Реферат: Заготовки и процесс обработки оптических деталей
Реферат: Заготовки и процесс обработки оптических деталей
Министерство образования Республики Беларусь
Учреждение образования
«БЕЛОРУССКИЙ ГОСУДАРСТВЕННЫЙ УНИВЕРСИТЕТ
ИНФОРМАТИКИ И РАДИОЭЛЕКТРОНИКИ»
Кафедра электронной техники и технологии
РЕФЕРАТ
На тему:
«Заготовки и процесс обработки оптических деталей»
МИНСК, 2008
1.
ЗАГОТОВКИ ОПТИЧЕСКИХ ДЕТАЛЕЙ
Заготовки
оптических деталей из оптического стекла получают в виде прямоугольных или
круглых пластин, плиток, штабиков и прессовок (рис.1). На обработку заготовки
поступают партиями, состоящими из заготовок одного наименования и размера. К
партии прикладывают сопроводительный паспорт, в котором указывают фактические
значения оптических характеристик стекла, показатели качества, номера варок и
отжига. При обработке нельзя смешивать заготовки разных партий, так как в ряде
случаев при сборке изделия оптических детали комплектуют с учетом фактических
значений показателя преломления и дисперсии.
Наиболее
рациональной заготовкой деталей типа линз и призм является прессовка (рис.1.1,
д), повторяющая конфигурацию готовой детали. Для изготовления прессовок
необходима технологическая оснастка: пресс-форма, шаблоны и др. Стоимость
оснастки окупается только при прессовании определенного числа заготовок.
Поэтому ГОСТ 13240 “Заготовка оптического стекла” установлен минимальный объем
партии заготовок, поставляемых в виде прессовок.
Масса заготовки, г |
Объем при заказе, шт., не менее |
1,5-10 |
2000 |
10-15 |
1000 |
50-100 |
250 |
100-250 |
150 |
250-500 |
100 |
При
заказе меньшего числа заготовок их изготовляют в виде плитки, штабиков с
размерами, кратными размерам единичной заготовки (см. рис.1.1, а-г).
Технические
условия (ТУ) на заготовку составляют на основе чертежа оптической детали. В ТУ
приводится эскиз заготовки с необходимыми для изготовления и контроля размерами
и допусками, указывается марка стекла, технические требования к стеклу и
заготовке, масса и число заказываемых заготовок в штуках (рис.1.2).
На
эскизе рядом с размерами заготовки в скобках проставляют как справочные
соответствующие размеры готовой детали. Для деталей с размерами более 150 мм на
заготовке указывают также световой диаметр или расположение рабочей зоны. Вне
рабочей зоны дефекты типа одиночных пузырей и узловых свилей не нормируются.
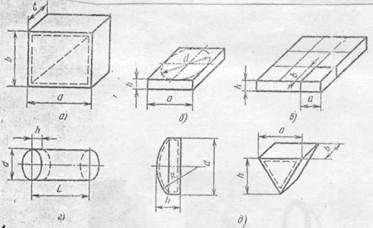
Рис.
1.1 Заготовки оптических деталей:
а - прямоугольная пластина;
б - плитка для круглых деталей; в - плитка с размерами, кратными размерам
единичной заготовки; г - штабик с круглым сечением; д - прессовки линзы и призмы
Маршрутную
технологию (МТ) изготовления заготовки технолог разрабатывает с учетом
требований к стеклу, размерам партии и габаритным размерам детали. Выбирается
метод и последовательность операций на основе типовых технологических
процессов. Номер маршрутной технологии указывают в ТУ на заготовку.
Коэффициент
запуска (КЗ), равный отношению массы сырьевого стекла, необходимого для
изготовления заготовки, к теоретической массе заготовки, устанавливают на
основе имеющихся нормативов и выбранной МТ. Коэффициент запуска зависит от
требований к показателям качества стекла.
Размеры
заготовки рассчитывают с учетом необходимого припуска на обработку и предельных
отклонений размеров. Значение припуска зависит от выбранной технологии, метода
базирования детали при обработке и толщины дефектного слоя поверхности
заготовки. Дефектный слой образуется при термических процессах формообразования
ввиду включения в поверхность стекла мелкодисперсных частичек порошка подсыпки
(“шамота”), появления вмятин, складок и поверхностный посечек. При механических
методах разделки стекла: распиливании, сверлении и др. – образуется
трещиноватый поверхностный слой, сколы и царапины.
