Курсовая работа: Изготовление торцовой насадной фрезы
Курсовая работа: Изготовление торцовой насадной фрезы
Федеральное агентство по
образованию
Пензенский колледж
управления
и промышленных технологий
им. Е.Д. Басулина
ПОЯСНИТЕЛЬНАЯ ЗАПИСКА
к курсовому проекту
по дисциплине
«ТЕХНОЛОГИЯ
МАШИНОСТРОЕНИЯ»
ПКУПТ
4.407.151001.05.1.21
2008
Введение
При
изготовлении машин, двигателей, приборов, станков широко применяют обработку
металлов резанием. Обработка резанием на металлорежущих станках или вручную
невозможна без применения необходимых для этого орудий труда – режущих
инструментов.
Качество
режущего инструмента характеризуется его надежностью, т.е. его способностью
безотказно работать согласно своему назначению, сохраняя при этом
предусмотренные техническими условиями показатели. К таким показателям
относятся размерная и геометрическая точность, стойкость. Характеризует
качество режущего инструмента. Стойкость режущего инструмента – это способность
длительное время работать между двумя переточками. Чем больше будет это время,
тем выше качество такого инструмента.
Производство
режущих инструментов на современном уровне требует соответствующей подготовки
специалистов – инструментальщиков. Подготовка специалистов среднего звена –
техников – инструментальщиков – сосредоточена в инструментальных техникумах.
При
выполнении курсового проекта мы научимся:
1.
проектировать
тех. процессы режущего инструмента;
2.
выбирать
операционные припуски;
3.
рассчитывать
общие припуски;
4.
выбирать
базы;
5.
выбирать
оборудование;
6.
выбирать
приспособление (технологическую оснастку)
7.
рабочий
режущий инструмент
8.
заполнять
технологическую документацию
9.
рассчитывать
технологическую себестоимость обработки, рассчитав предварительно режимы
резания на нужные операции и нормы штучного времени.
1. Основной
раздел
1.1
Конструкция
и служебное назначение изготавливаемой детали
Фрезы –
многолезвийный инструмент, применяющийся на фрезерных станках для обработки
плоских и фасонных поверхностей, фрезерования уступов, плоскостей и пазов в
деталях из различных сталей, алюминиевых сплавов, меди, легких и цветных
металлов и сплавов. В курсовом проекте проектируется и рассчитывается фреза торцовая
насадная диаметром 63 мм и шириной В=40 мм. Данная фреза
изготовляется двух типов: тип I – фрезы торцовые насадные с мелким зубом и тип II – фрезы торцовые
насадные с крупным зубом. Моя фреза относится ко второму типу. Число зубьев Z=8. Для улучшения равномерности
фрезерования и отвода стружки фреза имеет винтовые стружечные канавки с углом
наклона W=35–400.
В централизованном порядке фрезы изготовляются праворежущими, а по соглашению с
потребителем – леворежущими. небольшое количество зубьев на фрезах улучшает
условия для отвода стружки и повышает виброустойчивость фрез. Для
дополнительного увеличения виброустойчивости фрез по соглашению с потребителем
фрезы изготавливаются с неравномерным окружным шагом зубьев.
Геометрические
параметры режущих кромок фрезы, изготавливаемой в централизованном порядке:
передний угол в нормальном сечении к режущей кромке на цилиндре jn=150, на торце jт=120; задний
угол в сечении перпендикулярном к оси фрезы, α=140; задний угол
в сечении к режущей кромке на торце α1=80.
Радиальное
биение режущих кромок (относительно оси посадочного отверстия) для смежных
зубьев фрез Ø63–80 мм – не более 0,03 мм.
Фреза
изготавливается из стали Р6М5 по ГОСТ 19265–73.
При
фрезеровании углеродистых и легированных сталей и чугуна
рекомендуется
применять фрезы из быстрорежущей стали марок Р12 и Р6М3 по ГОСТ 9373 – 60 и
Р0М5 по ЧМТУ 1–865–70 с твердостью после термообработки HRC62–65. Допуск на диаметр
посадочного отверстия d по А, ОСТ 1012. Размеры шпоночного паза по ГОСТ 9412–70.
Основные размеры по ГОСТ 9304–69. Технические требования по ГОСТ 1695–67.
1.2
Анализ
технологичности детали
Одним из
эффективных путей решения задач при проектировании является внедрение принципов
технологичности конструкции. Под этим термином понимают такое проектирование,
которое при соблюдении всех эксплуатационных качеств обеспечивает минимальную
трудоемкость изготовления, материалоемкость и себестоимость, а так же
возможность быстрого освоения выпуска изделий в заданном объеме с
использованием современных методов обработки и сборки.
Технологичность
– важнейшая техническая основа, обеспечивающая использование конструкторских и
технологических резервов для выполнения задач по повышению
технико-экономических показателей изготовления и качества изделий. Работа по
улучшению технологичности должна производиться на всех стадиях проектирования и
освоения в производстве выпуск изделий.
Технологичность
конструкций деталей обуславливается:
А)
рациональным выбором исходных заготовок и материалов;
Б)
технологичностью форм деталей;
В)
рациональной постановкой размеров;
Г)
назначением оптимальной точности размеров, формы и взаимного расположения
поверхностей, параметров шероховатости и технических требований.
Технологичность
деталей зависит от типа производства, а так же от условий работы детали и
сборочных единиц в изделии и условий ремонта.
