Контрольная работа: Химические методы получения порошкообразных материалов и извлечения железа
Контрольная работа: Химические методы получения порошкообразных материалов и извлечения железа
ВВЕДЕНИЕ
Как с точки зрения экономической, так и экологической
существует потребность в разработке процесса прямого превращения отходов
механической обработки, таких как мелкая стружка, в порошок, который может быть
использован в порошковой металлургии железа. По оценке одна только фирма «Форд
Мотор Ко» производит на разных заводах 105 000 т стружки низколегированной
стали, которая поступает в продажу на рынок в качестве скрапа, используемого
для загрузки в печь при некоторых процессах плавления.
Глава 1. ПОРОШКОВЫЕ МАТЕРИАЛЫ
ОБЩИЕ СВЕДЕНИЯ
Основным
сырьем порошковой металлургии являются порошки чистых металлов и сплавов, а
также порошки неметаллических элементов. Под термином «порошковая металлургия»
в соответствии с ГОСТ 17359–82 принято понимать «область науки и техники,
охватывающую область производства металлических порошков, а также изделий из
них или их смесей с неметаллическими порошками». Порошковая металлургия — один
из наиболее прогрессивных процессов превращения металла в изделие, с помощью
которого обеспечиваются свойства изделия, полученного традиционными методами,
или свойства, которые не могут быть достигнуты при использовании иных
технологических процессов.
Применение
технологических процессов порошковой металлургии при изготовлении деталей и
изделий различного назначения позволяет резко повысить коэффициент
использования металла (КИМ) — до 96–98 % за счет сокращения отходов при
обработке, а также возможного передела отходов в исходный материал (порошок);
во многих случаях заменить дефицитные и дорогостоящие металлы и сплавы менее дефицитными
и дорогими, понизить энергоемкость и трудоемкость производства, а
следовательно, уменьшить себестоимость готовой продукции без снижения, а в ряде
случаев — даже при повышении ее эксплуатационных свойств.
К химическим
методам получения порошков относится восстановление оксидов и солей металлов
твердыми или газообразными восстановителями, диссоциация карбонилов и
неустойчивых соединений, металлотермия. Большую группу порошков — олово,
серебро, медь и железо — получают методами электролитического осаждения
металлов в виде порошка из водных растворов солей, а также электролизом
расплавленных сред (тантал, ниобий, уран и др.).
К
механическим методам получения порошков относятся измельчение металла резанием,
размол в шаровых, вибрационных, конусно-инерционных и других мельницах и
дробилках, распыление струй жидкого металла сжатым паром, газом, водой.
Выбор метода
определяется возможностью получения порошка необходимого качества и
экономической целесообразностью применения того или иного метода. Наибольшее распространение
получили химические методы и методы распыления, которые при минимальных
затратах обеспечивают получение целой гаммы порошковых металлов и сплавов со
свойствами широкого диапазона.
Возможность
применения порошка для изготовления конкретных изделий определяется его
свойствами, которые зависят от метода получения и природы металла порошка.
Металлические порошки характеризуются технологическими, физическими и
химическими свойствами.
К
технологическим свойствам, согласно ГОСТ 19440–94, относятся: насыпная
плотность, представляющая собой массу единицы объема свободно насыпанного
порошка; относительная плотность — отношение насыпной плотности и плотности
металла в беспористом состоянии; текучесть — способность порошка заполнять
определенную форму, выражающуюся через число граммов порошка, протекающего за 1
с через воронку с диаметром выходного отверстия (носика воронки) 2,5 мм; прессуемость (ГОСТ 25280–90) — способность порошка под давлением сжимающих усилий
образовывать заготовку заданной формы и размеров (формуемость) с минимально
допустимой плотностью (уплотняемость).