Глубина
залегания дефектов на поверхности прессованной заготовки размером до 50 мм с
нижней (“зашамоченной”) стороны не должна превышать 0,8 мм, а с верхней
(“светлой”) стороны – 0,5 мм. У заготовок диаметром 50-150 мм соответственно
1,5 и 0,8 мм. Существуют оговоренные стандартом оговоренные стандартом
ограничения размеров заготовок.
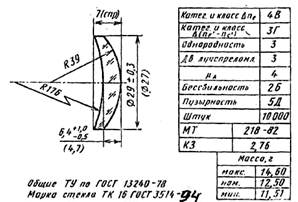
Рис.1.2
Образец, оформления технических условии на заготовку
линзы
Для
заготовок – прессовок размером до 150мм толщина заготовок не должна быть менее
3 мм для линз и 4 мм для плоских деталей, отношение диаметра или диагонали
заготовки и ее толщине должна быть в пределах от 15:1 до 1,25:1.
Значения
и расположение полей допусков на размеры заготовок установлены на основе
анализа точностных возможностей существующих технологических процессов.
Предельные
отклонения размеров заготовки регламентируют ГОСТ 13240-78 в зависимости от ее
диаметра или наибольшей стороны.
Таблица
1.1
Диаметр
или наибольшая сторона заготовки, мм |
Допуск
заготовки, мм |
Просвет
в середине сферической поверхности при контроле радиусным шаблоном, мм, не
более |
Отклонение
от плоскостности плоских поверхностей, мм, не более |
диаметра |
стороны
заготовки прямоугольного сечения |
толщины
по оси |
До
20 |
±0,3 |
±0,5 |
+1,5
-0,5
|
0,5 |
0,4 |
20-50 |
±0,3 |
±0,5 |
+1,0
-0,5
|
0,8 |
0,5 |
50-80 |
±0,5 |
±0,5 |
+1,0
-0,5
|
1,0 |
0,6 |
80-120 |
±0,8 |
±0,8 |
+1,5
-0,5
|
1,2 |
0,8 |
120-150 |
±1,0 |
±1,0 |
+1,5
-0,5
|
1,5 |
1,0 |
150-250 |
±1,5 |
±1,5 |
+2,0
-1,0
|
- |
1,2 |
250-360 |
±2,0 |
±2,0 |
±2,0 |
- |
1,5 |
360-500 |
+5,0
-2,0
|
+5,0
-2,0
|
+5,0
-2,0
|
- |
2,0 |
Минусовый
допуск должен быть приплюсован к номинальному размеру соответствующего
параметра заготовки, который рассчитывается из номинального размера ОД плюс
припуска на операции, выполнение которых необходимо для его получения.
Последовательно
порядок припусков следующий:
-
на распиливание кратных заготовок пилами (табл.1.2)
Таблица
1.2
Глубина распиливания, мм |
Расчетная ширина выемки при
распиливании, мм |
До 10 |
1,5 |
Свыше 10 до 65 |
2,0 |
65 |
2,5 |
Толщина
диска пилы принята равной 1 мм. При применении дисков иной толщины ширина
выемки определяется по формуле , где - толщина диска пилы и - расчетная толщина ширины
выемки (табл.2).
