, а также кислорода:
2OH-
– 2ē→1/2О2+Н2О
или
2Cl-
– 2ē→Cl2
Нормальный
электродный потенциал разряда OH – – ионов составляет +0,41 В, а
нормальный электродный потенциал разряда ионов хлора равен +1,36 В. В
нейтральном насыщенном растворе хлорида натрия концентрация гидроксильных ионов
около 1·10-7 г-экв/л. При 25° С равновесный потенциал разряда
гидроксильных ионов будет φар=0,82 В. Равновесный
потенциал разряда ионов хлора при концентрации NaCl в растворе 4,6 г-экв/л
равен φар=1,32 В. Следовательно, на аноде с малым
перенапряжением должен в первую очередь разряжаться кислород. Однако на
графитовых анодах перенапряжение кислорода много выше перенапряжения хлора и
поэтому на них будет происходить в основном разряд ионов Cl- с
выделением газообразного хлора по реакции (а). Выделение хлора облегчается при
увеличении концентрации NaCl в растворе в следствии уменьшения при этом
равновесного потенциала. Это является одной из причин использования при
электролизе концентрированных растворов хлорида натрия, содержащих 310–315 г./л.
На катоде в щелочном растворе происходит разряд молекул воды по уравнению
H2O
+ ē→H + OH-
Атомы
водорода после рекомбинации выделяются в виде молекулярного водорода:
2H→H2
Разряд
ионов натрия из водных растворов на твердом катоде невозможен в следствии более
высокого потенциала их разряда по сравнению с водородом. Поэтому остающиеся в
растворе гидроксильные ионы образуют с ионами натрия раствор щелочи. Процесс
разложения NaCl можно выразить следующими реакциями:
2Cl-
– 2ē→Cl2
Н2О
+ ē=2Н + ОН-
2H→H2
Просуммировав
уравнения получим:
2Н2О
+ 2Cl-→ Cl2 + H2 + 2ОН-
или
2Н2О
+ 2NaCl→ Cl2 + H2 + 2NaOH
То
есть на аноде идет образование хлора, а у катода – водорода и едкого натра. При
электролизе наряду с основными описанными процессами могут протекать и
побочные, один из которых описывается уравнением (б). Помимо этого, хлор,
выделяющийся на аноде, частично растворяется в электролите и гидролизуется по
реакции
Cl2
+ Н2О↔НОCl + НCl
В
случае диффузии щелочи (ионов ОН-) к аноду или смешения катодных и
анодных продуктов хлорноватистая и соляная кислоты нейтрализуются щелочью с
образованием гипохлорита и хлорида натрия:
НОC
+ NaOH=NaOC + Н2О
HCl
+ NaOH=NaCl + Н2О
Ионы
ClO – на аноде легко окисляются в ClO3- Следовательно,
из-за побочных процессов при электролизе будут образовываться гипохлорит,
хлорид и хлорат натрия, что снижает выход по току и коэффициент использования
энергии. В щелочной среде облегчается выделение кислорода на аноде, что также
будет ухудшать показатели электролиза. Чтобы уменьшить протекание побочных
реакций, следует создать условия, препятствующие смешению катодных и анодных
продуктов. К ним относятся разделение катодного и анодного пространств
диафрагмой и фильтрация электролита через диафрагму в направлении,
противоположном движению ОН – – ионов к аноду. Такие диафрагмы
называются фильтрующими диафрагмами и выполняются из асбеста.
4. Описание электролизера с твердым катодом
Электролизеры
БГК-17 рассчитаны на номинальную нагрузку 25 кА. Она выпускается для работы при
750 и 900 А/м3, но могут работать и при более высокой плотности
тока. Электролизеры этого типа предназначены в основном для цехов электролиза
мощностью 25–100 тыс. т хлора в год.
В
электролизерах типа БГК-17 применена конструкция разветвленного катода,
состоящего из узких плоских катодных пальцев, выполненных из стальной сетки и
расположенных в виде четырех или шести гребенок. Катоды электролизеров имеют
стальной каркас, что обеспечивает ток по поверхности катода. При правильном
соотношении объемов катодного и анодного пространства в этих электролизерах
можно значительно увеличить рабочую высоту электродов без опасения снизить
выход по току.
Конструкция
катодного блока предусматривает повышенное газонаполнение в катодном
пространстве и исключает возможность снижения давления фильтрации через
диафрагму в нижней части. В электролизерах применен нижний подвод тока к
анодам. Верхняя часть анодного пространства свободна от анодов и моет быть
достаточно развита в высоту.