К физическим
характеристикам порошков относятся форма и размер частиц порошков. Они могут
резко различаться по форме (от нитевидных до сферических) и размерам (от долей
до сотен и даже тысяч микрометров). Важная характеристика порошков —
гранулометрический состав, под которым понимается соотношение количества частиц
различных размеров (фракций), выраженное в процентах. Размеры частиц порошка
обычно составляют 0,1–100 мкм. Фракции порошков размерами более 100 мкм
называют гранулами, менее 0,1 мкм — пудрой. Определение
гранулометрического состава может производиться с помощью просеивания порошка
через набор сит (ГОСТ 18318–94). Этот метод применим к порошкам размерами более
40 мкм; для более дисперсных порошков применяется метод седиментации (ГОСТ
22662–77) и микроскопический анализ с помощью оптического или электронного
микроскопа (ГОСТ 23402–78). Также к физическим характеристикам относится
удельная поверхность порошков, под которой понимают суммарную поверхность всех
частиц порошка, взятого в единице объема или массы.
К химическим
характеристикам относятся химический состав порошка (как порошка чистого
металла, так и порошка сплава), определение которого производится по методикам
соответствующих компактных (беспористых) металлов и сплавов.
К химическим
характеристикам относят также пирофорность — способность порошка
самовозгораться при соприкосновении с воздухом — и токсичность — ядовитость
порошков. Если в компактном состоянии большинство металлов безвредны, то в
порошковой форме, попадая в атмосферу помещений, они образуют аэрозоли, которые
при вдыхании воздуха или приеме пищи могут вызывать болезненное состояние.
Широкое
применение имеют порошки меди, никеля и других металлов. Согласно ГОСТ 4960–75
выпускаются и применяются следующие порошки меди: ПМА, ПМАу, ПМС-1у, ПМС-Н и
т. д. Химические составы этих марок порошков приведены в табл. 21.2. Здесь
в названии марок две первые буквы обозначают порошок медный (ПМ), следующие: С
— стабилизированный, К — конопаточный, Н — низкодисперсный; индексы, в
частности у, Н, В и др. — со специальными свойствами. В табл. 21.3 даны области
применения этих порошков.
Медный
порошок не должен иметь посторонних примесей и комков и по цвету
соответствовать образцу, согласованному изготовителем и потребителем. Удельное
электрическое сопротивление медного порошка марки ПМА не должно превышать 25
мкОм м.
1.1 Принципы отбора изделий для изготовления методами
порошковой металлургии
В связи с
ограниченными возможностями формообразования деталей при изготовлении их
методами порошковой металлургии важное значение приобретают принципы отбора
деталей, переводимых на изготовление их методами порошковой металлургии. При
этом необходимо учитывать ряд факторов — материал, применяемый при их
изготовлении, режимы их термической и химико-термической обработок и обработки
резанием, условия и режимы эксплуатации изделия. Одним из определяющих факторов
является сложность их формы. Общие требования к форме деталей изложены в ГОСТ
29278–92 («Изделия порошковые. Конструктивные элементы»). В зависимости от
применяемых конструктивных элементов изделия порошковой металлургии различают
простой, сложной и особо сложной форм.
К изделиям
простой формы относятся:
·
изделия без
переходов по высоте;
·
изделия без
отверстия или с одним отверстием и с торцами, ограниченными параллельными
плоскостями.
Дополнительными
конструктивными элементами изделий простой формы являются стенки, фаски, пазы и
зубья.
К изделиям
сложной формы относятся:
·
изделия с одним
переходом по высоте, без отверстия и с торцами, ограниченными параллельными
плоскостями;
·
изделия с одним
или несколькими отверстиями, с одним переходом по высоте и торцами,
ограниченными параллельными плоскостями.
К изделиям
особо сложной формы относятся:
·
изделия с двумя
или более переходами и буртами по высоте, с торцами, ограниченными
параллельными или непараллельными плоскостями, криволинейными плоскостями;
·
изделия,
ограниченные одной или более коническими, сферическими и другими криволинейными
поверхностями.
Дополнительными
конструктивными элементами изделий сложной и особо сложной формы являются
стенки, фаски, пазы, зубья, бурты, выступы, уклоны, углубления в торцах.
В зависимости
от сложности формы изделий, отходы при производстве и затраты на механическую
обработку могут перекрывать другие преимущества порошковой металлургии.
Применение порошковых методов изготовления изделий будет оправдано только
тогда, когда в общей технологии изготовления достигается положительный
экономический эффект или другие методы изготовления не обеспечивают заданных
свойств.
