Курсовая работа: Безопасность технологического процесса производства асфальтового бетона
Курсовая работа: Безопасность технологического процесса производства асфальтового бетона
Федеральное
агентство по образованию Российской Федерации
Белгородский
государственный технологический университет
им. В. Г.
Шухова
Губкинский
филиал
Курсовой
проект
по
дисциплине: "Безопасность технологических процессов и производств"
на тему: "Безопасность
технологического процесса производства асфальтового бетона"
Выполнил:
Захаров Максим
Александрович
группа: БЖ-31
Проверила:
Черных Ольга
Александровна
Губкин, 2008
Содержание
Введение
1. Общие сведения асфальтовых
бетонов
1.1. Классификация
асфальтовых бетонов
1.2. Разновидности
асфальтовых бетонов
1.3. Составляющие
материалы асфальтового бетона
2. Технология
производства асфальтового бетона
2.1. Общие сведения
3. Анализ вредных и опасных
производственных факторов
3.1. Общие положения
3.2. Требования
безопасности к производственному оборудованию при
производстве асфальтового
бетона
3.3. Техника безопасности
при эксплуатации машин и оборудования
4. Расчет
основных параметров оборудования при производстве
асфальтового
бетона
4.1. Расчет
ширины уступа площадок карьера
4.2. Расчет основных
размеров параметров работы экскаваторов
4.3. Расчет
основных параметров конвейера
4.4. Выбор и расчет
дробильно-помольного оборудования с учетом
требований
производственной безопасности
4.5. Машины для тонкого
измельчения (помола) материала
Заключение
Список литературы
Введение
В настоящее время стоит
вопрос о строительстве более усовершенствованных дорог с асфальтобетонным
покрытием, отвечающие всем требованиям по долговечности, ровности,
шероховатости (коэффициенту сцепления). Для реализации этой цели необходим
подробный и более детальный анализ технологического процесса производства
асфальтобетонной смеси производства такого покрытия требуется приготовление
асфальтобетонной смеси.
Производство
асфальтобетонной смеси - это один из самых энергоемких процессов дорожного
строительства. От состояния всего парка машин и оборудования зависит расход
топлива - энергетических ресурсов.
Асфальтовый бетон
(асфальтобетон) - искусственный строительный материал, получаемый в результате
затвердевания уплотненной смеси минеральных заполнителей (щебня, песка,
тонкоизмельченного минерального порошка) с органическим вяжущим (битумом или
дегтем). Асфальтобетон без крупного заполнителя (щебня) называют песчаным
асфальтом или асфальтовым раствором.
Асфальтовые бетоны
значительно более стойки к коррозионным воздействиям, чем цементные, но боятся
воздействий жидких топлив и масел. Износостойкость асфальтовых бетонов выше,
чем цементных.
Наиболее широкое
применение асфальтовый бетон находит в строительстве при возведении магистральных, городских,
аэродромных, дорожных, кровельных и других покрытий, гидротехнических,
мостовых, промышленных, жилищно-гражданских и иных зданий и сооружений.
Для повышения качества
дорог необходимо производить качественную и эффективную асфальтобетонную смесь,
а для этого необходимы АБЗ с новейшей технологией и применением местных
ресурсов.
1. Общие сведения об
асфальтовом бетоне
1.1. Классификация
асфальтовых бетонов
Асфальтобетон
1) По показателю
бывает:
- холодный;
- горячий;
2) По виду минеральной
составляющей (заполнителя):
- щебёночный;
- гравийный;
- песчаный;
3) По вязкости применяемого
битума:
- горячий а\б - вязкие и
жидкие;
- холодный а\б - жидкие;
4) По остаточной
пористости
- горячие а\б делятся:
а) высокоплотные - от 1
до 2.5%
б) плотные - свыше 2.5 до
5%
в) пористые - свыше 5 до
10%
г) высокопористые - свыше
10 до 18%
- холодные а\б - свыше 6
до 10%
5) По содержанию
щебня:
- горячий а\б:
а) А-свыше 50 до 60%
б) Б-свыше 40 до 50%
в) В-свыше 30 до 40%
- холодный а\б:
а) Бх-свыше 40 до 50%
б) Вх-свыше 30 до 40%
6) По
производственному назначению;
7) По технологическим
признакам асфальтобетонной смеси в процессе укладки.
К основным
классификационным признакам асфальтобетонов относятся разновидность крупного
заполнителя, вязкость битумов, размеры зерен щебня или гравия, структурные
параметры, производственное назначение.
В зависимости от вида
крупного заполнителя асфальтобетоны разделяют на:
- щебеночные, состоящие
из щебня, песка, мин. порошка и битума;
- гравийные, состоящие из
гравия, песка, мин. порошка и битума;
- песчаные —отсутствует
крупный заполнитель (щебень или гравий).
По вязкости применяемого
битума и по температуре укладки асфальтобетонной массы в конструктивный слой
они подразделяются на:
- горячие укладываемые
при температуре не ниже 120°С;
- теплые укладываемые при
температуре не ниже 70°С;
- холодные укладываемые
при температуре не ниже 5°С.
Кроме того, горячие и
теплые асфальтобетоны в зависимости от использования их в дорожной конструкции
разделяют на:
- плотные — для верхних
слоев покрытия дорог с остаточной
пористостью от 2 до 7%;
- пористые — для нижнего
слоя и оснований дорожных покрытий, с
остаточной пористостью от
7 до 12% по массе;
- высокопористые — с
пористостью 12 ... 18%.
Плотные дорожные
асфальтобетоны (горячие и холодные) в зависимости от количественного содержания
в них крупного или мелкого заполнителя подразделяют на пять типов: А, Б, В, Г,
Д. Так, например, тип А содержит 50 ... 65% щебня; тип Б — 35 ... 50% щебня или
гравия; тип В — 20 ... 35% щебня или гравия.
Кроме того, плотные
горячие и теплые асфальтобетоны подразделяют на три марки — I, II, III в
зависимости от качественных показателей.
По производственному
назначению различают асфальтобетоны:
дорожные, аэродромные,
гидротехнические, для плоской кровли и полов.
По технологическим
признакам асфальтобетонной массы в процессе ее укладки и уплотнения
асфальтобетоны и растворы разделяют на:
-жесткие;
-пластичные;
-литые.
Для уплотнения жестких и
пластичных масс применяют тяжелые и средние катки. Литую асфальтобетонную массу
часто уплотняют специальными валками, легким катком или вовсе не уплотняют
1.2. Разновидности
асфальтовых бетонов
К разновидностям асфальтобетона
относятся теплый, холодный, литой, цветной. Более редким в строительстве
является дегтебетон.
Теплый асфальтобетон используют для устройства нижних
слоев в пoкрытиях.
Для приготовления теплого
асфальтобетона используют вязкие нефтебитумы марок БНД 200/300 и БНД 130/200
или жидкие битумы; теще более тоньше измельченный, чем в горячих смесях известняковый
порошок; щебень, искусственный песок, прочные шлаки. Температура готовой теплой
массы при ее выходе из смесителя должна быть 90—130°С. Допустимые пределы
температур массы при ее уплотнении в покрытии: нижний — 50°С при работах в
теплую погоду и при марке битума СГ 70/130; верхний — 100°С при работах в
холодную погоду и при марке битума СГ 130/200. Уплотнение производят легкими и
тяжелыми (12 т) катками; при холодной погоде рекомендуется уплотнять массу
сразу же после ее укладки в покрытие, чтобы не остудить массу и не потерять ее
удобообрабатываемость. Толщину рыхлого слоя назначают на 15—20% больше
проектной толщины и покрытия, что регулируется положением выглаживающей плиты
укладчика.