2. Специальный
раздел
2.1 Характеристика
заданного типа производства
Тип
производства для изготовления фрезы торцовой насадной с годовой программой
выпуска , будет являться серийное
производство.
Серийным
производством называется такое производство, в котором изделия изготовляются
партиями, регулярно повторяющимися через определенный промежуток времени.
Серийное производство в инструментальной промышленности организуется для
изготовления изделий одного вида. При этом номенклатура может доходить до
нескольких сотен типоразмеров. В данном типе производства применяются станки
общего назначения, которые располагаются в цехах по типам (группа токарных
станков, фрезерных, сверлильных и т.д.). Для этого выделяются участки в цехах с
замкнутым циклом обработки изделий одного вида.
2.2 Выбор
способа получения заготовки
Правильный
выбор заготовок и соответствующая их подготовка для механической обработки
являются весьма важными технико-экономическими вопросами.
При решении
этого вопроса надо стремиться к тому, чтобы форма и размеры исходной заготовки
были максимально близки к форме и размерам детали. Но повышение точности
размеров заготовки и получение ее более сложной формы чаще всего приводит к
увеличению себестоимости, особенно в мелкосерийном и единичном производствах.
На выбор
способа получения исходной заготовки влияют следующие факторы:
1.
вид
материала
2.
его
физико-механические свойства
3.
объем
выпуска изделий и тип производства
4.
размеры
и форма изделия
5.
характер
применяемого на проектируемом участке оборудования (универсальное или
специальное)
6.
производственные
возможности заготовительных цехов завода (кузнечного, литейного, сварочного и
т.п.)
в
машиностроении в зависимости от номенклатуры изделий и характера производства
применяют исходные заготовки в виде прутков круглого, прямоугольного,
квадратного сечений профильного и периодического проката, толстостенных
бесшовных труб; горячекатаных и холоднокатаных листов и полос; поковок,
получаемых методам свободной ковки, ковки в штампах, чеканки, ротационного
обжатия; отливок из стали, серого, ковкого, высокопрочного и антифрикционного
чугунов и цветных металлов, получаемых литьем в земляные формы из
быстротвердеющих смесей, в металлические
формы
(кокили), по выплавляемым моделям, в корковые или оболочковые формы и т.п.;
сварных заготовок для режущего инструмента и для корпусов машин, приборов и приспособлений;
пластин из быстрорежущей стали и твердых сплавов.
Изготовление
режущего инструмента целесообразно производить из поковок, а не из сортовой
горячекатаной стали, вследствие улучшения структуры – более равномерного
распределения карбидов и размельчения их. Ковку в штампах выгодно производить в
условиях серийного производства при изготовлении изделий, имеющих сложное
очертание, например зуборезных долбяков, угловых фрез и пр.
2.3 Выбор
и обоснование технологических баз
Базами
называются поверхности заготовки, за которые ее зажимают. В процессе
производства режущего инструмента различают черновые и чистовые базы. В данном
курсовом проекте при изготовлении фрезы торцовой насадной черновой базой
является наружная поверхность. При дальнейшей обработке поковку штампованную
зажимают в трех кулачковом патроне для обработке торца, отверстия и выточки в
отверстии, и здесь чистовой базой является обработанная наружная поверхность.
Отверстие в
корпусе фрезы торцовой насадной служит посадочным местом для отправки в
процессе фрезерования и, следовательно, является базой.
Таким
образом, черновыми называются базы, применяемые при обработке заготовок на
первых операциях; черновые базирующие поверхности предварительно не
обрабатывают. Чистовыми называют базы, применяемые при всей последующей
обработке; поверхности, применяемые за чистовые базы, предварительно
обрабатывают.
Чистовые базы
разделяют на основные и технологические. Основными базами называют такие
поверхности, которые ориентируют изделие – режущий инструмент в процессе его
работы на станке. У торцевой насадной фрезы чистовая база – отверстие, но оно
одновременно служит и основной базой, т. к. в процессе работы фреза
насаживается на рабочую оправку. Технологическими базами называют такие базы,
которые ориентируют заготовку только в процессе ее обработки. Наружная поверхность у фрезы
торцовой насадной может служить технологической базой.
2.4
Разработка технологического маршрута изготовления детали с выбором оборудования
и технологической оснастки
005 Отрезная.
Б. Абразивно-отрезной
автомат МФ-332
Т. Призма
ГОСТ 12194–66, центра ГОСТ 8742–75
О. Отрезать
заготовку в размере 1
Т. Круг
шлифовальный 0400х3х25. 16А50НСТ 23К1А.
ГОСТ 2424–75;
ШЦ-1 ГОСТ 166–80
010 Ковочная.
Б. Ковочный
молот модели М-132
О. Ковать
заготовку в размер 1,2,3
015
Термическая
Б. Печь
для отжига
О. Отжечь
заготовку.
020 Очистная
Б. Галтовочный
барабан
О. Очистить
заготовку
025 Токарная
Б. Токарно-винторезный
станок 16К20
Т. патрон
трехкулачковый самоцентрирующий ГОСТ 2675–80; Оправка 3. 1107–81
О. Подрезать
торец в размер 1
Т. Резец
токарный подрезной 16х25х140 Т15К6 ГОСТ 178–83; ШЦ-I ГОСТ 166–83.