Электролизеры
БГК-17 отличаются большой высотой, что обеспечивает компактность конструкции и
высокие съемы продукции с единицы площади производственного здания при
сравнительно невысокой плотности тока, пониженные удельные расход
электроэнергии и затраты цветных металлов по сравнению с электролизерами других
типов. Достигнута хорошая герметичность в местах соединений катодного блока с
анодным комплексом и крышкой.
Схема
устройства электролизера БГК-17 на нагрузку 25 кА показана на рис. 1.
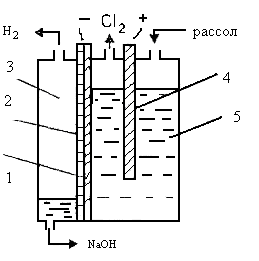
1 – перфорированный катод, 2 – диафрагма, 3 – катодное
пространство, 4 – анод, 5 – анодное пространство.
Рис. 1. – Электролизер вертикального типа
Катодный блок
представляет собой стальной корпус, внутри которого в четыре ряда вмонтированы
гребенки катодных пальцев представляющих собой сплющенные полые карманы,
выполненные из металлических каркасов с натянутой на них стальной проволочной
сеткой. Толщина катодных пальцев 20 мм. Крайние каркасы катодных гребенок
приварены к продольным стенкам корпуса катода, два средних образуют двухстороннюю
гребенку, приваренную к торцевым стенкам корпуса.
Внутреннее
пространство катодных элементов в электролизере сообщается между собой, образуя
общее катодное пространство, заполненное католитом, а в верхней части –
водородом. Между двумя соседними катодными гребенками сохраняется
циркуляционное пространство, свободное от электродов.
На сетчатую
поверхность катода насасывается асбестовая диаграмма. В корпусе катода
предусмотрен штуцер для присоединения к вакуумной линии при насасывании
диафрагмы.
Анодный блок
состоит из графитовых плит толщиной 50 мм и шириной 250 мм,
монтируемых на стальном анодном днище, которое одновременно используется для
подвода тока к анодным плитам с помощью специальных контактных устройств (без
применения свинца).
Днище
электролизера вместе с контактной частью анода для защиты от действия
хлорсодержащего анолита заливают битумной массой специального состава, поверх
которой наносят тонкий слой бетона. Битумная масса имеет температуру плавлении,
удобную для ее нанесения и удаления. При комнатной температуре масса достаточно
хрупка и легко удаляется пневматическим инструментом. Во время работы
электролизера масса размягчается и заполняет все пустоты, поры и возможные
трещины. При этом повышается ее адгезия к графиту и металлу и увеличивается
надежность защиты анодного контакта.
Ток к
анодного днищу подводится с помощью контактных пластин, приваренных к днищу
электролизера, а ток к катоду – через пластины, приваренные к катодному
корпусу.
При установке
катодного блока на анодный комплект графитовые плиты располагаются в
промежутках между пальцами катодных гребенок. При новых анодах расстояние между
электродами составляет около 12 м. щелочь из катодного пространства
сливается по нижнему штуцеру, соединенному сифонной трубой с капельницей.
Уровень жидкости в катодном пространстве можно регулировать, меняя положение
подвижной трубы для слива щелочи. Водород отводится из электролизера по верхнему
штуцеру катодного блока.
Стенки корпуса
катода подняты несколько выше катодных карманов и образуют надкатодную камеру и
раструб для устранения крышки. Для защиты от действия хлора внутренние стенки
раструба покрывают слоем бетона.
Бетонная крышка
электролизера типа БГК-17 изготавливается в металлических формах. Для
предотвращения от разрушения при действии кислого анолита и влажного хлора
крышку выполняют из кислотобетона, стойкого в условиях работы электролизера.
При использовании таких крышек исключается загрязнение анолита солями кальция и
магния, как это происходит в результате коррозионного разрушения крышки в
случае применения обычного бетона на портланд-цементе.
Крышка
электролизера снабжена отверстиями для отвода хлора, подачи свежего рассола,
установки термометра, измерителя уровня рассола и отбора проб анолита. После установки
в раструбе катода крышка уплотняется специальной замазкой.
В последнее
время в электролизерах БГК-17 с успехом стали применяться стальные
гуммированные крышки, что облегчает конструкцию электролизеров, их монтаж и
обслуживание.
Уплотнение
между анодным комплектом и катодным блоком достигается за счет собственной
тяжести катода с крышкой и с помощью дополнительной болтовой стяжки. Особая
конструкция уплотнительного устройства в электролизере позволяет легко и
надежно герметизировать стык между анодной и катодной частями электролизера и
обеспечивает точность расположения анодов между катодными пальцами при сборке.
Устройство для уплотнения исключает возможность течи электролита, что позволяет
поддерживать чистоту и опрятный вид серии электролизеров во время их работы.