Холодный асфальтобетон содержит жидкий или разжиженный вязкий битум, что
позволяет укладывать массу холодного асфальта при температуре окружающего
воздуха.
Приготовление холодного
асфальта осуществляется в горячем и холодном состояниях. При приготовлении
массы в горячем состоянии применяют жидкий или разжиженный битум, в холодном —
битумную эмульсию. Холодный асфальт применяют для создания верхних слоев
дорожных покрытий и при производстве ремонтных работ.
Если холодный асфальт
употребляется в строительных работах после его изготовления на АБЗ, то укладку
массы производят еще в теплом состоянии. В этом случае слой массы ложится
компактнее, а при его уплотнении быстрее формируется монолитное покрытие.
При работах во влажную
погоду используют холодный асфальт, приготовленный на битумной эмульсии.
В первый период
эксплуатации дорожного покрытия рекомендуется не допускать высокой
грузонапряженности при движении автотранспорта, так же как нельзя допускать и
слишком слабой интенсивности движения транспорта, поскольку окончательное
формирование покрытия происходит именно под действием этого движения.
Холодный асфальт
приготовляют с применением щебня из морозостойких карбонатных пород
(известняков, доломитов) и доменных шлаков с пределом прочности при сжатии не
менее 80 МПа.
Чтобы покрытие не
становилось скользким при его эксплуатации, к известняковому щебню добавляют до
30% мелкого (8—10 мм) гранитного, базальтового щебня или искусственного
дробленого песка из тех же пород камня. Песок должен быть чистым, однородным, без
органических примесей или глинистых частиц.
Для повышения вязкости и
клеящей способности разжиженного или жидкого битума в состав холодного асфальта
добавляют минеральный (известняковый) порошок.
Холодный асфальт может
длительное время оставаться в рыхлом состоянии в складских условиях (до 8—10
месяцев). Поэтому холодную асфальтобетонную массу обычно приготовляют в зимнее
время года с тем, чтобы ее раскладку в покрытие произвести с наступлением
весны. Зимняя заготовка массы позволяет работать АБЗ практически в течение
полного года. При чрезмерно длительном хранении рыхлая масса холодного асфальта
постепенно слеживается, образуются глыбы, в этом случае требуется
предварительное ее рыхление, добавляя на последней стадии перемешивания массы,
хлорное железо и другие специальные вещества (добавки) до 2—3%, чтобы уменьшить
слеживание при длительном хранении. Однако, нужно помнить, что механическое
рыхление ухудшает качество массы вследствие обнажения отдельных частиц,
покрытых пленкой битума.
При тонких пленках битума
слеживаемость массы меньше и прочность плотного покрытия выше. При выборе
вяжущего учитывают, что чем холоднее погодные условия, длительнее срок хранения
массы, ниже прочность камня, тем вяжущее вещество должно быть более жидким.
Доля вяжущего вещества в
составе холодного асфальта устанавливается проектированием оптимального
состава, но обычно находится в пределах 6—8% для песчаного и 5—7% для
мелкозернистого. Качество холодного асфальта в покрытиях характеризуется его
прочностью при сжатии в сухом и водонасыщенном состояниях при 20°С
соответственно 1,5—2,0 и 1,0—1,5 МПа, коэффициентом водоустойчивости не менее
0,6—0,8 и некоторыми другими, показателями свойств. В целом следует отметить,
что эта разновидность асфальтового бетона применяется в ограниченных размерах,
но покрытия из него перспективные.
Литой асфальтовый
бетон выделяется из
других горячих аналогов тем,
что все межзерновые поры
в нем заполнены асфальтовым вяжущим веществом. После укладки массы и ее
уплотнения в монолите практически отсутствуют остаточные поры и пустоты,
поэтому покрытия из него водонепроницаемые.
Преимущество литого
асфальта состоит в том, что работы по его укладке можно производить при
сравнительно низких температурах (до -10°С) воздуха. Не требуется продолжительного
уплотнения массы катками или тромбования при ямочном ремонте. Достаточно
прикатать его легкими (0,5—1,5 т) катками. Преимуществом покрытий из литого
асфальта является также их высокая долговечность, износостойкость и
шероховатость.
Литой асфальтобетон не
лишен и некоторых недостатков: к деформациям при высоких температурах воздуха и
к образованию трещин в период низких температур воздуха. В последние годы эти недостатки
были резко ослаблены. В получаемых составах литого асфальта содержится
минеральных частиц крупнее 5 мм 50—55%, асфальтовяжущего вещества 20—25%. Слой
уложенной массы не требует дополнительного уплотнения. С понижением температуры
покрытия с 200°С до атмосферной литой асфальт в покрытии отвердевает и пригоден
к эксплуатации.
Достоинства покрытий из
вибролитых смесей отмечены при их укладке на дорогах высоких категорий, мостах,
эстакадах и взлетно-посадочных полосах аэродромов. По технологии вибролитья
используют подогретые зернистые минеральные материалы температурой 280—300°С,
если порошок поступает холодным; температуру нагрева их снижают на 12—14%, если
порошок в мешалку подается подогретым до температуры 120—140°С. Битум
подогревают до температуры 150—170°С. Температура смеси должна быть 190—200°С,
если температура воздуха выше -10°С; не ниже 220°С, если температура воздуха
+10—15°С. Технические свойства смеси и асфальтобетона: пористость минеральной
смеси не более 20%, подвижность смеси при 200°С — не менее 25 мм (определяют с
помощью металлического конуса); водонасыщение уплотненных образцов — 1,0% от
объема; глубина вдавливания штампа в образцы при температуре 40°С — не более 4
мм.
Цветной асфальтовый
бетон состоит из
мелкого щебня (5—7 мм), песка, минерального порошка, связующего, пластификатора
и пигмента. В качестве вяжущего вещества в нем выступает структурный элемент из
связующего и минерального порошка с добавлениями пластификатора и пигмента. В
качестве щебня применяют измельченные отходы белого мрамора и известняка. Песок
должен быть чистым и светлым, а минеральный порошок — из тонко измельченного
белого мрамора. Связующим в цветном асфальте обычно служат полимеры,
полиэтилен, поливинилхлорид, и др. Из пигментов более цветостойкими являются
железный сурик, крон желтый, оксид хрома.
Цветной асфальтобетон
применяют для оформления площадей скверов, остановок городского транспорта,
пешеходных переходов и других объектов города.
1.3. Составляющие
материалы асфальтового бетона.
При изготовлении
асфальтобетонной массы используют щебень, гравий, песок, минеральный порошок и
битум.