030 Токарная
программная
Б
Токарно-винторезный станок с ЧПУ 16К20Т1
О. Патрон
трехкулачковый самоцентрирующий ГОСТ 2675–80
035 Фрезерная
Б. 6Т82Г
Т. Тиски
призматические
О. Фрезеровать
паз в размере 1, 2, 3
Т. Фреза
дисковая трехсторонняя ГОСТ 3755–78;
ЩЦ-I ГОСТ 166–83
040 Токарная
Б. Токарно-винторезный
станок 16К20
Т. Оправка
центровая 3. 1107–81; Центр упорный
1.
обточить
начерно в размер 1
2.
обточить
начисто в размер 2
Т. Резец
токарный проходной прямой 16х25х140; Т15 К6; ГОСТ 18879–73
045 Фрезерная
Б. 6Т12
050 Фрезерная
Б. 6Т12
Т. Оправка
3.1107–81; Поводковый патрон
О. Фрезеровать
стружечные канавки на торцы в размер 1, 2, 3
Т. Фреза
двухугловая Р6М5 по ТУ 2–035–526–76; Угломер ГОСТ 5378–88
055
Термическая
Б. Печи;
ванны.
О. Закалить
и отпустить.
060
Шлифовальная
Б. Внутришлифовальный
станок 3К228В
065 Заточная
Б. Универсально-заточной
станок 3М642
Т. Центр
вращающийся ГОСТ 8742–75
О. Заточить
зубья на торце по средней поверхности в размер 1
Т. Шлифовальный
круг ЧК 125х20 ЧК34А16НМ29К1А ГОСТ 2424–75
070 Заточная
Б. Универсально-заточной
станок 3М642.
Т. Центр
Вращающийся ГОСТ 8742–75
О. Заточить
по передней поверхности на цилиндре в размер 1
Т.
шлифовальный круг ЧК 34А16 НМ 29К1А ГОСТ 2424–75
075 Заточная
Б. Универсально-заточной
станок 3М642
Т. центр
вращающийся ГОСТ 8742–75
О. Заточить
зубья по цилиндру по задней поверхности в размер 1
Т.
шлифовальный круг ЧК 34А16 НМ29К1А ГОСТ 2424–75
080 Заточная
Б. Универсально-заточной
станок 3М642
Т. Центр
вращающийся ГОСТ 8742–75
О. Заточить
зубья на торце по задней поверхности в размер 1
Т. Шлифовальный
круг ЧК 34А16 НМ29К1А ГОСТ 2424–75
085
Шлифовальная
Б. Плоскошлифовальный
станок 3П722
Т. Центр
вращающийся ГОСТ 8742–75; поводок ГОСТ 3.1107–81
О. Довести
ленточку в размер 1
Т. Шлифовальный
круг ЧК34А16 НМ29К1А ГОСТ 2424–73
090
Шлифовальная
Б. Плоскошлифовальный
станок 3П722
Т. Поводковый
патрон ГОСТ 3.1107–81; оправка ГОСТ 3.1107–81
О. Довести
ленточку на зубе на торце в размер 1
Т. Шлифовальный
круг ПП 600х25х205 33А8 НСМ 26К1А ГОСТ 2424–83
095
Маркировочная
100
Контрольная
2.5 Расчет
припусков и межоперационных размеров
2Zобщ.=2Z8+2Z17;
2Z8=2Zобщ+2Zсм+2Zкр;
2Zобщ=2Zобщ+2Zсм+2Zкр+2Z17;
2Zчист.точ.=30%*2Zточ=30%*2Z8;
2Zобщ.=2*(0,8+0,3)=2,2 мм
[1, С. 7, m. 3]
2Zсм=2*0,55=1,1 мм [1,
С. 31, m
29]
2Zкр.=2*40*0,5\1000=0,04 мм
2Z8=2,2+1,1+0,04=3,34 мм
2Zчист.точ.=30%*2Zобщ.8
2Zчист.=0,3*3,34=1,002 мм
2Zчерн=3,34–1,002=2,338 мм
2Zобщ=2Z8+2Z17;
2Z17=0,9–0,5=0,4 [1, m. 9, С. 8]
Припуски на
линейные размеры общей длины инструмента.
2Zобщ.=3+0,002[1, С. 19,
m. 15]
2Zшлиф.=0,2 [1, C.28, m. 27]
2Zчист.точн.=1
2Zчерн.точн=1,8
Припуск на
заточку фрез
Z13=0,4÷0,6~0,5 мм
[1, C.26, m. 29]
№ оп. |
Наименование операции |
2Z |
h |
Ra |
17 |
Круглошлифовальная Доводка |
0,4 |
8 |
0,63 |
8a |
Чистовое обтачивание по наружн. пов-ти |
1,0 |
12 |
6,3 |
8б |
Черновое обтачивание по наружн. Пов-ти |
2,3 |
14 |
12,5 |
Расчет
операционных размеров на наружный диаметр рабочей части
1.
A17=63-0,046; h8; √ Ra
0,63
2.
A8a min чист= A17+2Z17=63+0,4=63,4 мм
A8a
max чист =A8 min чист+Tdh12=63,4+0,3=63,7 мм
A8a
чист=ø63,7-0,3;
h12; √ Ra 6,3
3.
Aб min черн= A8a чист max+2Zчист=63,7+1,002=64,702 мм
Aб max черн= A8a чист min+Tdh14=64,702+0,74=65,442 мм
A8 черн= ø65,442-0,74;
h14; √ Ra 12,5
Определяем
наружный диаметр заготовки для рабочей части фрезы.