Оценка
экономической целесообразности изготовления изделий простых и сложных форм
методами порошковой металлургии не представляет особых сложностей и в основном
отражает их серийность. В случае изготовления изделий особо сложной формы
рентабельность производства дополнительно определяется затратами на
изготовление деталей пресс-форм, которые возрастают по мере усложнения формы
порошковых изделий, необходимостью применения специальных прессов, например,
прессов с боковым давлением и т. п., повышенными затратами на механическую
обработку. При прессовании в пресс-формах круп-ных деталей относительная
стоимость изделия резко увеличивается, так как требуется применение более
мощных (обычно гидравлических) прессов, которые, как правило, тихоходны, что
снижает производительность труда. В связи с тем что при прессовании порошков
применяются высокие давления (500–1000 МПа), площадь поверхности, на которую
прикладывается давление прессования, лимитируется размерами пресс-формы и
мощностью пресса.
Конструктор
при проектировании порошковых изделий должен учитывать возможные изменения
размеров при прессовании и спекании порошковых заготовок, величины которых в
большинстве случаев определяются экспериментально, и назначать более жесткие и
легко воспроизводимые допуски, определенные в ГОСТ 29278–92. Установлено, что
методами порошковой металлургии можно получать готовые изделия без механической
обработки отклонением перпендикулярно к направлению прессования в пределах от
0,025 до 0,130 мм на длине 25 мм. Более жесткие отклонения могут быть получены
с помощью специальных методов порошковой металлургии — повторного прессования
(калибрования) после спекания или динамического горячего прессования, горячей
штамповки. Шероховатость прессованных изделий зависит от шероховатости рабочих
поверхностей деталей пресс-форм. Внешние поверхности порошковых изделий имеют
практически ту же шероховатость, что и рабочие поверхности матрицы, знаков,
сердечников и других элементов пресс-формы.
Порошковые
материалы, используемые для изготовления изделий конструкционного назначения,
могут быть разделены на две группы: 1) для изготовления изделий в целях замены
обычных углеродистых и легированных сталей, чугунов, некоторых цветных металлов
и сплавов и 2) материалы со специальными свойствами, получить которые можно
только при производстве изделий методами порошковой металлургии.
Наиболее
характерными деталями первой группы являются шатуны, шестерни, храповики,
кулачки, ригеля, накидные и специальные гайки, рычаги и многие другие, которые
выпускаются промышленностью методами литья и механической обработки.
Изготовление деталей этой группы рентабельно только при массовом производстве
одинаковых изделий, так как изготовление пресс-форм, установка их на пресс и
отладка процесса прессования — длительная и дорогостоящая операция. Так,
например, если производительность прессования в зависимости от типа пресса
(пресс-автомат, механический, гидравлический прессы) составляет от 150–200 до
2000 и более прессовок в ч, то на смену инструмента (пресс-формы) и его наладку
затрачивается от 1–2 до 20–30 ч. В связи с этим, принято считать, что
изготовление изделий методами порошковой металлургии может быть оправдано в том
случае, если эти изделия составляют в серии 10 000–50 000 штук
(простой формы), 5000–10 000 штук (сложной формы) и 500–1000 штук (особо
сложной формы). В некоторых случаях производство более мелких партий порошковых
изделий связано со сложностью или невозможностью изготовления изделий
традиционными методами, а используемые порошковые технологии снижают
себестоимость, материалоемкость и энергозатраты и повышают производительность
труда,
Глава 2. КОНСТРУКЦИОННЫЕ ПОРОШКОВЫЕ
МАТЕРИАЛЫ
В зависимости
от плотности и назначения порошковые материалы подразделяются на две группы: 1)
плотные — материалы с минимальной пористостью, изготовленные на базе порошков
железа, меди, никеля, титана, алюминия и их сплавов; и 2) пористые, в которых
после окончательной обработки сохраняется свыше 10–15 % пор по объему. Первая
группа материалов нашла широкое применение в машино- и приборостроении,
автомобильной и авиационной технике и других отраслях оборонного и
общегражданского производства. Высокая пористость материалов второй группы
обеспечивает приобретение ими специальных свойств и позволяет применять их для
изготовления специальных изделий (изделий антифрикционного назначения,
фильтров, деталей охлаждения и т. п.). При производстве этой группы
деталей применяются железографитовые материалы, бронзы, нержавеющие стали.