Щебень применяют из
изверженных и метаморфических горных пород с пределом прочности при сжатии не
менее 100,0-120,0 МПа или пород осадочного происхождения с пределом прочности
не менее 60,0-80,0 МПа (в водонасыщенном состоянии); для дробления горных пород
на щебень чаще всего используют граниты, диабазы, базальты, известняки и
доломиты, а также прочные доменные шлаки. Щебень или гравий должны быть
чистыми, разделенными по фракциям 20...40, 10... 20 и 5... 10 мм с
морозостойкостью не менее Мрз25; в мягких климатических условиях — не менее
Мрз15.
Песок природного
происхождения или полученный в результате дробления горных пород с прочностью
не ниже прочности щебня. Природные пески должны быть разнозернистые, чистые с
модулем крупности более 2,0 и содержанием пылевато-глинистых частиц не более 3%
(по массе).
Минеральный порошок
изготовляют путем измельчения известняков и доломитов с пределом прочности при
сжатии не менее 20,0 МПа, а также доменных шлаков или асфальтовых пород. По
степени измельчения необходимо, чтобы порошок проходил (при мокром рассеве)
через сито с отверстиями 1,25 мм, содержание же частиц мельче 0,071 мм было не
менее 70% по массе, а частиц мельче 0,315 мм — не менее 90%.
Битумы бывают природные и
нефтяные. Природные являются продуктом естественного видоизменения нефти. Они
встречаются иногда в чистом виде, образуя озера, в виде твердых скоплений –
асфальтитов, но чаще пропитывают горные породы – известняки, доломиты,
песчаники. Содержание битрумав них 10-80%. Из этих пород битум получают путем
экстрагирования с помощью различных растворителей.
В основном применяют
нефтяные битумы. Их стоимость в 5-6 раз ниже природных.
По способу получения
нефтяные битумы делят на:
- остаточные (остаток
после отгонки из нефти бензина, керосина и части масел);
- окисление (нефтяные
остатки окисляют кислородом воздуха в конвекторах периодического или
непрерывного действия или в трубчатых реакторах, называемые окислительными
колонками;.
Кроме указанных
компонентов в процессе приготовления асфальтобетонной массы иногда добавляют ПАВ,
улучшающие качество готового асфальтобетона. Эти вещества позволяют удлинить
сроки строительного сезона, облегчить технологические операции и увеличить
долговечность материала.
2. Технология
производства асфальтового бетона
2.1. Общие сведения
Производство
асфальтобетонной массы осуществляется на специальных заводах: стационарных и
временных. Стационарный асфальтобетонный завод (АБЗ) выпускает массу в больших
количествах и предназначен для строительства асфальтобетонных покрытий на
крупных строительных объектах, работы на которых выполняют в течение нескольких
лет, например АБЗ для строительства городских дорожных покрытий. Временные АБЗ
предназначены для обслуживания асфальтобетонной массой небольших объектов или
крупных, но сильно растянутых в одном направлении, — магистральных
автомобильных дорог и др.
Заводы по производству
асфальтобетонной массы относятся к высокомеханизированным предприятиям. На
современных заводах достигнута полная механизация и автоматизация основных
технологических операций. В состав завода входят: смесительный цех, машины и
оборудование которого предназначены для приготовления асфальтобетонной массы,
дробильно-сортировочный цех для изготовления щебня, помольный цех для изготовления
минерального порошка, цех битумного хозяйства, энергосиловое и паросиловое
отделения, складское хозяйство, ремонтно-механические мастерские и лаборатория
при отделе технического контроля качества.
Известно, что одним из
важнейших компонентов асфальтобетонной смеси является минеральный порошок, без
которого невозможно получить асфальтобетон, отвечающий требованиям ГОСТа. Для
получения минерального порошка используется часть песчаной фракции минерального
состава асфальтобетонной смеси, предварительно прошедшей через сушильный барабан,
затем измельченной в мельнице, и поданной через накопительный бункер в
смеситель.
На листе 1 показана
технологическая схема производства асфальтобетонной смеси. Основная операция
технологии — смешение исходных и подготовленных материалов, принимаемых в
определенных количествах по проектному составу. Температура выпускаемой из
смесительного аппарата массы 150—180°С или ниже у теплых и холодных масс. Иногда
в состав асфальтобетонной массы одновременно с битумом вводят
поверхностно-активную добавку, дозируемую с помощью специального дозатора.
Наиболее часто используют
лопастные смесители. Быстрое перемешивание в смесителях этого типа достигается
при турбулентно-вращательном движении массы за счет повышенной частоты вращения
валов лопастей мешалки — до 200 об/мин. Облегчает и ускоряет перемешивание песчаной
асфальтобетонной массы предварительное активирование минерального порошка или
введение активных добавок в смеситель в период перемешивания. При производстве
асфальтобетонной смеси используют ковшовые конвейеры (данный конвейер указан на
листе 2). Их применяют для подъема материалов по вертикали на высоту до 50 м.
На бесконечной цепи установленной на двух звездочках, ведущей и ведомой, или
бесконечной ленте, установленной на двух барабанах, закрепляют рабочие органы –
ковши. На таких элеваторах можно транспортировать как сыпучие, так и кусковые
материалы. Сыпучие и мелкокусковые материалы загружают предварительно в
загрузочный башмак, из которого его забирают ковши. Крупнокусковые материалы
необходимо подавать непосредственно в ковши.
Элеваторы бывают
быстроходные (со скоростью тягового органа 1,25-2,0 м/с) и тихоходные (со
скоростью 0,4 – 1.0 м/с).
В этих элеваторах
используют ковши с цилиндрическими днищами (указан на листе 2 рис. б ) и
остроугольные с бортовыми направляющими.
Ковши с цилиндрическими
днищами для транспортирования сухих материалов (земли, песка, мелкого каменного
угля) и мелкими для транспортирования плохо высыпающихся материалов (влажного
песка, молотого гипса, извести, цемента).
Остроугольные ковши с
бортовыми направляющими применяют для транспортирования абразивных и кусковых
насыпных материалов.
Чтобы не остудить
асфальтобетонную массу в пути следования к месту ее укладки, кузов
автомобиля-самосвала рекомендуется покрывать брезентом, деревянными щитами и
др.
Укладывают горячую массу
механическими укладчиками. Чем выше температура воздуха и лучше участок защищен
от ветра, тем больше длина укладываемой полосы. Так, например, при температуре
более +25°С и хорошей защите от ветра длина полос составляет 100—200 м, при
+5—10°С она составляет 25—60 м. Самый распространенный способ уплотнения
горячей массы при больших масштабах строительства дорожных покрытий — укатка
катками (статического действия, вибрационными, пневмоколесными), а в помещениях
— площадочными вибраторами. Первичное уплотнение уложенного слоя производится
трамбующим брусом асфальтоукладчика. Монолитный асфальтобетон в покрытии должен
удовлетворять определенным техническим требованиям.
Реальные свойства
асфальтобетона не остаются постоянными, так как внешние условия могут быстро
изменяться, а вместе с ними должны изменяться и свойства покрытия из
асфальтового бетона. При обычной температуре (20—25°С) четко проявляются
упруго- и эластичновязкие его свойства, при повышенных температурах —
вязкопластические, а при пониженных, отрицательных температурах асфальтобетон
становится упругохрупким телом. Но он чувствительно реагирует не только на
колебания температуры (t°), но также
на изменение скорости (v) приложения механических усилий (нагрузки) или
скорости деформирования. Чем выше значения v, тем при более высоких
напряжениях разрушается асфальтобетон.