Азаг. min= A8 черн. +2Z8 черн=65,442+2,338=67,78 мм
Азаг. max= Азаг. min+2Z8 черн+Tdзаг=67,78+1,0=68,78 мм
Ди.з=70+0,3-1,0(по
ГОСТ 7505–83)
Расчет
фактических припусков на черновую токарную обработку.
2Zmax= Азаг. max – А8 черн min=70,3–64,702=5,59 мм
2Zmin= Азаг. min – А8 черн max=69–65,442=3,558 мм
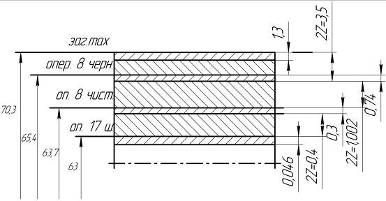
Расчет массы
заготовки
1.
Lи.з=L+5 мм=40+5=45 мм
2.
Определяем
массу круглой поковки
Мп=3,14
(70+1,3/2)2/4
3.
Диаметр
прутка, от которого будет отрезана заготовка для получения поковки
Lп/Дп=45/70=0,6=>Ди.з=(40÷45)·3√Мп=43∙3√1,519=49,4;
Ди.з=ø 50+0,2-0,9
4.
определяем
нормативную массу прутка длиной 100 мм
Мнор.=
5.
Длина
исходной заготовки для ковки
Lи.з=
Проверка: Lи.з/Ди.з=93,5/50=1,87<2,5
6.
рассчитываем
массу исходной заготовки для прутка.


Расчет массы
детали
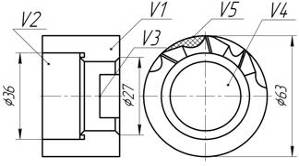
ma.=Va·ρ·10-9 (кг)
Vд = V1 –
V2 – V3 – V4 – V5
;
;
;
С=(63 – 27) / 2
= 18;

V5=SΔ·lкан=0,5·a·h·
lкан=0,5·9·10·40=1800м3
Vа=124. 626,6–18.
312,48–3. 124,8–12. 589,89–1800=88. 799,49м3
ma.=Va·ρ·10-9
=88. 799,49·8100· 10-9=0,719
кг.
7.
Определяем КИМ

2.6 Расчет
(назначение) режимов резания на 5 разнохарактерных операциях
025 Токарная
программная.
1-й
переход-рассверливание отверстия
Станок 16К20Т
Сверло
спиральное Ø22 мм
По карте 1
определяем необходимые стадии обработки. Для Ø27 мм, соотв. 7 классу
заготовки необходимо вести обработку: чистовая стадия 13…12 кв. [п. 5]
1.
Определяем глубину резания
T=2 мм
2.
Назначаем подачу
Som=0,95;
Vm=17,3; Pm=3430; Nm=1,77 [К. 47, Л.1, С 130]
Поправочный коэффициент
на подачу КSM=0,85 [1, К. 53, Л.1, С 143]
S0=0,95·0,85=0,8 мм/об.
Скорость
корректируем по формуле.
V=Vm·KVm· KV3· KVж · KVm· KVw· KVu· KVc
KVM= 0,85; KV3=1,0; KVж=1,0; KVт=1,0; KVw=1,0; KVu=1,0;
KVl=1,0.
V=17,3·0,85·1·1·1·1·1·1=14,7 м/мин
3.
Определяем
частоту вращения

4.
Значение
минимальной подачи
Sмин=S0·n=0,8·208=166,4 мм/мин
Корректируем
по паспорту станка пд=180 мин-1;
SМф=169 мм/мин; Sоф=0,8 мм/об
5.
Корректируем
табличные значения мощности резания и осевой силы.
6.
N=
KNM=KPM=0,85

7.
Nд=4кВт;η=0,81
– условие выполняется
P=4035H, Что допустимого
значения по стандарту.
8.
Основное
время
9.

L1=5; L2=5; L3=5 [1, пр-ие 23, С. 329]
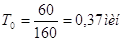
2-ой переход
– подрезание торца.
1.
Определяем
глубину резания
T=0,8 мм [1, к. 2, п. 4, с37]
2.
Назначаем подачу
Sот=0,22 мм/об [1, к. 6,
л. 1, с. 46]
3.
Определяем период стойкости резца:
Т=45 мин
[1, пр-ие 13, л. 2, с. 317]
Поправочные
коэффициенты на подачу
КSm=1; КSy=0,8; КSr=1; КSk=0,8; КS4k=1 [1, к. 8, л. 1,
с. 48–49], тогда
Sот=0,22·0,8·0,8=0,14 мм/об
4.
Определяем
скорость резания
Vm=327 м/мин [1, к. 22, с. 81]
Поправочные
коэффициенты
на скорость
KVc=1;
KV0=1; KVj=0,75; KVM=1; KVφ=1;
KVm=0,8; KVж=0,75
Vm=327·0,75·0,8·0,75·1·1·1·1=147,15 м/мин
5.
Определяем
частоту вращения

Корректируем
по паспорту станка16К20Т1 и принимаем n= 630 мин-1
6.
Определяем
действительную скорость резания

7.
Определяем
мощность резания
Nрез=5,1 [КВт] [1, к. 21,
л. 1, с. 73]
8.
Определяем мощность на шпинделе
Nшп=Nэ·η=10·0,75=[кВт] –
обработка возможна
9.
Определяем основное время
10.