-
на обдирку заготовок (табл.1.3)
Таблица
1.3
Припуски
на обдирку (в миллиметрах)
Форма
детали |
Вид
заготовки |
Профиль
обрабатываемой поверхности |
Размер
диска линзы или наибольшей стороны прямоугольной детали |
до
10 |
свыше
10 до 25 |
свыше
25 до 40 |
свыше
40 до 65 |
свыше
65 |
величины
припуска на одну поверхность |
на
любую сторону |
1-я
поверх
ность
|
2-я
поверх
ность
|
1-я
поверх
ность
|
2-я
поверх
ность
|
1-я
поверх
ность
|
2-я
поверх
ность
|
1-я
поверх
ность
|
2-я
поверх
ность
|
Сферические
линзы |
Прессовки
со сферическими поверхностями |
Выпуклый
и вогнутый |
- |
0,2 |
0,3 |
0,3 |
0,4 |
0,4 |
0,6 |
0,6 |
0,9 |
Прессовка
с плоской поверхностью |
Выпуклый |
0,4 |
0,5 |
Плоский |
0,2+h |
0,3+h |
0,2+h |
0,3+h |
0,3+h |
0,4+h |
0,4+h |
0,6+h |
вогнутый |
0 |
0 |
0 |
0 |
Предварительно
плоскошлифовальные |
Выпуклый |
h |
h |
h |
h |
Вогнутый |
|
|
|
|
|
|
|
|
|
Призмы
и детали, ограниченные плоскостями |
Любые,
кроме обколотых |
Плоский |
0,4 |
0,5 |
0,5 |
0,6 |
0,6 |
0,7 |
0,7 |
0,9 |
0,9 |
Обколотые |
1,5 |
1 |
1 |
1,25 |
1,25 |
1,5 |
1,5 |
1,75 |
1,75 |
-
на грубое шлифование (табл. 1.4)
Таблица
1.4
Припуски
на грубое шлифование
Размер диаметра или наибольшей стороны |
Величина припуска на 1-ю поверхность |
До 10 |
До 0,1 |
Свыше 10 |
Свыше 0,16 |
-
на мелкое (тонкое) шлифование и полирование (табл. 1.5)
-
на кругление (табл. 1.6)
Таблица
1.5
Припуски
на мелкое шлифование и полирование
Диаметр
или размер наибольшей стороны, мм |
Заданная
точность изготовления |
Величина
припуска на одну сторону, мм |
Линейных
размеров (толщина или высота), мм |
Углов
призм, мин |
До
10 |
До
0,1 |
Любая |
0,1 |
Свыше
0,1 |
До
6 |
Свыше
6 |
0,06-0,07 |
Свыше
10 до 65 |
До
0,3 |
Любая |
0,15 |
Свыше
0,3 |
До
4 |
Свыше
4 |
0,07-0,08 |
Свыше
65 |
До
0,3 |
Любая |
0,2 |
Свыше
0,3 |
До
3 |
Свыше
3 |
0,07-0,08 |
Таблица
1.6
Припуски
на кругление
Заготовки |
Толщина |
Диаметр
заготовки линз |
Припуски
на диаметр |
До
10 |
Свыше
10 до 25 |
Свыше
25 до 40 |
Свыше
40 до 65 |
Свыше
65 до 100 |
Свыше
100 |
Прессовки,
предварительно шлифованные |
любая |
1 |
1,5 |
2 |
2,5 |
3 |
3,5 |
До
5 |
2 |
2,5 |
3 |
3,5 |
4 |
5 |
Свыше
5 до 10 |
3 |
3,5 |
4 |
4,5 |
5 |
6 |
Обколотые |
Свыше
10 до 15 |
- |
- |
5 |
6 |
7 |
8 |
-
на центрировку линз (табл. 1.7)
Таблица
1.7
Припуски
на центрировку
Диаметр
линз |
Свыше
1,5 до 2,5 |
Свыше
2,5 до 4 |
Свыше
4 до 6 |
Свыше
6 до 10 |
Свыше
10 до 15 |
Свыше
15 до 25 |
Свыше
25 до 40 |
Свыше
40 до 65 |
Свыше
65 до 100 |
Свыше
100 |
Величина
припуска на диаметр |
0,4 |
0,6 |
0,8 |
1 |
1,2 |
1,5 |
2 |
2 |
2,5 |
3 |
2. СУЩНОСТЬ ПРОЦЕССОВ
ОБРАБОТКИ ОПТИЧЕСКИХ ДЕТАЛЕЙ
Шлифование свободным абразивом
Стекла и другие хрупкие оптические
материалы шлифуют свободным абразивом, используя жесткий металлический
инструмент 1 (рис. 2.1), который давит на заготовку 4 с силой Р и перемещается
с относительной скоростью v.
Между заготовкой и инструментом располагаются зерна 2 абразивного порошка,
смешанные с жидкостью 3. При перемещении инструмента по заготовке они взаимно
изнашиваются под действием абразивных зерен и притираются друг к другу.
Природа обработки стекла водными
суспензиями зерен абразивных порошков имеет двоякий характер. С физической
стороны—это процесс механического разрушения стекла абразивными зернами.
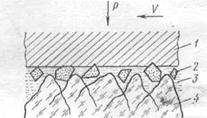
Рис. 2.1.Шлифование свободным абразивом
С химической стороны — это
взаимодействие воды с растворимыми компонентами стекла.