В производственных
работах обычно механическую прочность асфальтобетона характеризуют пределом
прочности при сжатии стандартных образцов, испытанных при заданных температуре
и скорости приложения нагрузки. При одноосном сжатии предел прочности
асфальтобетона определяют на цилиндрических образцах, размерами(диаметр и
высота) 50,5×50,5 или 71,4×71,4 мм (в зависимости от крупности
минерального заполнителя). Испытания проводят при температурах 20, 50°С и
скорости приложения нагрузки, равной 3 мм/мин.
При температуре 20°С
предел прочности при сжатии асфальтобетона составляет около 2,5 МПа, а при
растяжении — в 6—8 раз меньше. С понижением температуры предел прочности при
сжатии возрастает (до 15—20 МПа при -15°С), а с повышением — снижается (до
1,0—1,2 МПа при +50°С).
Из других технических
характеристик следует отметить износостойкость и водостойкость. Износостойкость
определяют по потере массы образцов, испытываемых на кругах истирания или в
барабанах (с определением износа). Горячий асфальтобетон в дорожных покрытиях
изнашивается в пределах 0,2—1,5 мм в год. Водостойкость характеризуют величиной
набухания и коэффициентом водостойкости, равным отношению пределов прочности
при сжатии образцов в водонасыщенном и сухом состояниях при температуре 20°С.
Он должен быть в пределах 0,6—0,9; величина набухания в воде не более 0,5% (по
объему).
3. Анализ вредных и
опасных производственных факторов
3.1. Общие положения
Организация и технология
работ при производстве асфальтового бетона должны обеспечивать безопасность для
работающих на всех стадиях производственного процесса и соответствовать
требованиям настоящего стандарта, ГОСТ 12.3.002-75, ГОСТ12.1.004.91, СНиП III-4-80, правил пожарной безопасности.
При выполнении работ по
производству асфальтового бетона должна быть обеспечена безопасность для
работающих при возникновении следующих опасных и вредных производственных
факторов: запыленность и загазованность воздуха, уровень шума и вибрации, недостаточная
освещенность, отклонения от оптимальных норм температуры, относительной
влажности и скорости движения воздуха в рабочей зоне; электробезопасность
применяемых машин и оборудования.
Содержание вредных
веществ в воздухе рабочей зоны и параметры микроклимата не должны превышать
норм, установленных ГОСТ 12.1.005-88. Допустимые значения уровней шума и
вибрации, создаваемые машинами на рабочих местах, соответственно по
ГОСТ12.1.003-83 и ГОСТ12.1.012-90.
При выполнении работ по
приготовлении асфальтобетонной смеси в опасных зонах порядок допуска к
производству работ , а также границы опасных зон , в пределах которых действуют
опасные факторы, должны соответствовать СНиП III-4-80.
3.2. Требования
безопасности к производственному оборудованию при производстве асфальтового
бетона
При производстве
асфальтобетонной смеси существуют опасные и вредные производственные факторы,
которые негативно воздействуют организм на человека. Следовательно, нужно
выявить и знать какие ОВПФ существуют при производстве асфальтобетона для их
устранения.
На территории
асфальтобетонных заводов выделение загрязняющих веществ происходит в основном
следующих цехах:
- в цехе
подготовки битума,
- в цехе
производства и подготовки минеральных материалов (склады щебня, песка,
ленточные транспортеры, грохоты);
- в
котельной, гараже, складе ГСМ.
В воздух
рабочей зоны могут выделяться в основном следующие вещества: неорганическая
пыль с разным содержанием диоксида кремния, углеводороды, оксиды углерода карбита,
ангидрид сернистый, оксид серы, сажа, свинец и его неорганические содержания.
Для
обеспечения минимального загрязнения окружающей среды используют три типа
оборудования: сухие пылеуловители, мокрые пылеуловители (скрубберы) и
пылеуловители с рукавными фильтрами. Сухой пылеуловитель обычно устанавливается
перед остальными системами очистки и называется первичным пылеуловителем.
Мокрый пылеуловитель (мокрый скруббер) и пылеуловитель с рукавными фильтрами
являются вторичными пылеуловителями. Первичный пылеуловитель используется для
очистки дымовых газов от более крупных частиц заполнителя. Вторичный
пылеуловитель используется для очистки дымовых газов от мелких частиц
минеральных материалов (пыли).
Для работы
горелки требуется определенное количество воздуха.
Этот воздух
вместе с продуктами сгорания топлива и выпаренной из минеральных материалов влагой
перемещается через сушильный или сушильно-смесительный агрегат со скоростью, зависящей
от режима работы асфальтосмесительной установки. Содержание пыли в дымовых
газах возрастает пропорционально увеличению производительности дымососа. На
асфальтосмесительных установках непрерывного действия количество попадающей в
дымовые газы пыли можно значительно сократить путем ускорения подачи в
сушильно-смесительный агрегат битума. Чем раньше осуществляется подача битума в
сушильно-смесительный агрегат, тем меньше пыли захватывается потоком дымовых
газов. Загрязненность дымовых газов зависит от режима работы
сушильно-смесительного агрегата - степени заполнения барабана материалом,
расположения точки подачи битума и скорости движения газов. Загрязненность
дымовых газов может резко колебаться при изменении зернового состава
минеральных материалов и режимов работы асфальтосмесительной установки.
Под
эффективностью работы оборудования для очистки дымовых газов подразумевается
отношение количества пыли, оставшейся в пылеуловителе, к количеству пыли,
содержавшейся в дымовых газах до его прохождения через пылеуловитель. В
частности эффективность пылеуловителя можно определить по количеству частиц,
выбрасываемых из вытяжной трубы. Основным загрязнителем дымовых газов являются
мелкие фракции, мелкодисперсная пыль, которая попадает в атмосферу через
негерметичное оборудование или трубопроводы. Для асфальтосмесительных установок
периодического действия можно назвать три основных источника утечки
мелкодисперсной пыли: элеватор для подачи горячего материала на грохоты и в
смесительный агрегат. В результате разгрохотки горячих материалов появляется
мелкодисперсная пыль. Она также появляется в процессе цикла сухого смешивания в
смесительном агрегате. Для предотвращения выбросов мелкодисперсной пыли в
атмосферу необходимо закрыть грохоты герметичным кожухом и свести цикл сухого
перемешивания к минимуму.
Кроме этого
возможно применение специальной системы очистки дымовых газов от
мелкодисперсной пыли. Эта система состоит из трубопровода с регулируемыми
заслонками, который подводится с одной стороны к кожуху грохотов, бункерам для
хранения горячих материалов, весовому бункеру-дозатору и смесительному
агрегату, а с другой стороны - к вентилятору-дымососу, который подает пыль в
пылеуловитель второй стадии очистки. Если на асфальтосмесительных установок
вентилятор-дымосос для не используется, то трубопровод соединяется с
пылеуловителем второй ступени очистки. Как на асфальтосмесительных установках
периодического действия, так и на асфальтосмесительных установках непрерывного действия
трубопровод между сушильным и сушильно-смесительным агрегатом и оборудованием
для очистки дымовых газов может служить причиной попадания в атмосферу
мелкодисперсной пыли. Все отверстия в трубопроводе необходимо герметично
закрыть, чтобы вся находящаяся в дымовых газах пыль попадала в пылеуловитель.