Lp=l+l1+l2;
l1+l2=2 мм [1, пр=ие 22, с. 328]
Lp=45+2=47 мм
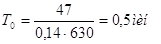
3-ий
переход-растачивание торцовой выточки.
Для растачивания
выточки по 14 кв заготовки-11…9 кв. детали выбираем получистовую стадию
обработки.
[1, к. 1, л. 2]
1.
Выбираем глубину резания
t=1 мм
2. Назначаем
подачу
Sот=0,49 мм/об. [к. 4, л. 2, с. 41]
Поправочные
коэффициенты на подачу
KSИ1=0,8; KSp1=1,05; KSд=1; KSm=0,9; KSy=1,2; KSп=1; KS4=1; KSj=0,75; KSt=0,8
Sот=0,49·0,8·1,05·1·1·0,9·1,2·1·1·1,75·0,8=0,26 мм/об
3. Определяем
скорость резания
V=66 мм/об [1, к. 30,
л. 2, с. 94]
Поправочные
коэффициенты на скорость
KVN=0,3; KVр=1,00; KVм=0,8; KVт=1,0; KVж=1,0; KVс=1,0; KVот=0,9;
V=66·0,3·1·0,8·1·1·1·0,9=14,2 мм/мин
4.
Определяем
частоту вращения

Корректируем
по паспорту станка и принимаем nд=200 мин-1
5.
Определяем
действительную скорость резания.

6.
Определяем
мощность
N=6,3 кВт
7.
Определяем
основное время
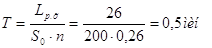
Lp.x =l+l1+l2; l1+l2=5 мм
Lp.x =21+5=26 мм
4-ый переход
– прорезать канавку
Для
прорезания канавки по 15 кВ заготовки-11…9 кв детали-выбираем получистовую
стадию обработки.
1.
Выбираем глубину резания
t=1,3 мм
2.
Назначаем
подачу
Sот=0,49 мм/об [1, к. 4,
л. 2, с. 41]
Поправочные
коэффициенты на подачу
KSH1=0,8; KSp1=1,05; KSд=1; KSh=1; KSм=0,9; KSy=1,2; KSn=1; KSφ=1; KSj=075; KSt=0,8.
Sот=0,49·0,8·1,05·1·1·0,9·1,2·1·1·0,75·0,8=0,26 мм/об
3.
Определяем
скорость резания
V=54 мм/мин
Поправочные
коэффициенты на скорость.
KVИ=0,3; KVр=1; KVм=0,8; KVт=0,8; KVж=1; KVс=1; KVот=0,9
V=54·0,3·1·0,8·0,8·1·1·0,9=9 мм/мин
4. Определяем
частоту вращения.
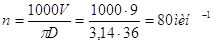
Корректируем
по паспорту станка и принимаем пд=71 мин-1
5.
Определяем действительную скорость резания.
6.

7.
Определяем
мощность
N=6,3 кВт
8.
Определяем
основное время.
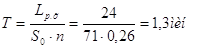
Lp.х=l+l1+l2; l1+l2=1+5=6 мм.
Lp.х=18+6=24 мм
5-ый
переход-развертывание отверстия.
Для
развертывания отверстия по 10 кВ заготовки – 7…9кВ детали выбираем чистовую
стадию обработки [1, к. 1, л. 2, стр. 122] Ø27Н7 (+0,02)
1.
Определяем глубину резания.
T=0,06 мм
2.
Назначаем
подачу.
Sот=0,97 мм/об [1, к. 53,
л. 1, с. 143]
Поправочный
коэффициент на подачу. КSM=0,85.
Sоф=0,97·0,85·1·1·1·1·1·1=7,39 м/мин.
3. Определяем
скорость резания.
VT=8,7 [1, к. 49, л. 1,
с. 134]
Поправочные
коэффициенты на скорость резания
KVм=0,85; KVЗ=1; KVж=1; KVт=1; KVw=1; KVn=1; KVl=1.
V=8,7·0,85·1·1·1·1·1·1=7,39 м/мин
4.
Определяем
частоту вращения
принимаем 
5.
Определяем минутную подачу
Sмин= S0 ·п=0,8·89=71,2 мм/мин
Корректируем
по паспорту станка и принимаем SМф=63 мм/мин.
6.

– обработка возможна
7.
Определяем основное время
[1, пр-ие 23, с. 329]
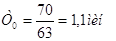
045 Фрезерная
1.
Фрезерование
стружечных канавок на цилиндрической поверхности. Фреза двухугловая Д=60 мм;
Z=20; B=20 мм; t=9 мм; SZ=0,06–0,04 [1, к. 194, с. 333];
V=33 м/мин; n=175 [1, к. 196, с. 335];
SM=173
Поправочные
коэффициенты на режимы резания
Knv= Knn= KnSM=0,6; Knv= Knn= KnSM=1; Kφv= Kφn= KφSM=1,05, при φ=450;
Kвv= Kвn= KвSM=0,8
VH=33·0,6·1·1,05·1,12·0,8=18,6 м/мин;
n=175·0,6·1·1,05·1,12·0,8=99 мин-1;
SM=173·0,6·1·1,05·1,12·0,8=97 мм/мин
Корректируем
по паспорту станка:
n=100 мин-1; SM=100 мм/мин
2.
Определяем
фактическую скорость резания.
VФ=
3.
Определяем
фактическую подачу на 1 зуб фрезы.
SZ=
Проверка
выбранных режимов по мощности.
4.
Мощность,
потребляемая на резание, составляем 1,2 кВт [2, к. 197, с. 337]
5.