Особое значение
имеют инструментальные порошковые материалы. К их числу относятся порошковые
быстрорежущие стали, карбидостали, твердые сплавы, материалы на основе
сверхтвердых соединений (нитридов, боридов и т. д.) и алмазные материалы.
2.1 Конструкционные порошковые материалы на основе железа
Основным
документом, регламентирующим марки и свойства применяемых в России
конструкционных материалов на основе железа, является ГОСТ 28378–89. Согласно
этому нормативному документу, все материалы на основе железа делятся на:
·
стали
малоуглеродистые, углеродистые и медистые;
·
стали
никельмолибденовые, медьникелевые, медьникельмолибденовые;
·
стали хромистые,
марганцовистые, хромникельмарганцовистые;
·
стали
нержавеющие, предназначенные для деталей, применяемых в различных отраслях
техники.
Классификация
порошковых сталей подчиняется тем же правилам, что и принятым для сталей
традиционных методов получения. Однако в дополнение к обычным методам
классификации — по равновесной структуре, по структуре, полученной при нагреве
выше точки охлаждении
на спокойном воздухе и т. п. — для порошковых сталей существует еще один
способ классификации. В зависимости от объемного содержания пор порошковые
стали подразделяются на непроницаемые (содержание пор менее 5–8 %), полупроницаемые
(от 8 до 14 % пор) и проницаемые (пористость более 12–14 %). По
технологии производства их можно подразделить на: однократно и многократно
прессованные в условиях статических нагрузок в закрытых пресс-формах при
обычных и высоких температуpax; стали, полученные при совмещении холодного
прессования и спекания высокопористых заготовок с последующим динамическим
горячим прессованием или горячей штамповкой; полученные экструзией, прокаткой,
взрывным прессованием и т. п.
Конструкционные
порошковые стали — это спеченные материалы, используемые для замены литых и
кованых сталей при изготовлении деталей машин и приборов методами порошковой
металлургии. Условное обозначение таких материалов состоит из букв и цифр,
например: сталь порошковая конструкционная медьникелевая со средней массовой
долей углерода 0,4 %, никеля 2 %, меди 2 % и минимальной
плотностью 6400 кг/м3 в соответствии с ГОСТ 28378–89 будет иметь
следующее обозначение: ПК40Н2Д2-64.
Буквы в марке
стали указывают: П — на принадлежность материала к порошковому, К — на
назначение материала — конструкционный, остальные буквы и цифры — на содержание
тех или иных легирующих элементов (Д — медь, Х — хром, Ф — фосфор, К — сера, М
— молибден, Г — марганец, Т — титан, Н — никель). Основу материала — железо
— в обозначении марок не указывают. Цифры, стоящие за буквами ПК, указывают на
среднюю массовую долю углерода в сотых долях процента. Массовую долю углерода,
равную 1 %, в обозначении марки материала, согласно ГОСТ 28378–89, не
указывают. Цифры, стоящие за остальными буквами, означают содержание легирующих
элементов в процентах; отсутствие цифры указывает на то, что массовая доля
легирующего элемента не превышает одного процента.
Условное
обозначение конструкционного порошкового материала состоит из обозначения его
марки — ПК40Н2Д2-64 и через дефис — его минимальной плотности — 6400 кг/м3.
Основой
порошковых сталей служит железо, свойства которого при спекании оказывают
большое влияние на формирование структуры и свойств стали. Наряду с порошковыми
сталями порошковые изделия могут изготавливаться на основе одного железного
порошка, а также железа, легированного другими элементами.
Применение в
качестве исходного материала чистого железного порошка при изготовлении
конструкционных деталей ограничено из-за низких прочностных свойств спеченного
железа. В основном оно применяется для изготовления ненагруженных деталей,
различных уплотнительных изделий и т. п. Свойства таких изделий зависят от
их плотности, величины и характера межчастичных границ, метода получения порошка,
гранулометрического состава, удельной поверхности частиц, внутренней их
рыхлости, технологии прессования (величины давления и скорости прессования),
кратности прессования, температуры и времени спекания.