Рекомендуется сразу устранить имеющиеся неплотности, чтобы вентилятор-дымосос
не осуществлял подсос дымовых газов, уменьшая тем самым его количество,
подаваемое к горелке. Таким образом, при работе с оборудованием для очистки
дымовых газов необходимо обращать внимание на следующее:
- необходимо
периодически контролировать цвет выходящих из вытяжной трубы дымовых газов.
- при
использовании мокрого скруббера необходимо регулярно проверять форсунки трубы
Вентури.
- необходимо
проверять чистоту воды в резервуаре-отстойнике в том месте, где вода
откачивается из резервуара.
- при
использовании пылеуловителя необходимо следить за тем, чтобы перепад давления в
рукавных фильтрах был в интервале от 50,4 до 152,4 мм водяного столба.
- температура
попадающего в пылеуловитель с рукавными фильтрами дымовых газов не должна
превышать 205°С.
- при
приготовлении асфальтобетонной смеси необходимо сравнивать фактический зерновой
состав с составом исходным.
В
битумоприемниках следует устанавливать автоматические газоанализаторы, при
отсутствии газоанализаторов периодически должен осуществляться лабораторный
анализ воздушной среды.
Для того,
чтобы избежать превышать указанных ПДК, следует соблюдать (в первую очередь
температурный режим), регулярно осуществлять профилактические осмотры и ремонт
оборудования, его поверку.
Для
предупреждения попадания в атмосферных осадков в расплавленный битум
битумоприемники должны быть расположены под навесом. В целях повышения
безопасности они должны быть оборудованы системами пароподогрева битума. В
системах пароподогрева битума должны быть устройства для непрерывного удаления
конденсата. Соединения всех элементов паропровода битума должны быть уплотнены.
Утечка пара и конденсата через уплотнения не допускается. Для переливания
жидкого битума из контейнеров и цистерн в битумоприемник последние должны быть
закрыты сплошными металллическии крышками, люками.
Люки должны
быть перекрыты металлическими решетками с ячейками размером не более 150х150мм.
Битумоприемники
и битумохранилища должны быть снабжены сигнализаторами максимально допустимого
уровня битума. Операции по опрокидывании. контейнеров с битумом и установке
пустых контейнеров в транспортное положение должны быть механизированы.
Битумоприемники
должны быть оборудованы площадками для обслуживания контейнеров, цистерн,
лебедок, применяемых для опрокидывания контейнеров. Рабочие, обслуживающие
битумоприемники, должны быть обеспечены инвентарными тормозными башмаками для
стопорения железнодорожных цистерн и контейнеров во время разгрузки, а также
переносными шлангами для по подключения пара к паровым рубашкам цистерн и
контейнеров.
Внутренний
осмотр, очистка ремонт битумоприемников и битумохранилищ следует производить
при температуре не выше 40 ºС по наряду-допуску.
При
эксплуатации битумоприемников и битумохранилищ запрещается:
- хождение по
крышам битумоприемников;
- присутствие
людей в зоне опрокидывания контейнеров и вблизи люка битумоприемника во время
слива;
-
передвижение железнодорожных платформ с не закрепленными контейнерами;
- слив битума
при незаторможенных контейнерах или цистернах;
Трубчатые
печи, предназначенные для окисления битума, должны быть оборудованы:
- запальником
для розжига форсунок;
- устройством
для продувки топки паром;
- манометрами
и термометрами для контроля давления и температуры битума на входе и выходе из
печи;
-
устройством, автоматически перекрывающим подачу топлива при падении давления
газа перед форсунками ниже допустимых
технологических
регламентов величин;
- звуковой и
световой сигнализацией, автоматически срабатывающей при прекращении подачи
топлива к форсункам.
Шум и вибрация
производственного оборудования также являются неотъемлемыми вредными
производственными факторами и поэтому не должны превышать оптимально-допустимых
норм и значений в соответствии с требованиями технологических регламентов и
нормативных документов.
3.3. Техника безопасности
при эксплуатации машин и оборудования
Основными и ответственными исполнителями мероприятий по
охране труда на асфальтобетонных заводах являются производители работ, а также
мастера цехов. В пределах порученных им объектах они обязаны:
- проводить первичный и
повторные инструктажи на каждом рабочем месте, а также повседневный контроль,
инструктаж и обучение рабочих безопасным приемам работы;
- обеспечивать рабочих средствами
индивидуальной защиты;
- отвечать за исправное
состояние ограждения мест работ – лестниц, переходов и укрепления траншей,
контролировать и отвечать за соблюдение работающими правил техники безопасности,
контролировать степень освещения рабочих мест, проходов и проездов;
- обеспечивать опасные
рабочие места предупредительными надписями, плакатами, участвовать.
Линейные механики и
энергетики на своих участках отвечают за техническое (исправное) состояние
машин и оборудования, за систематический контроль выполнения рабочими правил
техники безопасности при эксплуатации и ремонте дорожных машин, механизмов
подъемных приспособлений, механизированного и ручного инструмента, а также
электрооборудования.
Рабочие места на всех
участках работ должны обеспечивать безопасное выполнение всех видов работ. Для
этого рабочие места должны быть оборудованы необходимыми ограждениями,
защитными и предохранительными приспособлениями.
Посторонним лицам
находиться на рабочих местах и в зоне работ машин и оборудования запрещается.
На асфальтобетонных
заводах, а также в отдельных цехах должны быть аптечки со средствами для оказания
первой помощи пострадавшим.
Для каждого завода или
самостоятельного цеха разрабатывается инструкция по обеспечению пожарной
безопасности. Эта инструкция должна определять меры пожарной безопасности и
включать в себя: указания по содержанию территории, в том числе подъездных
дорог ко всем зданиям и сооружениям; правила и нормы хранения различных
материалов и веществ; систему производства пожароопасных работ; порядок
поведения рабочих на территории, а также на рабочих местах, где разрешено
разводить открытый огонь и курить; правила содержания средств пожаротушения,
пожарной связи и сигнализации.
Между зданиями и
сооружениями должны быть противопожарные разрывы, которые должны быть в течение
всего года в проезжем состоянии, не допуская даже кратковременного его
использования для складирования материалов и оборудования.
Пожарный инвентарь и
оборудование должны находиться на видных местах и быть в исправном состоянии.
Водоснабжение для тушение пожара должно осуществляться из водоемов или пожарных
гидрантов. Пожарные краны, рукава и стволы следует хранить в закрываемых и
опломбированных шкафчиках, дверцы которых должны легко открываться в случае
необходимости их использования при возникновении пожара.
Пожарный инвентарь и
первичные средства пожаротушения передаются под ответственность мастерам
участков или другим ответственным лицам.
Пусковые устройства
должны исключать возможность пуска электродвигателей машин, механизмов и
оборудования, а также электрических сетей посторонними лицами.
Неизолированные провода,
шины, контакты магнитных пускателей и предохранителей, находящихся вне
электротехнических помещений, должны быть со всех сторон ограждены или
находиться на высоте, недоступной для прикосновения к ним.