При примени
сдвоенного сварного катода достигается максимальное развитие активной катодной
поверхности и интенсивная естественная циркуляция электролита. Графитовые аноды
с трех сторон окружены катодами, что также увеличивает рабочую анодную
поверхность.
Надежный
токопровод к анодам без применения свинца, подвод тока к катодной сетке через корпус
катода и приваренный к нему каркас обеспечивают в электролизерах БГК
назначенный перепад напряжения в контактах и подводе тока к электродам.
Возможность при монтаже точного регулирования и фиксации положения анодов
позволяет точно установить расстояние между электродами и снизить напряжение на
электролизере.
Конструкция
электролизера дает возможность работать при высокой температуре анолита – до 95–100 °С,
что в свою очередь способствует снижению рабочего напряжения на электролизере и
увеличению выходов по оку. Для уменьшении потерь тепла и улучшения санитарных
условий работы в цехе электролиза наружные поверхности катода электролизера
покрываются слоем тепловой изоляции. Электролизер компактен и полностью
герметичен, что устраняет утечки электролитов и газов.
За счет
большой высоты крышки электролизера обеспечивается возможность изменения уровня
анолита в пределах от 50 до 300–400 мм над верхним краем катода. Поэтому
электролизеры работают с подачей постоянного количества рассола, необходимого
для получения щелочи концентрацией 130–140 г./л . Контроль питания
электролизера осуществляется обычно с помощью ротаметра. На некоторых заводах
подача рассола в каждый электролизер регулируется по уровню анолита, который
устанавливается в зависимости от состояния диафрагмы и изменяется по мере ее
старения. Для установления требуемого уровня анализируют католит, вытекающий из
электролизера.
Питание
электролизера рассолом может осуществляться через калибровочные отверстия
диафрагмы. Работа электролизера с подачей постоянного количества рассола и при
одинаковой нагрузке по току создает условия для получения максимально
возможного выхода по току при высокой концентрации щелочи.
5. Материальный баланс электролизера
В процессе
электролиза происходят изменения концентрации электролит, которые обусловлены
участием ионов в переносе тока, химическими процессами, протекающими на
электродах и а объеме электролита, испарением влаги и уносом ее с газообразными
продуктами электролиза – хлором и водородом.
В
электролизерах с твердым катодом объем католита меньше
объема поступающего на электролиз рассола .
Уменьшение объема связано с превращением хлорида натрия в гидроокись, имеющую
меньший молекулярный объем, расходом воды на химический процесс и испарение и
унос в виде паров с выделяющимися газами. Степень изменения объема католита:
,
где и - мольные концентрации
хлорида щелочного металла в исходном растворе и католите, соответственно;
- мольная концентрация
гидроокиси щелочного металла в католите.
Ниже приведен
расчет концентрации соли в анолите, а также соли и щелочи в католите с учетом
испарения и уноса влаги с газами.
Незначительный
расход воды, связанный с протеканием побочных реакций, не учитывается. Для
упрощения принято, что выход по току, температура и давление газов для анодного
и катодных продуктов одинаковы.
При подаче в
анодное пространство рассола, моляльные концентрации которого на 1000 г. воды (55,5
моль) поступит молей .
При степени
разложения соли через ячейку
должно быть пропущено фарадеев
электричества и на аноде должно выделиться г-экв
хлора.
Если процесс
электролиза проводить в условиях, исключающих электролитический перенос ионов из катодного пространства
в аноде, то количество ионов хлора, перенесенным током в анодные пространство
из катодного, составит г-ионов,
где - число переносы хлор-иона.
Общее
количество г-ионов хлора, находящееся в рассматриваемом объеме анолита и
поступающее затем в катодное пространство при стационарном процессе, составит:
,
или после
преобразования:
.
Учитывая, что
число переноса катиона , получим:
.
На аноде
выделяется молей газообразного хлора.
Если принебречь объемом и и подсасываемого к хлору
воздуха, то количество молей влаги, уносимой с хлор-газом в виде паров,
составит:
,
где - общее давление влажного
газа;
- парциальное давление
паров воды в хлоре над анолитом.
Моляльность
анолита можно определить из выражения:
или .
При .
На катоде
образуется молей гидроокиси натрия и
выделяется молей газообразного
водорода, при этом на химическую реакцию расходуется молей воды. Количество
воды, уносимой с водородом в виде паров воды, составит:
,
где – парциальное давление
паров воды в водороде над католитом.
Содержание
поваренной соли в католите определяется по разности между поступившим и
разложившимся количествами:
.
Содержание
воды в католите составит:
.
Моляльность
католита (по ) составит:
,
А по :
.
Суммарная
мольяность католита по и :
.
Степень
изменения количества воды в электролите в процессе электролиза:
.