Для получения
практически беспористых изделий с повышенными механическими свойствами
применяют горячее изостатическое прессование- экструзию, динамическое горячее
прессование.
В связи с
низкой прочностью и твердостью спеченного железа, для повышения его
механических свойств в железный порошок при приготовлении порошковой смеси
вводят легирующие добавки (фосфор, медь, хром, никель, молибден), а спеченные
изделия подвергают химико-термической обработке: азотированию, сульфидированию,
хромированию.
Медь в
железные изделия вводят непосредственно в виде порошка или при изготовлении
порошковой смеси в виде лигатуры. Введение меди в количестве 1,0–10 масс. %
увеличивает предел текучести и временное сопротивление материала, но несколько
снижает его пластичность и вязкость. Введение меди существенно повышает сопротивляемость
порошкового материала атмосферной коррозии. Максимальная прочность на разрыв
достигается при массовой доле меди 5–7 %. Медь снижает усадку материала
при спекании. При введении 2–3 % меди спекание происходит практически без
изменения размеров изделия, что позволяет избежать или существенно снизить
объем его последующей механической обработки. Увеличение массовой доли меди
свыше 3 % сопровождается ростом изделий при спекании, рост достигается при
введении 8 % меди.
Широкое
применение нашли железоникелевые и железоникельмедные сплавы. Присадка к
чистому железу 5 % никеля повышает прочность и твердость материала,
оставляя его пластичность практически без изменений. При одновременном
легировании никелем и медью (Ni — 4 % и Си — 2 %) прочность на разрыв
образцов с пористостью 10 % достигает 400–420 МПа, удлинение
—7–8 %, твердость — 120–127 НВ. Такие же образцы, легированные только
2 % меди, показывают следующие свойства при 10 % пористости:
прочность на разрыв — 280–300 МПа, удлинение — 3–4 %, твердость —
100 НВ. Наиболее благоприятное сочетание прочности и пластичности
наблюдается в сплавах содержащих от 1 до 5 % каждого из этих элементов.
В связи со
сравнительно низкой прочностью и твердостью спеченных железных изделий,
основная масса порошковых материалов на базе железа дополнительно легируется
углеродом, под действием которого спеченное железо приобретает способность
закаливаться и во много раз повышать свою твердость и прочность.
Углеродистые
порошковые стали и стальные изделия могут быть получены непосредственным
введением в железный порошок углерода в виде графита, сажи или чугунного
порошка, а также путем науглероживания изделий в процессе спекания или
цементации после спекания. Наиболее распространен метод введения в порошковую
смесь графита. Однако из-за неравномерного распределения графита по объему
смеси при смешивании стальные изделия в спеченном состоянии отличаются
непостоянством свойств и структурных составляющих. Наиболее насыщенные
углеродом микрообъемы аустенита располагаются вблизи графитовых включений, что
способствует появлению в структуре спеченной стали свободного избыточного
цементита и феррита в соотношениях, не соответствующих диаграмме состояния
железо—углерод.
При спекании
железографитовых изделий графит частично выгорает. Для уменьшения выгорания
применяют графитосодержащие засыпки, углеродсодержашие среды. Кроме этого при
приготовлении порошковой смеси в ее состав дополнительно вводят избыточное
количество графита. Так, для получения стальных порошковых изделий с 0,4–0,45 %
углерода при спекании в атмосфере конвертированного природного газа в смесь
необходимо вводить до 0,85 % графита. При применении эндогаза с точно
регулированным потенциалом по углероду содержание графита в смеси должно
превышать заданное на 0,3–035 %. В связи с этим при приготовлении стальных
изделий в порошковую смесь взамен графита зачастую вводят сажистое железо и
порошок из чугунной стружки. Более высокая плотность сажистого железа и порошка
чугунной стружки по сравнению с графитом позволяет получать более однородную
смесь, что обеспечивает стабильность структуры и свойств изделия.