Найденное
значение мощности провнряется по мощности электродвигателя с учетом К.П.Д
станка.
При Nд=7,5 кВт и К.П.Д станка η=0,8,
мощность на шпинделе Nэ будет.
Nэ=
Nд·η=7,5·0,8=6
кВт, т.е. больше мощности, потребной на резание =>установленный режим
резания по мощности осуществим.
6.
Определяем
основное время.
t=
Lp/Sm*i
Lp.=l+l1+l2; l1=25 мм [3, пр-ие 4, л. 5,
с. 373]
L2=0 мм
Lp.=40+25=65 мм; i=Z=8
t0=65*8/100=5,2 мин
060.
Внутришлифовальная.
Внутришлифовальный
станок 3К228В. Шлифование с продольной подачей. L=40 мм; Ra0,63.
1.
Определяем
скорость главного движения резания шлифовального круга.
VK=30–35 м/сек [1, с. 301,
т. 55]
По паспортным
данным станка 3К228В диаметр нового круга Дк=0,9 (Дотв)=0,9·27=24,3 мм;
Пк=13.000 мин-1
VK=3,14*24,3*13000/1000*60=16,5 м/сек,
принимаем VK =17 м/сек
2.
Скорость движения окружной подачи.
Vд=20–40 м/мин [1, т. 55, с 301]
Принимаем Vд=30 м/мин
3.
Определяем
частоту вращения заготовки
Пд=1000*Vd/πD=1000*30/3,14*27=354 мин
– 1
4.
Поперечная
подача круга.
St=0,0025–0,01 мм/ход,
принимаем St=0,006 мм/ход.
5.
Продольная
подача на оборот заготовки.
S0= Sд·ВК (мм/об); Sд=(0,25–0,4) В [1, т. 55, с. 301]
Принимаем Sд=0,3; В=32 мм [2, т. 6]
S0=0,3·32=9,6 мм/об
6.
Скорость движения продольной подачи
Sпрод.=Sa*
πD/1000=9,6*354/1000=3,4 м/мин
7.
Определяем
мощность, затрачиваемую на резание.
N=CN·V3r·tx·Sy·dq
CN=0,36;
r=0,35; x=0,4; y=0,4; q=0,3 [1, т. 56]
N=0,36·300,35·0,0060,4·9,60,4·270,3=1,0
кВт.
По паспорту
станка мощность двигателя шлифовального круга Nд= 5,5 кВт
8.
Проверяем,
достаточна ли мощность двигателя шлифовальной бабки.
Nшп= NМ·η=5,5·0,85=4,6
кВт
Nрез< Nшп
1,0<4,6, т.е.
обработка возможна
9.
Основное
время.
Т0=(L/ πd*S0*St)
* K
При перебеге
круга на каждую сторону, равную 0,5 Вк=0,5·17=8,5 мм, L=l=B3=40 мм.
Т0=0,68 мин
065 Заточная.
Форма круга Т
Материал монокорунд
431
Зернистость-16–12
Твердость-СМ3-С1
Связка
керамическая К5
Скорость
круга VK-20÷25 м/сек
Подача
продольная Sпр=2÷3 м/мин
Подача на
глубину St=0,02–0,04 мм/дв. ход.
Диаметр
заточного круга – 125 мм
Ширина круга,
Вк=15 мм
1.
Частота
вращения шлифовальногго круга
n=1000V/
πD=3057 мин-1
2.
Основное время.
Т0=2
(l+l1+l2)/Sпр*1000 * K* z (мин)
l1=42,12 мин; l2=3÷5, l2=4 мм.
h=0,5 мм; К=1,2–1,5
Т0=13,7 мин
2.7
Расчет
норм времени
025 Токарная
программная.
1.
Определяем
общее основное время
Т0общ=0,375+0,5+0,5+0,325+1,1=2,8 мин
2.
Определяем
вспомогательное время.
2.1
Вспомогательное
время на установку и снятие детали
tв1=0,32 мин [к. 6,
л. 1, с. 57]
2.2
Вспомогательное время, связанное с операцией
tв2=0,32+0,04+0,31+0,15+0,19+0,03=1,04 мин
[к. 14, с. 79]
2.3
Вспомогательное время на контрольные измерения.
tв=0,10 [к. 15, п. 147,
л. 5, с. 84]
tв=0,13 [к. 15, п. 184,
л. 7, с. 86]
tв=0,24 [к. 15, п. 228,
л. 8, с. 87]
tв=0,11 [к. 15, п. 16,
л. 2, с. 81]
tв0=0,10+0,13+0,24+0,11=0,58 мин
Определяем
общее вспомогательное время.
tв.общ=0,32+1,04+0,58=1,94 мин.
3.
Определяем
оперативное время.
Топ.= t0+ tв=2,8+1,94=4,74 мин
4.
Время
на обслуживание рабочего места составляет 8% от оперативного времени.
Тобс.=0,08·4,74=0,379 мин
[к. 16, с. 90]
5.
Время
перерывов на отдых и личные потребности в условиях многостаночного обслуживания
равно 2,0% от Топ.[к. 18, с. 93]
tотл=0,02·4,74=0,0948 мин.
6.
Норма штучного времени.
Тшт.=
tоп+ tобс+ tотл=4,74+0,379+0,0948=5,2 мин
7.
Подготовительно-заключительное
время.