Чтобы
перевести единицы концентрации из мольяльности в г/л ( ) можно воспользоваться
выражением:
,
где - моляльность раствора;
- плотность раствора;
- молекулярный вес
растворенной соли.
Моляльность
католита по поваренной соли и каустической соде составит:
,
.
Снижение
парциального давления паров воды над электролитическими щелаками может быть приближенно
принято равным сумме снижения парциального давления над соответствующими
растворами гидроокиси натрия .
.
При таком
подсчете парциальные давления паров воды над католитом мало отличаются от
парциального давления над насыщенным раствором поваренной соли при той же
температуре.
Если принять,
что , то тогда получаем:
.
При
парциальном давлении паров воды над электролитом выше 400–500 мм. рт. ст.
унос паров воды резко возрастает. При парциальном давлении паров около 720 мм.
рт. ст. теоретически с газами должно быть унесена вся вода из раствора. Поэтому
при сильном повышении температуры электролиза происходит интенсивное испарение
влаги, пересыщение раствора и выделения кристаллов соли, которые забивают поры
диафрагмы и приводят к нарушению нормального процесса электролиза.
Материальный
баланс элетролизера осложняется наличием примесей, например соды, щелочи и
сульфатов, в мешающем электролизу растворе, протеканием процессов выделения на
аноде кислорода и окисления графитовых анодов в образованием в основном
двуокиси углерода, а также вторичных процессов растворения и гидролиза хлора в
анолите и последующих реакций между растворенным хлором и ионами с образованием гипохлорита
и хлората. Однако для практических целей приведенная выше приближенная схема
расчета материального баланса дает достаточно точные результаты.
Образующийся
в электролизере гипохлорит практически полностью восстанавливается на катоде с
образованием исходного хлорида натрия. Количество хлората натрия, уходящего с
катодными щелоками, не превышает обычно десятых долей процента от
образовавшейся каустической соды. Поэтому в практических балансах электролизера
эти процессы могут не учитываться. Расчет воды и образования двуокиси углерода
за счет сгорания анодов в связи с выделением кислорода можно учесть
приближенно, приняв, что снижение выхода по току связано лишь с разрядом ионов на анод.
Расход воды
на разложение составит , а количество
двуокиси углерода, образовавшегося от сгорания анодов, равно . При температуре 90–95 °С,
поддерживаемой в современных электролизерах, потери воды на побочные процессы
не превышает 0,5–1,0% общего расхода воды на химические процессы и испарение.
Заключение
В настоящее
время едкая щёлочь и хлор вырабатываются тремя электрохимическими методами. Два
из них – электролиз с твёрдым асбестовым или полимерным катодом (диафрагменный
и мембранный методы производства), третий – электролиз с жидким ртутным катодом
(ртутный метод производства). В ряду электрохимических методов производства
самым лёгким и удобным способом является электролиз с ртутным катодом, но этот
метод наносит значительный вред окружающей среде в результате испарения и
утечек металлической ртути. Мембранный метод производства самый эффективный,
наименее энергоемкий и наиболее экологичный, но и самый капризный, в частности,
требует сырье более высокой чистоты.
Едкие щёлочи,
полученные при электролизе с жидким ртутным катодом, значительно чище
полученных диафрагменным способом. Для некоторых производств это важно. Так, в
производстве искусственных волокон можно применять только каустик, полученный
при электролизе с жидким ртутным катодом. В мировой практике используются все
три метода получения хлора и каустика, при явной тенденции в сторону увеличения
доли мембранного электролиза. В России приблизительно 35% от всего выпускаемого
каустика вырабатывается электролизом с ртутным катодом и 65% – электролизом с
твёрдым катодом (диафрагменный и мембранный методы).
Список литературы
1. Аблонин Б.Е. Основы
химических производств. – М.: Химия, 2001.
2. Бесков В.С. Общая
химическая технология и основы промышленной экологии. – М.: Химия, 1999.
3. Бесков В.С. Моделирование
каталитических процессов и реакторов. – М.: Химия, 1991.
4. Кутепов А.М. Общая
химическая технология. – М.: Высшая школа, 1990.
5. Лебедев Н.Н. Химия
и технология основного органического и нефтехимического синтеза. – М.: Химия,
1981.
6. Позин М.Е. Технология
минеральных удобрений. – Л.: Химия, 1983.
7. Расчеты
химико-технологических процессов. / под ред. Мухленова И.П. – Л.: Химия,
1982.
8. Степанов В.С. Анализ
энергетического совершенствования технологических процессов. – Новосибирск:
Наука, 1984.
9. Фролов Ю.Г. Физическая
химия. – М.: Химия, 1993.
10. Химико-технологические системы. / под ред.
Мухленова И.П. – М.: Химия, 1986.
|