Каждая машина, механизм и
оборудование должны быть закреплены приказом за определенными лицами или
бригадой, обслуживающей их.
Самоходные машины должны
находиться в технически исправном состоянии и иметь световую, звуковую или
комбинированную сигнализацию. Работать на неисправных машинах запрещается.
Машины, механизмы и
оборудование, имеющие электропривод, должны иметь заземление в соответствии с "Инструкцией
по заземлению передвижных строительных механизмов и электрифицированного
инструмента" (СН 38-58).
В зоне работы или на машине
необходимо вывешивать надписи, знаки или плакаты по технике безопасности.
На всех емкостях,
предназначенных и используемых для хранения токсичных и огнеопасных материалов
(органических растворителей – бензола, ксилола, толуола, сольвента, бензина и др.),
должны быть соответствующие надписи краской "Яд", "Огнеопасно".
Емкости для хранения
токсичных и огнеопасных материалов должны закрываться герметичными крышками и
запираться. Наполнение емкостей и раздачу материалов необходимо производить с
помощью насосов и трубопроводов. Раздача материалов черпаками, ведрами и
сифонами запрещается. Для масляных ванн и картеров двигателей должна быть
указана и их вместимость.
В местах перехода через
конвейеры, траншеи и канавы должны быть установлены мостики шириной не менее
0,6 м с перилами высотой 1 м.
Внутризаводские дороги и
пешеходные дорожки в зимнее время должны регулярно очищаться от снега и льда и
посыпаться песком или мелким шлаком.
4. Расчет
основных параметров оборудования при производстве асфальтового бетона
4.1. Расчет
ширины уступа площадок карьера
Строительные
и дорожные машины в процессе работы взаимодействуют с грунтом, естественными
каменными и скальными материалами и породами или искусственными строительными
материалами, обеспечивая при этом отделение разрабатываемой среды от массива,
ее резание, копание или зачерпывание.
Основой сырья для
производства асфальтобетонов, строительства оснований автомобильных дорог
являются традиционные изотропные горные породы - граниты, базальты, песчаники,
известняки и т.д., месторождения которых имеют ограниченное распространение.
В нашей стране сырьевые
материалы для производства асфальтового бетона добывают в карьерах открытым
способом.
Определим текущий
коэффициент вскрыши kв, если слой
полезного ископаемого постоянной мощности залегает горизонтально и его
разрабатывают одним уступом, имеющим высоту 13,9 м, а покрывающие породы,
залегающие также слоем постоянной мощности разрабатывают двумя способами
подступами высотой соответственно 19,2 м и 7,4 м.
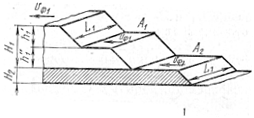
Рис.1 Схема уступов в
карьере
Так как текущий коэффициент вскрыши определяют за конкретный
отрезок времени t, например, за месяц то за этот же период находят объемы вскрышных
Q1 и добычных Q2 работ. По мере продвижения
вскрышного забоя А1 на расстояние L1 добыча полезного
ископаемого забоем а2 продвинется
также на расстояние L1 а фронт работ будет постепенно подвигаться в направлении границы
карьера со средними скоростями (в м/месяц) и
. При постоянных значениях
высоты уступов и подуступов (в м3) получим
,
а так как вскрышные и добычные работы ведут одновременно, то
скорости производств равны:
При этом условии определим коэффициент вскрыши (в м3/м3)
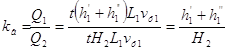 (1)
при =19,2
м, =7,4 м, Н2 =13,9
м, м3/м3
При мощности уступа
добываемой породы 13,9 (число и мощности уступов пустой породы 19,2 м и 7,4 м
коэффициент вскрыши составит 1,91 м3/м3.
4.2. Расчет основных
размеров параметров работы экскаваторов
Одноковшовые экскаваторы используют для выполнения наиболее
тяжелых и трудоемких работ, связанных с копанием грунта, т. е. с отрывом части
его от целого массива, с перемещением порции грунта в ковше на небольшое
расстояние путем поворота платформы и с погрузкой его в транспортные средства.
Определим длину стрелы,
теоретическую и эксплуатационную производительность и основные размеры ковша
для экскаватора ЭКГ – 3,2 при разработке грунта – мелкий гравий, вид ковша –
драглайн с зубьями, работа в отвал, угол поворота платформы - 90º,
Длину стрелы (в м) одноковшового экскаватора, рассчитывают по
эмпирической формуле
(2)
где G - масса экскаватора, т;
k – коэффициент, равный 1,9 - 2,1 –
для универсальных экскаваторов
и 1,85- для карьерных экскаваторов. Принимаем коэффициент
k=1,85 (т.к. экскаватор
карьерный);
В нашем
случае экскаватор ЭКГ – 3,2 имеет массу G =150 (т). Подставив значения
величин в формулу, получим

Теоретическая
производительность (в м3/ч)
, (3)
где q – геометрическая емкость ковша, м³;
n0 – теоретическое число циклов в минуту при углах
поворота
платформы на разгрузку и
в забой равных 90º, высоте забоя,
равной высоте расположения
напорного вала экскаватора при
расчетных скоростях и усилиях
,
где t ц.т. - теоретическая производительность
цикла, с.
Мелкий гравий относится к
II группе, значит емкость ковша
принимаем q=4; для карьерного экскаватора ЭКГ -
3,2 теоретическая производительность цикла t ц.т. =22 (с), значит
м³/ч
Исходя из полученных
данных, вычислим теоретическую производительность экскаватора
м³/ч
Эксплуатационная
производительность (в м3/ч)
, (4)
где q – геометрическая емкость ковша, м³;
n – фактическое
количество циклов в 1 мин (для строительных и
карьерных экскаваторов
n=2-4);
kн - коэффициент наполнения
ковша (kн=0,55-1,5);
kи - коэффициент использования экскаватора во
времени, равный
отношению
числа часов чистой работы экскаватора к
продолжительности
рабочих смен отчетного периода (kи=0,7-0,8);
kp – коэффициент разрыхления грунта,
принимается по табл.
В нашем случае
эксплуатационная производительность:
м³/ч
Определим
геометрическую емкость ковша (в м3)

где с – коэффициент, учитывающий форму днища и закругления стенок
ковша (с
= 0,9 — для ковша с зубьями, с=0,75 — для ковша с
полукругло режущей
кромкой);
В, Н, L — соответственно ширина,
высота и длина ковша,
измеренные по
расстояниям между внутренними
поверхностями
соответствующих стенок ковша, а также
днищем и
верхней кромкой стенки ковша, м.
Для прямой и
обратной лопаты высоту ковша Н измеряют от стенки с зубьями на середине ее
длины до стенки, к которой крепится рукоять. При более точном определении
объема ковша Н и L рассчитывают как средние значения предельных величин, ввиду того,
что, например, ковш прямой лопаты для удобства разгрузки расширяется книзу.

Т.к. драглайн с зубьями, принимаем коэффициент,
учитывающий форму днища и закругления стенок ковша с = 0,9.
ширина ковша ;
высота ковша 
длина ковша .
Выполняем проверочный
расчет:
q = 0,9 *1,9*1,19*2,06=4,2≈4, что не превышает значения
погрешности коэффициентов.