Основой механического разрушения стекла
является возникновение внутри поверхностного слоя хрупкого тела трещин,
пересекающихся между собой и создающих ослабление связей между соседними
частицами материала. Абразивные зерна вместе с водой находятся между рабочей
поверхностью металлического инструмента и обрабатываемой поверхностью стекла.
Эти поверхности имеют неровности, размеры которых соизмеримы с размерами
абразивных зерен. При относительном движении стекла но инструменту абразивные
зерна перекатываются или проскальзывают с некоторой скоростью.
Наиболее крупные из зерен
взаимодействуют со стеклом и инструментом. Более мелкие зерна переносятся водой
до тех пор, пока крупные не раздробятся, после чего и мелкие зерна вовлекаются во
взаимодействие со стеклом и инструментом.
Под действием ударов зерна раскалываются
на более мелкие зерна взаимодействуют не только со стеклом и инструментом, но и
между собой, перетираясь и еще более измельчаясь. Измельченные зерна, смешанные
с осколками стекла, уносятся из-под шлифовальника вместе с водой.
На обрабатываемой поверхности создается
разрушенный слой, верхняя часть которого (рельефный слой) состоит из впадин и
конических выступов и трещиноватого слоя. Разрушение происходит после
многократного воздействия абразивных зерен на одно и то же место стекла.
Образующиеся трещины пересекаются и между ними образуется объем, отошедший от
остальной соседней массы стекла. Этот объем под действием абразивных зерен и
воды удаляется с поверхности стекла. Высота поверхностных неровностей составляет
примерно 1/4—1/3 размера зерен. Под
рельефным слоем образуется трещиноватый слой глубиной в 2—4 раза больше первого.
По мере уменьшения абразивных зерен величина поверхностных неровностей
уменьшается.
Равномерность структуры шлифованной
поверхности нарушается дефектами — царапинами, точками и выколками. Они
образуются в том случае, когда зерно надолго закрепляется в шлифовальнике или
имеются зерна размером в несколько раз больше, чем зерна основной фракции. В последнем
случае крупные зерна не раскалываются и оставляют на стекле крупные царапины и
выколки.
Химическое взаимодействие воды с
растворимыми компонентами стекла проявляется в том, что вода активно вступает в
реакцию с поверхностным слоем стекла, образуя внутри трещин коллоидную пленку
кремневой кислоты, которая занимает объем больший, чем стекло. Таким образом,
вода расширяет и углубляет трещины, ускоряя и облегчая удаление осколков стекла
при абразивной обработке.
Шлифование закрепленным абразивом
На заготовительных операциях, а в
последнее время и па операциях среднего и мелкого шлифования, используют
инструменты с закрепленным абразивом. Особенно широко этот способ обработки,
стал применяться в оптической промышленности после появления синтетических алмазных
порошков. Это позволило наладить выпуск алмазных инструментов, в которых
алмазные зерна 2 (рис. 2.2.) определенной крупности жестко закреплены в теле
инструмента металлической связкой из сплавов меди и железа.
Шлифование таким инструментом 1 (рис. 2.2)
производится на станке при перемещении его по заготовке 5 со скоростью v
и давлением Р. Между инструментом и заготовкой находятся вырванные из
связки абразивные или алмазные зерна 3 и слой смазочно-охлаждающей жидкости 4.
Кроме силового воздействия инструмента на заготовку он подается на глубину
снимаемого припуска с помощью механизма поперечной подачи станка.
Процесс обработки закрепленным абразивом
отличаются от способа обработки свободным абразивом. Быстро движущиеся и жестко
закрепленные в инструменте абразивные зерна при врезании в обрабатываемую
поверхность образуют трещины, опережающие перемещение зерен. В результате па
поверхности возникают выколки, которые обусловливают съем материала заготовки.
Закрепленные зерна с течением времени
затупляются, усилие резания увеличивается, и они выкрашиваются из связки, но не
раскалываются. Вместо них вступают в работу новые зерна того же размера, и
процесс шлифования идет с равномерной интенсивностью.

Рис. 2.2. Шлифование закрепленным
абразивом
Обработка таким способом сопровождается
значительным нагревом контактирующих поверхностей и образованием большого
количества отходов. Для уменьшения температуры и трения между инструментом и
заготовкой, а также для удаления отходов в процессе шлифования применяют
обильную подачу смазочно-охлаждающей жидкости.