К основным
факторам, определяющим структуру и свойства порошковых углеродистых сталей,
относятся температура, время и среда спекания. При содержании в смеси до
1,0–1,2 % графита оптимальная температура спекания составляет
1150–1200 °С, при содержании графита выше 1,2–1,5 % — 1050–1150 °С.
Время спекания определяется масштабом садки и массой изделия.
Медь в
порошковые стали (табл. 21.6) вводится в виде порошка чистой меди, омедненного
графита, путем пропитки спеченных заготовок. В первых двух случаях при спекании
медь, имея температуру плавления 1083 °С, находится в жидком состоянии и
взаимодействует с железом, образуя твердый раствор замещения на основе
-железа с максимальной концентрацией меди в растворе до 8 %.
Медь понижает
концентрацию углерода в перлите, сдвигая точки S и Е на диаграмме
железо—углерод (см. гл. 1) влево. При содержании в стали до 1 % меди она
способствует усадке при спекании, при дальнейшем повышении ее концентрации
наблюдается рост спеченного изделия. Повышение в порошковых сталях углерода
уменьшает влияние меди на рост спеченного изделия, что достигается образованием
в структуре сплава тройной железомедноуглеродистой фазы, которая расплавляясь
при 1100 °С, вызывает усадку. Введение углерода в железомедные сплавы также
резко повышает прочность порошковых изделий, причем максимальное возрастание
свойств наблюдается при содержании меди до 5–6 % и углерода до 0,3–0,6 %.
Большое влияние на свойства спеченных изделий из медистой стали имеет метод
введения меди. Более высокие свойства достигаются при использовании омедненного
графита.
Введение
никеля в порошковые стали приводит к повышению механических свойств материала,
что связано как с повышением прочности феррита, так и благоприятным
воздействием никеля на состояние межчастичных границ. Никель способствует
«рассасыванию» межчастичных границ, увеличению протяженности металлического
контакта, повышает усадку и плотность изделий.
Отличительной
особенностью хрома является высокая устойчивость его оксидов, температура
диссоциации которых почти достигает температуры плавления чистого хрома. Это
осложняет процесс спекания, особенно когда хром вводится в смесь в виде чистого
порошка хрома. Наличие оксидов затрудняет диффузионные процессы, а само
спекание необходимо производить при высоких температурах в остроосушенных
восстановительных средах (водороде, диссоциированном аммиаке). Поэтому
структура спеченных хромсодержащих сталей отличается повышенной гетерогенностью
и наличием фаз, которые по среднему составу материала не отвечают равновесной
диаграмме его состояния.
К числу
основных характеристик, определяющих возможность перевода изготовления деталей
с традиционных технологий на порошковые, относятся точность производства и
механические свойства порошковых материалов.
Точность
изготовления порошковых деталей определяется в основном точностью прессового
оборудования, стабильностью упругих последействий при холодном прессовании и
объемных изменений при спекании, износом пресс-форм, ростом линейных размеров
полуфабрикатов и изделий при хранении.
Точность
размеров холоднопрессованных брикетов при уплотнении «по давлению»
соответствует для высотных размеров 12–14 квалитетам, для диаметральных — 6–8
квалитетам; при уплотнении с ограничителем для высотных размеров — 12
квалитету, для диаметральных 8–11 квалитетам.
Спекание
приводит к снижению точности изделия на 1–2 квалитета. Для повышения точности
пористых конструкционных изделий применяют калибрование заготовки путем обжатия
в калибровочных пресс-формах при припуске 0,5–1,0 %. Усилие калибрования
составляет 10–25 % усилия холодного прессования. Упругое расширение после
калибрования достигает 0,1 %.
Точность
линейных размеров изделий после горячей штамповки в основном определяется точностью
пресс-инструмента.