4.3. Расчет
основных параметров конвейера
К машинам непрерывного транспорта в строительстве
относятся ленточные конвейеры, ковшовые элеваторы, винтовые конвейеры,
аэрожелоба, устройства пневматического транспорта и самотечные установки.
Производительность
машин и установок непрерывного транспорта зависит от погонной нагрузки q (в кг/м) и скорости
движения v (в м/с) и не зависит от пути транспортирования.
Рассчитаем
погонную нагрузку и производительность элеватора:
Погонная
нагрузка элеватора при перемещении груза в ковшах рассчитывается по формуле
(5)
где i0 – геометрическая емкость
ковша, м³;
ρ – насыпная масса
материалов, кг/м³;
kн – коэффициент наполнения
ковшей (среднее отношение объема материала заполняющего ковш к геометрической
емкости ковша), принимаемый kн=0,6 для глубоких и остроугольных ковшей,
kн=0,4 для мелких ковшей;
d – шаг между ковшами
Геометрическая
емкость ковша 5,9 дм³
= 0,0059 м³, насыпная масса материалов 2000 кг/м³,
коэффициент наполнения ковшей для глубоких и остроугольных ковшей 0,6, шаг между ковшами 510 мм = 0,51 м
Следовательно, погонная нагрузка
кг/м³
Производительность машин и установок непрерывного
транспорта зависит от погонной нагрузки q (в кг/м) и скорости
движения v (в м/с) и не зависит от пути транспортирования. В
общем виде производительность (в т/ч)
Рассчитаем
производительность элеватора по формуле:
, (6)
где q – погонная нагрузка, кг/м³;
v – скорость движения, м/с.
В нашем
случае погонная нагрузка равна 4 кг/м³, а скорость движения
1,35 м/с, подставив
значения величин, получим
т/ч
Определим натяжение набегающей
ветви ленты конвейера (в Н), если коэффициент ленты между лентой и приводным
барабаном 0,2, угол обхвата приводного барабана ленты 360º, длина ленты
конвейера 29, 4 м, ширина 850 мм, высота подъема материала 10 м, скорость ленты
конвейера 1,4 м/с, производительность 160 т/ч.
, (7)
где e - основание натурального логарифма (в
нашем случае f=0,2,
α=360º, значит, по табл. e =3,51);
f - коэффициент трения между лентой и приводным барабаном;
α - угол обхвата приводного барабана
ленты;
P – окружное усилие, передаваемое на
барабан, Н
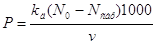
где kд – коэффициент динамичности, принимаемый от 1,1 до 1,2
(принимаем kд=1,15);
N0 – мощность на приводном барабане ленточного
конвейера, (кВт) определяется по формуле

где k – коэффициент, зависящий от длины
конвейера L
L, м
|
<15 |
16-30 |
30-45 |
>45 |
k
|
1,25 |
1,1 |
1,05 |
1 |
(в нашем случае длина
конвейера 29,4 м, значит принимаем k=1,1);
c – коэффициент, значение которого
принимают от ширины ленты, если ролики конвейера установлены на
шарикоподшипниках
В, мм
|
500 |
650 |
800 |
1000 |
1200 |
с
|
0,018 |
0,023 |
0,028 |
0,038 |
0,048 |
(в нашем случае ширина
конвейера 850 мм=0,85 м, значит принимаем с=0,028);
Nсбр. – мощность на сбрасном барабане, кВт
(принимаем Nсбр.=0);
v – скорость ленты конвейера;
П – производительность;
Lг – горизонтальная проекция длины конвейера от угла
наклона β конвейера
так, что Lг = Lcosβ,м;
H – высота подъема материала Н = Lsinβ, м
Н = Lsinβ
Выразив из предыдущей
формулы β и, подставив величины значений, получим
 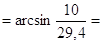 
Горизонтальная проекция
длины конвейера от угла наклона β
Lг = Lcosβ=29,4*cos19,88= 29,4*0,94=27,6 м
Получив значение
горизонтальной проекции длины конвейера от угла наклона β, можно
рассчитать мощность на приводном барабане ленточного конвейера (кВт)
кВт
Отсюда, зная мощность на
приводном барабане ленточного конвейера, получим окружное усилие, предаваемое
на барабан
Н
Определим натяжение
набегающей ветви ленты конвейера
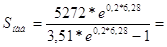 Н
4.4. Выбор и расчет
дробильно-помольного оборудования с учетом требований производственной
безопасности
Щековые дробилки
используют для крупного и реже среднего дробления пород высокой и средней
прочности. Первичное дробление осуществляется в щековых дробилках с простым
качанием щеки, которые создают большие усилия при измельчении и позволяют
перерабатывать куски горной массы размером до 700—1200 мм и более.
При
измельчении различают дробление и помол. Дробление подразделяют на крупное —
размер куска после дробления от 80 до 200 мм, среднее — от 20 до 80 мм, мелкое
— от 2 до 20 мм. Помол подразделяют на грубый — размер частиц после помола от
0,2 до 2 мм, тонкий — от 0,01 до 0,2 мм и сверхтонкий — менее 0,01 мм.
Нормальная работа щековых
дробилок мало зависит от влажности материала при дроблении пород с небольшим
содержанием глины. При большом содержании глины и высокой влажности сырья (6%)
производительность дробилок падает, особенно при среднем дроблении, из-за
комкования материала.
Рассчитаем оптимальную
угловую скорость и частоту вращения вала щековой дробилки, если ход щеки 23 мм =
0,023м, угол между щеками 19º, коэффициент торможения материала 0,8.
Угловая скорость эксцентрикового вала щековой дробилки (в
рад/с)
, (8)
где kт – коэффициент торможения материала при разгрузке (kт=0,9)
g – ускорение свободного падения (g=9,81 м/с2)
α – угол между щеками (α=15º-23º)
S – наибольший ход щеки по горизонтали
у разгрузочного отверстия, м
а)
б)
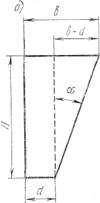 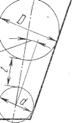
|
|
Рис. 3 Схема к
расчету производительности щековой дробилки
|
|
Подставив величины
значений, получим
рад/с
ω=2πn;  об/c
Щековые дробилки для
среднего дробления выпускают производительностью 5—200 т/ч.
Рассчитаем производительность
щековых дробилок П (в т/ч). Коэффициент рыхления 0,42, наименьшие размеры разгрузочной
щели 54 м, ход щеки 73 м , угол между щеками 21,3º , вид материала –
гранит крупнозернистый (ρ=2700
кг/ м³), длина разгрузочного
отверстия 600 мм=0,6 м , частота вращения вала 5,12 сˉ¹
(9)
где S – ход щеки по горизонтали у разгрузочного
отверстия, м;
α – угол между щеками, град. (α=15º-23º);
ℓ - длина разгрузочного отверстия
равная ширине щеки, м;
n – частота вращения вала, сˉ¹;
kр – коэффициент разрыхления материала (kр=0,3-0,65);
dср – средний размер кусков выходящих из дробилки
; 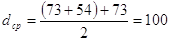
Отсюда, т/ч
4.5. Машины для
тонкого измельчения (помола) материала
Шаровые мельницы используются
после дробления и служат для помола и превращения сырьевых материалов в
сырьевую муку. При вращении слоя шаров с барабаном
шаровой мельницы на каждый шар действует сила тяжести, направленная вертикально
вниз, и центробежная сила инерции.