Удельный объем удаляемого припуска
пропорционален крупности, твердости, прочности абразивных зерен и связки.
Стекло обрабатывается закрепленными абразивными зернами приблизительно в 20 раз
быстрее, чем свободными. Большая скорость шлифования стекла закрепленным
абразивом по сравнению с обработкой свободным абразивом объясняется различными
причинами.
Закрепленный абразив вызывает не
разрозненные точечные выколки, а сплошные царапины. Закрепленные абразивные
зерна работают как резцы. Закрепленные зерна разрушаются только при воздействии
на стекло, а свободные измельчаются и от взаимного перетирания. Неоднородность
размеров зерен при данном способе не проявляется, поскольку они работают только
выступающими из связки острыми гранями. Рабочее давление инструмента
сосредотачивается на небольшом участке поверхности зерен, выступающих из
связки, и достигает значительных величин. Скорость резания закрепленным абразивом
составляет от 10 до 50 м/с, а свободным абразивом 3—7 м/с.
Полирование
Процесс полирования оптических деталей
связан с достижением величины микронеровностей значительно меньшей длины волны
света, т.е. менее 0,05 мкм. В этом случае поверхность становится прозрачной для
оптического излучения. Кроме того, погрешности формы и размеров этой
поверхности также составляют доли микрометра.
В процессе полирования (рис. 2.3)
упругопластичный слой 2 (обычно смола, сукно или фетр) полировальника 1,
пластически деформируясь, выглаживается по шлифованной поверхности заготовки
5. Зерна 3 полирующего порошка находятся между полиро-вальником и заготовкой,
поверхностные неровности которых значительно больше зерен полирующего порошка.
Размеры зерен порошка обычно лежат в пределах от 0,5 до 2 мкм.
Вода 4, в которой взвешены зерна, в
первые моменты подачи оказывает противодавление нажиму, но затем растекается и
зерна закрепляются в наружном слое смолы. Часть зерен, еще не закрепившихся в
смоле, перекатывается или, закрепившись на мгновение, продолжает движение.
Зерна срезают вершины рельефного
шлифованного слоя, которые становятся гладкими, полированными. В дальнейшем
размеры полированных площадок увеличиваются, высота неровностей уменьшается до
сотых долей микрометра.
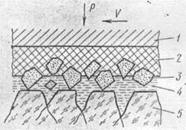
Рис. 2.3. Полирование
В начале процесса полирования работа
закрепленных зерен эффективнее, так как площадь впадин еще велика и
перекатывающимся зернам негде закрепляться. Толщина сдираемых пленок
уменьшается при расширении площади полированных участков и к концу процесса
обработки приблизительно равна высоте остающихся поверхностных неровностей. Под
действием воды коллоидная пленка образуется и сдирается вновь все более тонкими
слоями.
Пластические свойства смолы,
удерживающей зерна, к коллоидной пленки способствуют тому, что работа зерен
полирующего порошка не сопровождается появлением царапин. Благодаря
пластическим свойствам коллоидной пленки борозды, образующиеся от снятия
материала, затягиваются и заполняются продуктами разрушения стекла.
Припуски операционные
Понятие о припуске.
Технологический процесс механической обработки оптических деталей состоит из
нескольких операций, которые выполняют на одном определенном рабочем месте.
Таких операций обычно не менее трех: заготовительные, шлифование и полирование.
Готовые детали получают из заготовок,
последовательно удаляя с их поверхностей материал. Причем на каждом переходе с
заготовки удаляют определенный слой материала, вследствие чего ее размеры и
масса уменьшаются, а обрабатываемые поверхности постепенно приобретают форму и
размеры готовой детали. Для суждения о разности размеров заготовки и детали
введено понятие о припусках.
Припуском
называют избыточный (сверх размера детали по чертежу) слой материала заготовки,
удаляемый в пpoцессе обработки. Как
правило, припуск назначают па сторону в виде слоя материала по толщине. Припуск
может быть с двусторонним и односторонним расположением.