Глава 3. ПРИМЕРЫ
ИЗВЛЕЧЕНИЯ ЖЕЛЕЗА ИЗ ПРОИЗВОДСТВЕННЫХ ПРОЦЕССОВ
3.1 Извлечение железа из использованных
автомобильных шин
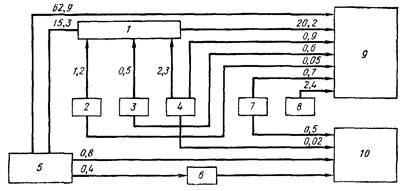
Схема потребления первичных н вторичных железосодержащих материалов при
производстве железа и стали в США в 1976 г. (в миллионах американских тонн железа, 1 т = 907,2 кг)
1 — установка для агломерации железной руды; 2 — колошниковая пыль (доменных печей); 3 — шлак (сталеплавильных печей); 4 — окалина (прокатных станов); 5 — первичная руда, 6 — установка прямого восстановления; 7 — шлаковый скрап (сталеплавильных
печей); 8 — другой скрап
(сталеплавильных печей и прокатных станов); 9 — Доменные печи; 10 — сталеплавильные печи
3.2 Железный порошок из отходов механической
обработки
Как с точки
зрения экономической, так и экологической существует потребность в разработке
процесса прямого превращения отходов механической обработки, таких как мелкая
стружка, в порошок, который может быть использован в порошковой металлургии
железа. По оценке одна только фирма «Форд Мотор Ко» производит на разных
заводах 105 000 т стружки низколегированной стали, которая поступает в продажу
на рынок в качестве скрапа, используемого для загрузки в печь лри некоторых
процессах плавления. Однако применимость такого сырья ограничивается высоким
соотношением его объема к массе и присутствием остатков машинного масла.
Различные
компоненты сплавов, присутствующие в стружке, представляют собой источник
ценных элементов, конечно в том случае, если имеются экономичные методы их
извлечения. В процессе плавления большинство компонентов сплавов окисляется и
теряется со шлаком. Непосредственное превращение опилок в порошок без
промежуточной плавки является более чистым процессом, не загрязняющим
окружающую среду и позволяющим достигать 100 % выделения ценных компонентов.
Этот процесс является также более экономичным, поскольку при существующих
рыночных ценах производство порошка из опилок приводит к получению значительной
прибыли. Однако предпринимавшиеся до сих пор попытки применения железного
порошка, произведенного из опилок, в стандартных процессах порошковой
металлургии не увенчались успехом.
Для решения
указанной проблемы предназначен процесс, который заключается в воздействии
удара на металлургическую стружку при температурах ниже температуры перехода от
пластичного к хрупкому состоянию, в результате чего происходит образование
металлического порошка. Металлическую стружку подвергают воздействию удара на
двух стадиях (например с использованием шаровой мельницы).
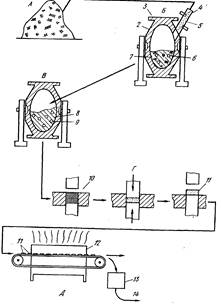
Обычно в качестве сырья используют стружку с отношением площади
поверхности к объему не менее 60 : 1. В качестве сырья может быть также
использован и мелкий скрап—частицы шириной 0,25—2,5 см, толщиной 0,15—0,8 мм и
длиной 2,5—250 см. Стружку, имеющую высокое отношение поверхности к объему, как
правило, в электрической печи не плавят ввиду низкой эффективности этого
процесса.
Можно также перерабатывать скрап с большим размером частиц, хотя при
толщине металла более 0,8 мм возникают существенные трудности при измельчении,
приводящие к повышению капиталовложений в процесс. Используемые частицы скрапа
должны иметь приблизительно одинаковый химический состав; лучше всего
использовать скрап, получаемый в результате обработки одной и той же партии
металла.
Частицы сырья 1 по линии 4 подают в шаровую
мельницу 3 или в другое
устройство для измельчения. При подаче сырья добавляется замораживающий агент
5, например жидкий азот, который разбрызгивается непосредственно на частицы
металла. В результате контакта с жидким азотом металлические частицы мгновенно
замерзают. Подача жидкого азота на сырье осуществляется равномерно на всем его
пути до места измельчения.
При вращении корпуса мельницы 2 железные шары разбивают замороженные частицы металла 7 и измельчают их
в порошок. Этот процесс достаточно длительный. Получаемый порошок 8 обычно состоит из мелкой и более грубой фракций. Частицы в обеих
фракциях имеют конфигурацию зерен или пластинок.