Рассчитаем угловую и
окружную скорости и частоту вращения барабана шаровой мельницы для сухого
помола при гладкой футеровке и при футеровке бронеплитами с продольными
ребрами, а также для мокрого помола и определить коэффициент загрузки, если
барабан мельницы загружен мелющими телами до уровня 1920 мм = 1,92 м.,
внутренний диаметр нефутерованного барабана 2,7м=2700 мм, угол α =51.9º.
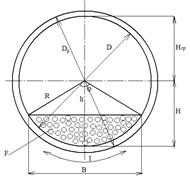
Рис. 4 Схема барабана
шаровой мельницы заполненного мелющими телами
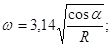
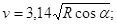
,
где R—радиус окружности, описываемой центром тяжести шара, м;
w — угловая скорость шара, рад/с;
n — частота вращения шара, с-1;
v — окружная скорость шара, м/с.
В технической
характеристике обычно указывают внутренние размеры не футерованного барабана,
поэтому расчетный диаметр D
определяем по формуле:
Dр = Dб – 2δ, D ≈ 0,94*Dб,
где Dб – внутренний диаметр нефутерованного барабана, м;
δ – толщина футеровки равная равная 2,9-3,1% от диаметра барабана, м,
Внутренний диаметр нефутерованного
барабана нам дан – 2,7 м
Следовательно, Dр ≈ 0,94*Dб = 0,94*2,7 =2,538 м
Определим радиус окружности
описываемой центром тяжести шара:
R = Dр/2 = 2,538/2 = 1,27 м
Рассчитаем угловую
скорость, окружную скорости и частоту вращения барабана шаровой мельницы для
сухого помола при гладкой футеровке:
Угловая скорость = рад/с
Окружная скорость: = м/с
Частота вращения: = сˉ¹
Рассчитаем угловую
скорость, окружную скорости и частоту вращения барабана шаровой мельницы для
сухого помола при футеровке бронеплитами с продольными ребрами:
Частота вращения:  сˉ¹
Угловая скорость: ω2
= 2πn2 = 2*3,14*0,42 = 2,64 рад/с
Окружная скорость: ύ2
= π Dрn2 =
3,14*2,538*0,42 = 3,35 м/с
Рассчитаем угловую и
окружную скорости и частоту вращения барабана шаровой мельницы для мокрого
помола:
Частота вращения:  сˉ¹
Угловая скорость : ω3
= 2πn3 = 2*3,14*0,74= 4,65 рад/с
Окружная скорость: ύ3
= π Dрn3 = 3,14*2,538*0,74=5.9
м/с
Эффективность шаровых
мельниц зависит от степени заполнения барабана мелющими телами, которая характеризуется
коэффициентом загрузки, представляющим собой отношение площади поперечного
сечения слоя загрузки в спокойном состоянии к площади поперечного сечения
барабана, и рассчитывается по формуле
(10)
где F - площадь поперечного
сечения слоя загрузки, м2;
R – внутренний радиус
нефутерованного барабана, м.
Площадь
кругового сегмента равна разности площади кругового сектора F1 и площади
равнобедренного треугольника F2.
Радиус футерованного
барабана: R = D/2 = 3/2 = 1,5 м

,
где F1- площадь сегмента;
F2 – площадь
равнобедренного треугольника

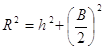



  


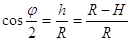
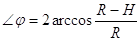



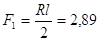
м²
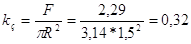
Анализируя полученный результат, приходим к выводу, что
коэффициент загрузки kз=0,32 соответствует оптимальному значению, это
значит, что барабан мельницы загружен соответственно.
Заключение
В результате проделанного
курсового проекта, была изучена технологическая схема процесса производства
асфальтового бетона, принцип работы технологического оборудования, выявлены
источники опасных выделений, изучены правила безопасности при работе с
технологическим оборудованием, общие требования безопасности.
При производстве
асфальтового бетона приходится иметь дело с вибрирующими и шумовыми
механизмами, оборудованиями. В каждом случае следует руководствоваться
специальными правилами техники безопасности.
Основным технологическим
оборудованием, применяемым при производстве асфальтобетона, являются: агрегат
пылеулавливания, агрегат минерального порошка, битумоплавильный и сушильный
агрегаты, смесительный агрегат, одноковшовые элеваторы, которые служат
источниками таких вредных факторов, как вибрация, шум, тепловыделения,
загрязнение окружающего воздуха и т.д., которые нормируются ГОСТами, СНиПами и
другими нормативно-техническими документами.
В данном проекте был
произведен расчет ширины площадок уступов карьера, расчет и размеры основных
параметров и выбор конвейера, удовлетворяющего заданным условиям; расчет машин
измельчения материалов (щековые дробилки, шаровые мельницы).
Список используемой
литературы
1. Рыбьев И.А., Строительные
материалы
2. Клюковский Г.И., Общая
технология строительных материалов
3. Ицкович С.М., Заполнители для бетона;
Минск; изд. Высшая школа, 2001.
4. Горчаков Г.И., Строительные материалы, М.,изд. Высшая
школа, 1999.-352 5. Мухленова И.П., Основы химической технологии. – 4-е изд.,
перераб. и доп.— М.: Высш. школа, 1999. – 463 с.: ил.;
6. http://www.bestreferat.ru/referat-57965
7. http://stroy-spravka.ru/article/raznovidnosti-asfaltovykh-betonov
Лист 1
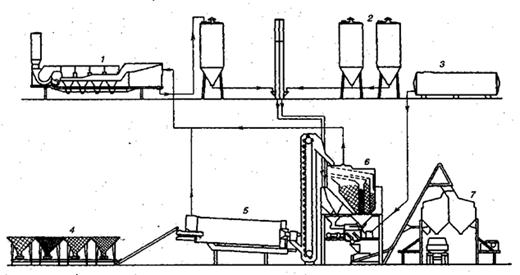
Технологическая схема
производства асфальтобетонной массы:
1 — агрегат
пылеулавливания; 2 — агрегат минерального порошка; 3 — битумоплавильный
агрегат; 4 — агрегат питания; 5 — сушильный агрегат; 6 — смесительный агрегат;
7 — накопительный бункер
Лист 2
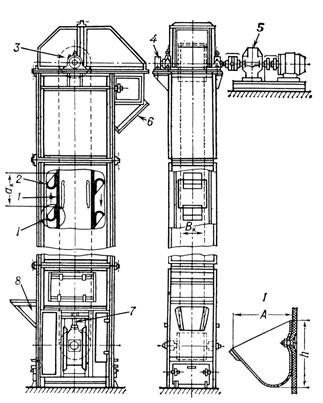
Вертикальный ленточный
ковшовый элеватор:
1 — тяговый орган; 2 —
ковш; 3 — приводной барабан; 4 — останов; 5 — привод; 6 — разгрузочный
патрубок; 7 — шпиндель натяжного устройства; 8 — загрузочный патрубок.
|