Для экономии материала, удешевления
обработки детали, обеспечения эффективности технологического процесса припуск
необходимо назначать, исходя из условий получения требуемого качества при
обеспечении наименьшей трудоемкости обработки. Увеличенные припуски на
обработку приводят к ненужным затратам времени, материала, энергии и
абразивного порошка, что увеличивает себестоимость изделия. Уменьшение припуска
удешевляет продукцию, однако при занижении припуска затрудняется технология
обработки детали, не гарантируется удаление дефектного и трещиноватого слоя
материала, пс обеспечивается требуемая точность и заданная шероховатость
поверхностей.
Величину припуска определяют в
зависимости от материала заготовки, вида, размеров, величины дефектного слоя на
обрабатываемой поверхности, формы детали, требуемой точности и заданной
шероховатости, сложности процесса обработки и других факторов.
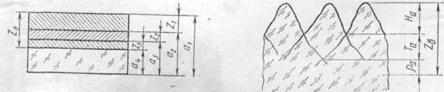
Puc. 2.4 Схема
расположения Рис. 5 Распределение припуска
межоперационных припусков на одну
сторону заготовки
Распределение припуска. Различают общие,
межоперационные и межпереходные припуски. Общий припуск равен разности размеров
заготовки и детали. Межоперационным или межпереходным припуском называют слой
материала, снимаемый при выполнении определенных операций или переходов.
Численно межоперационный припуск равен
разности размеров заготовки, полученных при двух смежных операциях. Например,
при обработке плоской поверхности пластины (рис. 2.4)
z1=
α1 - α2; z2=
α2 - α3; z3
= α3 - α4 ,
где z1,z2,z3
— межоперационные припуски; α1, α2, α3,
α4 — межоперационные размеры. Общий припуск zо
= а1 - а4 определяют как сумму всех межоперационных
припусков.
Величину припуска на сторону заготовки
определяют из зависимости (рис. 2.5) zB=
(Hа
+ Ta) + (ρa
+ ξ ), где zB
—минимальный припуск па обработку (на сторону); Hа—
высота микронеровностей, которая зависит от величины зерен абразива, материала
инструмента и других факторов предыдущей обработки; Ta
— глубина дефектного поверхностного слоя; ρa
— суммарное значение пространственных отклонений обрабатываемой поверхности; ξ
—погрешность на установку заготовки. Последнюю сумму двух слагаемых обычно
принимают равной одной пятой от суммы первых двух слагаемых. Если заготовку
обрабатывают с двух сторон, то припуск на две стороны удваивают. Значение (Hа
+ Ta) для прессовок
принимают равным 0,3—0,5 мм, после обдирки 0,1—0,3 мм, среднего шлифования
0,02—0,05 мм.
Если при обработке плоских поверхностей
припуск снимают и основном равномерными слоями, за исключением удаления погрешностей
угловых размеров, то при обработке сферических поверхностей это выполняют как
равномерными, так и неравномерными слоями. Экономически целесообразно снимать
припуск, со сферических поверхностей равномерными слоями, но в этом случае для
каждого перехода (рис. 2.6) необходимо назначать различные радиусы (R1
— R3)
шлифовальников, которые рассчитывают по определенным формулам
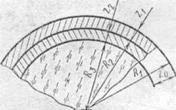
Рис. 2.6. Расположение припуска на
сферической поверхности.
Если же припуск снимают инструментами
одного радиуса, то толщина удаляемого слоя будет неравномерной, причем для
выпуклыx поверхностей она в
центре будет максимальной, а для вогнутых — минимальной.
В оптическом производстве теория
переходов устанавливает связь между крупностью зерна абразива, толщиной слоя
абразива, высотой микронеровностей и дефектного слоя со значениями радиусов
кривизны шлифовальников и детали для каждого перехода. Обрабатываемые
поверхности заготовок или блоков, у которых отношение диаметра к радиусу
кривизны менее 0,8 шлифуют одним инструментом, используя разные микропорошки.
Это объясняется тем, что изменение радиусов шлифовальников невелико и не
сказывается при смене переходов.
ЛИТЕРАТУРА
1.
Малов А.Н.,
Законников Обработка деталей оптических приборов. Машиностроение, 2006. - 304
с.
2.
Бардин А.Н.
Сборник и юстировка оптических приборов. Высшая школа, 2005. - 325с.
3.
Кривовяз Л.М.,
Пуряев Д.Т., Знаменская М.А. Практика оптической измерительной лаборатории.
Машиностроение, 2004. - 333 с.
|