Тп.з=4 мин;
Тп.з=9 мин; Тп.з=2,5 мин; Тп.з=0,2 мин;
Тп.з=1 мин; Тп.з=1 мин; Тп.з=1,5 мин;
Тп.з=0,4 мин; Тп.з=5 мин; Тп.з=2 мин.
Тп.з=4+9+2,5+0,2+1+1+1,5+0,4+5+2=27,6 мин
8.
Штучно-калькуляционное
время.
Тш-к=
Тшт+Тпз/ π=5,476 мин
045 Фрезерная
1.
Т0=5,2 мин
2.
Определяем
вспомогательное время.
2.1
Время
на установку и снятие детали
tв1=0,37 мин [к. 7, п. 8, с. 40]
2.2
время, связанное с переходом
tв2=0,18 мин
tв2=0,04·8=0,32 мин
tв2=0,18 мин [к. 31, п. 2,
с. 108]
tв.общ=0,18+0,32+0,18=0,68 мин
2.3
время
на контрольное измерение
tв4=0,23 мин [к. 86, л. 1,
с. 185]
Определяем
общее вспомогательное время
tв.общ=0,37+0,68+0,23=1,28 мин
3.
Опрееляем
оперативное время.
Топ.= t0+ tв=5,2+1,28=6,48 мин.
4.
Время
на обслуживание рабочего места составляет 3,5% от Топ. [к. 32, с. 109]
tобс=0,035·6,48=0,2268 мин
5.
Время
перерывов на отдых и личные потребности составляет 4% от Топ.
tотл=0,04·6,48=0,2592 мин.
6.
Норма
штучного времени
Тшт= tоп+ tобс+ tотл=6,48+0,2268+0,2592=6,96 мин
7.
Тп.з
tп.з=22 мин [к. 32, п. 5, с. 110]
tп.з=7 мин [к. 32, п. 24]
Тп.з=22+7=29 мин
8.
Тш-к
Тш-к=
Тшт+ Тпз/ π=7,25 мин
060
Внутришлифовальная
1.
Т0=0,68 мин
2.
Определяем
вспомогательное время.
2.1
время
на установку и снятие детали.
tв1=0,25 мин [3, к. 47, п. 2, с. 132]
2.2
время, связанное с переходом.
tв2=1,5 мин [3, к. 47, п. 19, с. 132]
tв2=0,22 мин [3, к. 86, п. 75, с. 188]
Определяем
общее вспомогательное время.
tв.общ=0,25+1,5+0,22=1,97 мин
3.
Определяем
оперативное время.
То.п=0,68+1,97=2,65 мин.
4. Время на
обслуживание рабочего места составляет 4% от Топ
tобс=0,04·2,65=0,106 мин.
5. Норма
штучного времени.
Тшт.=0,1061+0,106+2,65=2,86 мин
6. Тп.з
tп.з=12 мин [3, к. 46,
с. 131, п. 1]
tп.з=7,0 мин [3, к. 46,
с. 131, п. 8]
Тп.з=19 мин
7. Тш-к
Тш-к=2,86+19/100=3,05 мин
065 Заточная
1.
Т0=13,7 мин.
2.
Определяем вспомогательное время.
2.1
время
на установку и снятие детали
tв1=0,26 мин [к. 7, п. 1,
с. 40]
2.2
время, связанное с переходом
tв2=0,65 мин [к. 82, п. 2]
2.3
время на контрольные измерения.
tв3=0,26 мин [к. 86, л. 1,
с. 185]
Определяем
общее вспомогательное время
tв.общ=0,26+0,65+0,26=1,17 мин
3.
Определяем
оперативне время.
Топ.=13,7+1,17=14,87 мин.
4. время на
обслуживание рабочего места составляет 10% от Топ.
tобс.=14,87·0,1=1,48 мин.
время
перерывов на отдых и личные потребности составляет 4% от Топ
tотл=0,04·14,87=0,59 мин
6. Норма
штучного времени
Тшт=14,87+1,48+0,59=16,94 мин.
7. Тп.з
Тп.з=27 мин
8. Тш-к
Тш-к=16,94+27/100=17,21 мин
3. Конструкторский раздел
3.1
Описание и расчет измерительного инструмента
Измерительные
инструменты, применяемые для промежуточного контроля заготовка и окончательного
контроля детали (изделия), в
зависимости
от типа производства могут быть как стандартными, так и специальными. Для одной
из операций проектируемого технологического процесса необходимо сконструировать
измерительный инструмент, прибор или контрольное приспособление. Использование
для контроля специальных калибров, сложных приборов и приспособлений должно
способствовать повышению производительности труда, создавать условия для
улучшения качества продукции и снижения ее себестоимости.
В качестве
проектируемого измерительного инструмента могут быть выбраны гладкие и
резьбовые предельные калибры, шлицевые калибры, конусные калибры,
пространственные калибры для проверки межосевого расстояния и др.
В данном
случае проектируются пробка проходная и пробка непроходная для контроля
посадочного отверстия фрезы диаметром Ø27Н7 (+0,02).
1.
Определяем
азмеры калибр-пробок для отверстия диаметром Д=27 мм с полем допуска Н7.
По ГОСТ 25347–82 находим предельные отклонения отверстия; они равны +21 мкм и
0. Следовательно,
Дmax=27,021 мм;
Дmin=27,000 мм.
По ГОСТ 24853–81
находим допуски и предельные отклонения калибров для IТ7:
Н=0,004;
у=0,003, Z=0,003.