Вторую стадию измельчения как правило также проводят в шаровой
мельнице, но при комнатной температуре. Мелющие элементы 9 представляют собой твердые шары диаметром ~ 1,2 см с антиокислительным железным или медным покрытием. Покрытия должны отвечать следующим
требованиям: 1) иметь меньшую твердость, чем покрываемый порошок, чтобы при
ударе частицы шаровых элементов переходили на порошок; 2) полностью
растворяться в металле, из которого состоят частицы порошка; 3) легко
очищаться; 4) обладать антиокислительными свойствами.
Были проведены эксперименты с использованием цилиндрической камеры 7,5Х
15 см; объем загружаемого порошка составлял ~15 см3, время
измельчения 48 ч. Время и скорость измельчения зависят от объема мельницы,
диаметра железных или медных мелющих элементов и скорости вращения. На второй
стадии измельчения достигаются две цели: создается антиокислительное покрытие
на каждой частице порошка и проводится холодная обработка крупных частиц. При
ударе частицы меди или железа, входящие в состав шаровых мелющих элементов 9, переносятся практически на каждую частицу порошка 8, создавая на ней защитную оболочку. Мелкие частицы порошка при трении о
шаровые элементы соскребают с них медь или железо и таким образом также
приобретают защитную оболочку. Диаметр шаров 9 должен по меньшей мере в 50 раз превышать максимальный размер любой из
частиц криогенного порошка 8.
В результате измельчения также происходит искусственное образование
дефектов кристаллической решетки практически во всех частицах порошка, имеющих
размер более 124 мкм. Измельчение следует проводить таким образом, чтобы
практически каждая крупная частица имела хотя бы один дефект кристаллической
решетки. Эта цель достигается вращением корпуса 2 с такой скоростью, чтобы истирающая сила, действующая на шаровые
элементы, имела определенное заданное значение.
Порошок, полученный на второй стадии измельчения, прессуют обычным
прессом 10 до получения заданной плотности, желательно 6,6 г/см3.
Для этого необходимо прессующее усилие 3,3—3,9 МПа. Наличие медной или железной
оболочки на частицах порошка облегчает прессование. Для получения плотности 6,4
г/м3 при прессовании порошка без покрытия требуется усилие 4,3 МПа;
при прессовании порошка с покрытием при действии той же силы достигается
плотность 6,6 г/см3.
Форма для прессования 11 изготавливается с соответствующим допуском на усадку продукта
прессования. Величина усадки может контролироваться в пределах 0—15 %. Форма для прессования // подается в печь 12 для спекания, где нагревается при высокой температуре, например в
случае криогенного порошка на основе железа до 1100—1150 °С. Температура, до
которой нагревается порошок, должна по меньшей мере находиться в области
пластичности металлических компонентов порошка (обычно нагревание проводят до
температуры спекания). В печи желательно создавать защитную атмосферу,
используя для этой цели инертные газы или газы-восстановители.
При температуре спекания происходит диффузия атомов между частицами
порошка, особенно в местах контакта твердых частиц. Атомы одной частицы
переходят и заполняют дефекты кристаллической решетки в другой контактриуемой с
ней частице. Дефекты кристаллической решетки образуются в результате холодной
обработки на предыдущей стадии. Наличие дефектов увеличивает скорость диффузии
более чем в 100 раз. Подсчитано, что по меньшей мере 60 % общего улучшения
физических свойств в результате спекания обусловлено предварительной
контролируемой холодной обработкой грубых частиц порошка. Повышение скорости
диффузии приводит к увеличению усадки.
Оболочка из железа или меди, создаваемая на частицах порошка,
препятствует окислению содержащихся в них компонентов, в частности таких как
марганец и кремний. При использовании шаровых мельниц со стандартными
параметрами (размеры мельницы и шаров, скорость вращения), как показывают
расчеты, практически каждая частица криогенного порошка будет покрыта
непроницаемой оболочкой из меди или железа. Однако для улучшения свойств
получаемого продукта нет необходимости в том, чтобы эта оболочка была полностью
непроницаемой.
|