Наибольший
размер новой проходной калибр-пробки.
ПРmax=Dmin+Z+H\2=27,000+0,003=0,002=27,005 мм.
Размер
калибра ПР, проставляемый на чертеже, при допуске на изготовление Н=0,004 мм
равен 27,005–0,004
Исполнительные
размеры:
– наибольший
27,005 мм
– наименьший
27,001 мм
Наименьший
размер изношенной проходной калибр пробки рпи допуске на износ у=0,003 мкм
равен
ПРизн.=Dmin-y=27,001–0,003=26,998 мм
Наибольший
размер новой непроходной калибр-пробки.
НЕmax=Dmax+H/2=27,021+0,002=27,023 мм
Размер
калибра НЕ, проставляемый на чертеже, равен 27,023-0,004
Исполнительные
размеры:
– наибольший
27,023 мм
– наименьший
27,019 мм
3.2 Описание
и расчет приспособления
Рассчитать и
сконструировать приспособление для фрезерования торцового шпоночного паза.
Расчет
приспособления ведем на точность и усилие зажима.
I Расчет приспособления на
точность.
Правильно
выбрать степень точности изготовления деталей можно только при точном учете
всех возникающих в процессе производства погрешностей.
Сумма всех
погрешностей определяется из выражения:
∑ ε=К·
εбаз+ εуст+ εобр-ки+[ε]присп-ия;
[], где К=0,8÷0,85 – коэффициент уменьшения погрешности базирования;
εбаз-погрешность
базирования при выполнении данной операции;
εуст
– погрешность установки, возникающая под действием зажимных сил резания;
εобр-погрешность
обработки детали на данной операции;
[ε]присп-ия
– погрешность допустимая для данного приспособления и вызываемая неточностью
его изготовления.
εобр=К'·ω,
где К'=0,6÷0,8
ω – табличное значение
средней экономической точности []
Фрезерование
проводим по 11 квалитуту. Ширина шпоночного паза 12=0,11
εобр=0,8·0,11=0,088 мм
εбаз=0
[
εуст=0,09 мм[
[ε]присп-ия=0,
для новог приспособления
∑ ε=0,85·0+0,009+0,088=0,178 мм
Если допуск
на размер детали ТО=0,43, а сумма всех погрешностей ∑ ε=0,178 мм,
то необходимо, чтобы соблюдалось условие:
∑ ε≤Td (TD)
0,178≤0,43
(по 14 кв.) – условие выполнено
II Расчет зажимного усилия.
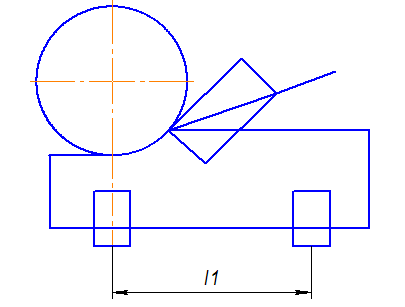
W=
KF/ff=0,1÷0,15
F=Rl/l1=l2
Rl-F(l1+l2)=0;
Rl-F1l1-F2l2=0
Сил резания.
Главная составляющая силы резания при фрезеровании-окружная сила Н.
Где Sz=0,5–1,2 мм/об[
Ср=68,2;
х=0,86; у=0,72; q=0,86; W=0 [
Для дисковой
трехсторонней резы по ГОСТ 3755–78 D=63 мм; В=12 мм; d=22 мм; Z=16 [
Кмр=
Кмр=
К=К0·
К1 ·К2· К3· К4 ·К5=1,5·1·1,9·1,2·1·1=3,42
К0=1,5;
К1 =1; К2=1,9; К3=1,2; К4 =1К5=1
W=395,581 H
Заключение
Выполненная
работа носила обучающий характер на заключительном этапе обучения в колледже.
В результате
закреплены и получены новые знания по следующим направлениям:
1. Оптимальному
выбору заготовки;
2.
Последовательное
освоение этапов проектирования технологического процесса: составлены операции,
переходы, выбраны современные металлорежущие станки и технологическая оснастка,
проведен расчет режимов резания и нормирования;
3.
Освоены
этапы проектирования измерительного инструмента.
Список
используемой литературы
1. Справочник технолога-машиностроителя.
В 2-х томах. Том 2. Под редакцией А.Г Касиловой и Р.К Мещерякова – 4-е издание,
перераб. И доп. – М. Машиностроение, 1985,496 с., ИЛ;
2. Общемашиностроительные нормативы
времени и режимов резания для нормирования работ, выполняемых на универсальных
и многоцелевых станках с числовым программным управлением. Часть II Нормативы режимов
резания;
3. Общемашиностроительные нормативы
времени и режимов резания для нормирования работ, выполняемых на универсальных
и многоцелевых станках с числовым программным управлением. Часть I. Нормативы времени.
4. Нефедов Н.А
Дипломное проектирование в машиностроительных техникумах: Учеб. Пособие для
техникумов. 2-е изд., перераб. И доп. – М. Высш. шк., 1986 г. - 239 с.,
ил.;
5. Полей М.М. Технология
производства металлорежущих инструментов – 2-е изд., перераб. И доп. – М.:
Машиностроение, 1982. – 256 с., ил;
6. 6 Барсов А.И
Технология инструментального производства. М., «Машиностроение», 1975. 272 с.
с ил.
7. М.М Палей Технология
производства режущего инструмента.
8. Каталог – справочник
«Металлорежущий инструмент» Часть 1. Резцы.
|